
In dieser Fallstudie zeigen wir Ihnen, wie MIDEA, der weltweit größte Hersteller von Großgeräten, Visual Components einsetzte, um die Kapazität und Flexibilität einer High-End-Waschmaschinen-Montagelinie zu verbessern und gleichzeitig die Kosten um 15 % zu senken.
Der weltweit größte Hersteller von großen Haushaltsgeräten
Die 1968 gegründete Midea Group mit Sitz in Südchina ist der weltweit größte Hersteller von großen Haushaltsgeräten und die Nummer 1 bei Luftaufbereitungsprodukten, Luftkühlern, Wasserkochern und Reiskochern. Der Bereich Wäschereigeräte umfasst ein Digital Center, das aus einem Team von Simulationsingenieuren besteht, die für die Überprüfung von Produktdesign, Formen und Ausrüstung sowie Robotik, Logistik und Fabrikimplementierungen verantwortlich sind.
Ein einzigartiges Projekt mit komplexen Anforderungen
Im Jahr 2018 initiierte die Midea Group ein Projekt zur Einführung einer flexiblen Montagelinie zur Herstellung hochwertiger Waschmaschinen. Diese neue Montagelinie sollte am Wuxi-Standort der Wäschereigerätesparte von Midea in Wuxi, China, gebaut werden. Neben der Produktion hochwertiger Waschmaschinen der Spitzenklasse wollte Midea die Linie auch skalierbar machen, um Bestellungen für maßgeschneiderte, maßgeschneiderte Waschmaschinen entgegennehmen zu können.
Das Simulationsteam war dafür verantwortlich, die Designs und das Layout der Montagelinie zu überprüfen und darüber zu berichten, wie es optimiert werden könnte.
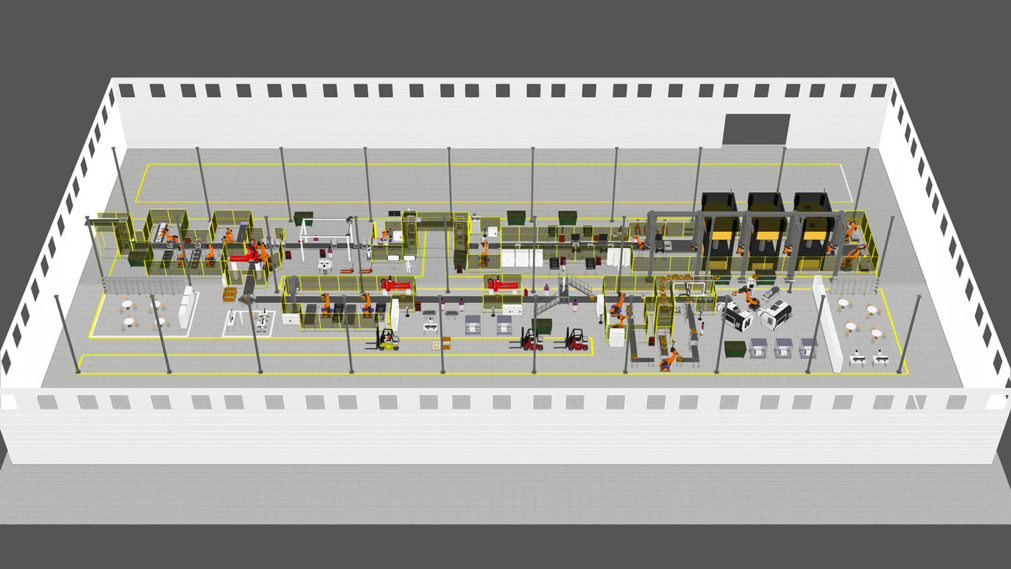
Während die Marge bei diesen High-End-Waschmaschinen im Vergleich zu den Waschmaschinen, die Midea bereits produzierte, höher war, wurden die Produktionsanforderungen immer strenger. Es gab höhere technische Kontrollanforderungen in Bezug auf Materialien, Prozesse und Endprodukte. Aufgrund komplexer Produktions- und Planungsanforderungen musste die Montagelinie intelligentere Fertigungskapazitäten stärker nutzen und flexible Produktionskapazitäten bereitstellen.
Ein besonderer Aspekt dieses Projekts ist die Tatsache, dass diese Montagelinie über 10 verschiedene Produktplattformen sowie über 100 SKUs gleichzeitig produzieren musste. All dies erfolgt nach dem Zufallsprinzip, wobei jedes Produkt seine eigenen Zykluszeiten, Materialanforderungen und Qualitätskontrollverfahren hat. Dabei wurden über 100 Prozesse neu geordnet, die sich völlig von den bisherigen Massenproduktionsmodellen unterschieden.
Mit visuellen Komponenten den Schritt wagen
„Visual Components spielte als umfassendes und professionelles Simulationstool eine sehr wichtige Rolle in diesem Projekt“, sagte Kong Fanshi, Ph.D., Simulationsingenieur im Digital Center-Team. „Früher haben wir drei verschiedene Softwareprogramme verwendet, um 3D-Layouts zu erstellen und Ausrüstung, Logistik und Produktionskapazität zu überprüfen. »
Die Software, mit der Kong und sein Team CAD-Modelle und 3D-Pläne erstellten, war umständlich, insbesondere bei der Modellierung komplexer Maschinen und Anlagen. Die umfangreiche Bibliothek parametrischer und wiederverwendbarer Modelle im E-Katalog von Visual Components machte die Modellerstellung für Kong und sein Team einfach.
Eine weitere Herausforderung war die mangelnde Kompatibilität zwischen ihrer CAD-Software und ihrer Gerätesimulationssoftware. Der Import von Modellen war nicht einfach. Sobald sie in der Lage waren, die Geometrie zu importieren, war die Modellierung der Bewegungen und des Verhaltens der Modelle komplex. Mit ihrem Logistiksimulationstool standen sie vor ähnlichen Herausforderungen; komplexe Programmierung und lange Arbeit. Sie stellten fest, dass die Modellierung von Komponenten und die Erstellung von Prozessen mit Visual Components viel schneller und einfacher war. Ihnen gefiel auch die hochwertige Grafik- und Videowiedergabe.
Nach einer kurzen Testphase nutzte Kongs Team Visual Components als primäres Simulationstool.
„Da die zusätzlichen Vorteile, die Visual Components im Vergleich zu anderer Software bietet, offensichtlich waren, griffen wir nach und nach auf die Software zurück, um die meisten Fälle unserer Projekte zu simulieren“, erklärt Kong.
Kong und sein Team verwenden Visual Components, um die Prozesse und die Produktionsdurchführbarkeit des Layouts für das Waschmaschinenprojekt zu entwerfen, zu optimieren und zu überprüfen sowie um Midea-Managern und Projektbeteiligten das Layout der Montagelinie und die Logistikabläufe dynamisch zu präsentieren.
„Visual Components spielte als umfassendes und professionelles Simulationstool in diesem Projekt eine sehr wichtige Rolle“
Kong Fanshi, Ph.D., ein Simulationsingenieur des Digital Center-Teams der Midea Group
Überprüfung des Designs und der Implementierung der Montagelinie
Um eine High-End-Waschmaschine herzustellen, müssen mehr als 100 Komponenten zusammengebaut werden. Das gesamte Montagelinienprojekt umfasste drei Hauptmontagelinien.
1. Der Panzer
Die Wannenbaugruppe wird gebildet, indem eine Innenwanne in eine hintere Wanne eingesetzt und dann mit einer vorderen Wanne abgedichtet wird
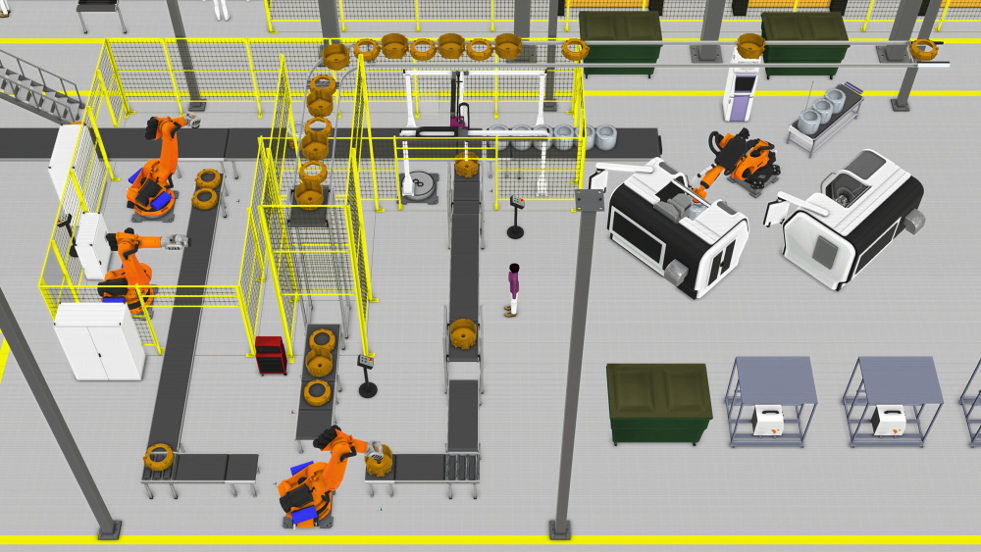
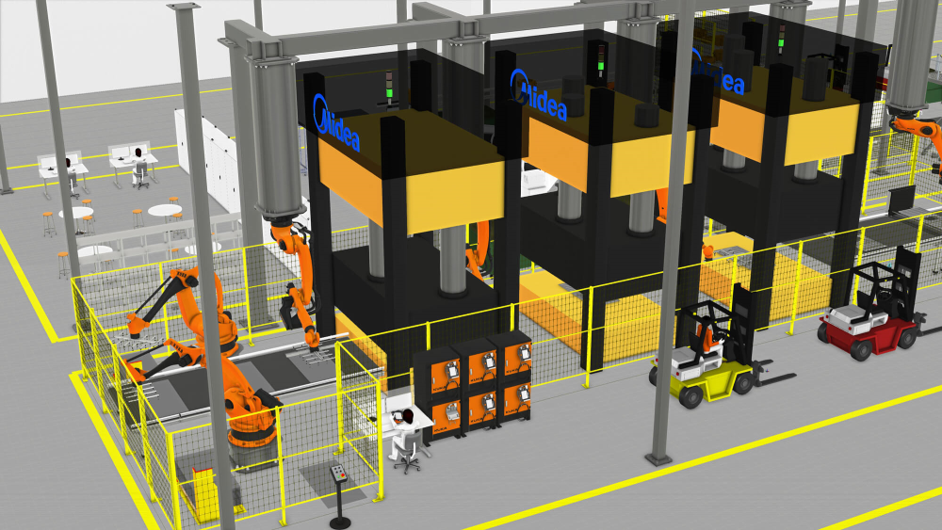
2. Zusammenbau des Kastens
Mit einer horizontalen Stanzmaschine wird aus einer Stahlplatte ein Stahlkasten geformt. Zubehör wie flexible Rohre und Drähte werden an der Box installiert und bilden die Box-Baugruppe.
3. Waschmaschinen zusammenbauen
Die Tank- und Kastenbaugruppen werden zusammen mit dem Ausgleichsblock, dem Bedienfeld, der Tür und der oberen Platte zusammengebaut, um das fertige Produkt zu bilden.
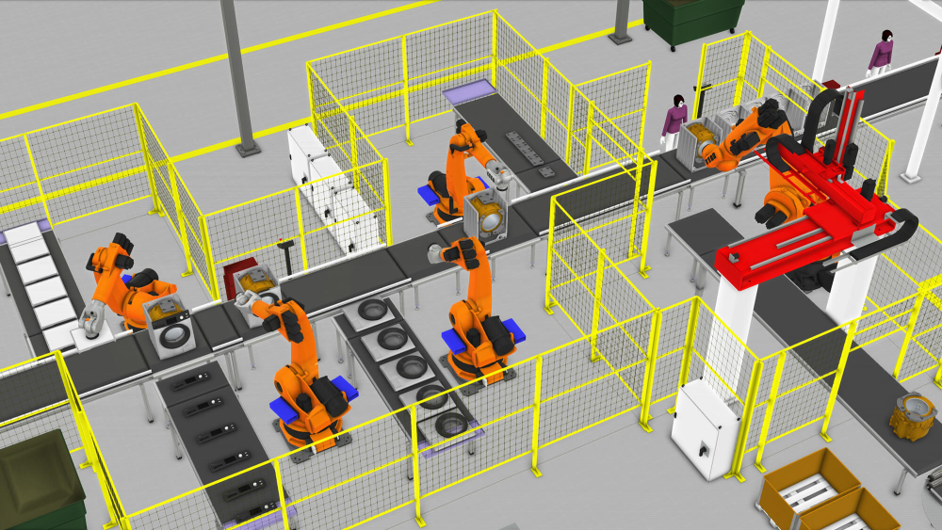
Kong und sein Team standen bei diesem Projekt vor zwei großen Problemen. Die erste bestand darin, Probleme während der Entwurfsphase zu erkennen und zu vermeiden, dass es während der Konstruktion und Implementierung zu Problemen kommt, deren Behebung viel mehr kosten würde. Um dieses Problem zu lösen, war eine Simulation unerlässlich. „Wir verwendeten Simulationen, um unser Design zu überprüfen“, sagt Kong. „Wir haben im Design aktiv nach Risiken gesucht und mithilfe von Simulationen deren Auswirkungen minimiert oder beseitigt. »
Das zweite Problem bestand darin, die beste Lösung zu finden, um den Anforderungen und anspruchsvollen Zielen des Projekts gerecht zu werden. Kongs Team nutzte Simulationen, um sein Design zu optimieren. Beispielsweise führten sie über 100 Simulationsfälle durch, um die beste Zuordnung für Bediener zu finden.
„Die Methoden, mit denen wir diese Herausforderungen bewältigten, waren bisher unvorstellbar“, sagt Kong. „Man konnte die Lösungen nicht einfach finden, ohne die Linie tatsächlich zu bauen und zu testen. »
„Mit Visual Components können wir ganz einfach alle Arten von Lösungen in einer virtuellen Umgebung entwerfen, simulieren und verifizieren. »
Kong Fanshi, Ph.D., ein Simulationsingenieur des Digital Center-Teams der Midea Group
Über die Projektziele hinaus
Mit einem unermüdlichen Fokus auf Optimierung und Verbesserung konnte das Team von Kong erhebliche Verbesserungen und Einsparungen gegenüber dem ursprünglichen Entwurf erzielen, angefangen bei einer effizienteren Nutzung der Grundfläche.
„Wir haben die Grundfläche der Montagelinie um 10 % reduziert und gleichzeitig die Produktionskapazität um 10 % erhöht“, sagt Kong. „Die Kapazität der Linie reichte aus, um 500.000 Einheiten pro Jahr zu produzieren. »
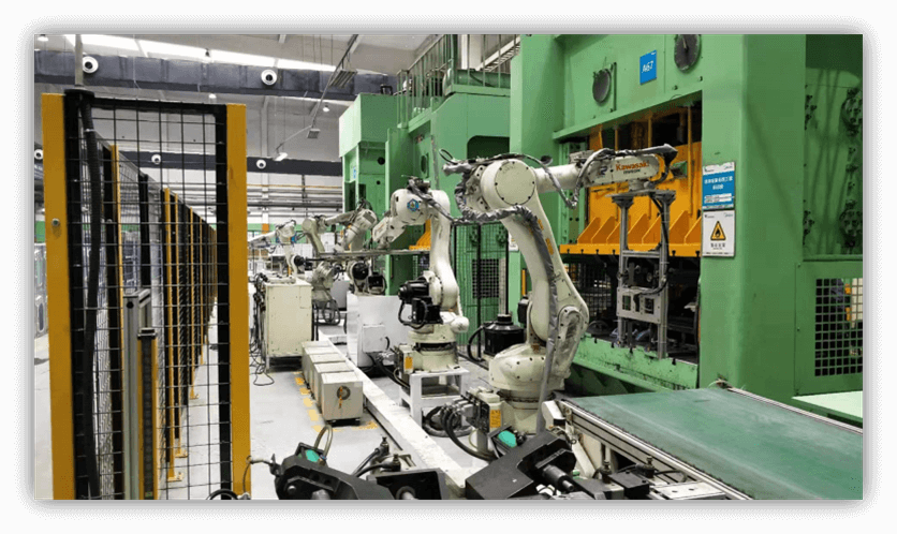
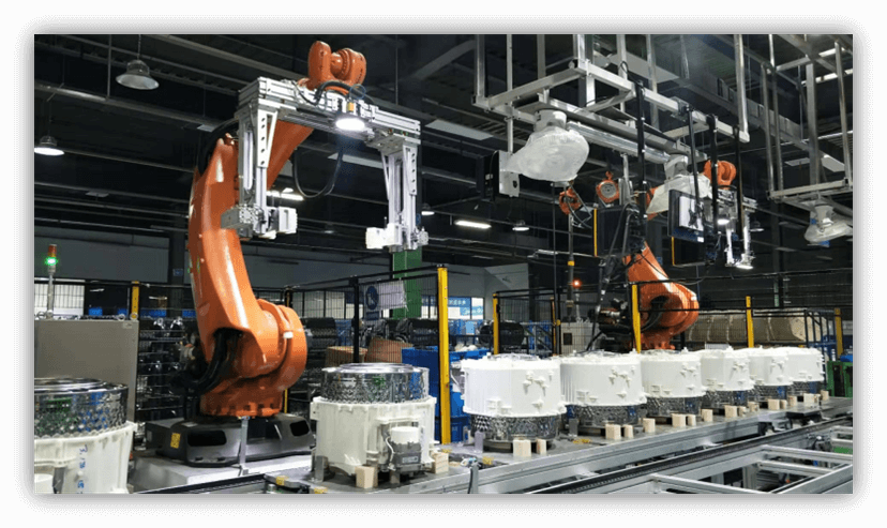
Die Linie war in der Lage, eine Mixed-Flow-Produktion von über 100 SKUs zu ermöglichen, im Vergleich zu den normalen 5–10 SKUs. Trotz des komplexeren Produktionsprozesses war die Linie auch ausgewogener. „Das Gleichgewicht der Linie wurde um 20 % verbessert und erreicht über 90 %“, sagt Kong.
Kong und sein Team konnten außerdem durch eine effizientere Verwaltung und Nutzung des Personals, etwa von Bedienern, Logistikern und Qualitätstechnikern, erhebliche Einsparungen erzielen.
„Wir konnten die Produktqualität verbessern und die Ausschussrate um 1.200 Fehler pro Million bei 120 dpm reduzieren“, sagt Kong.
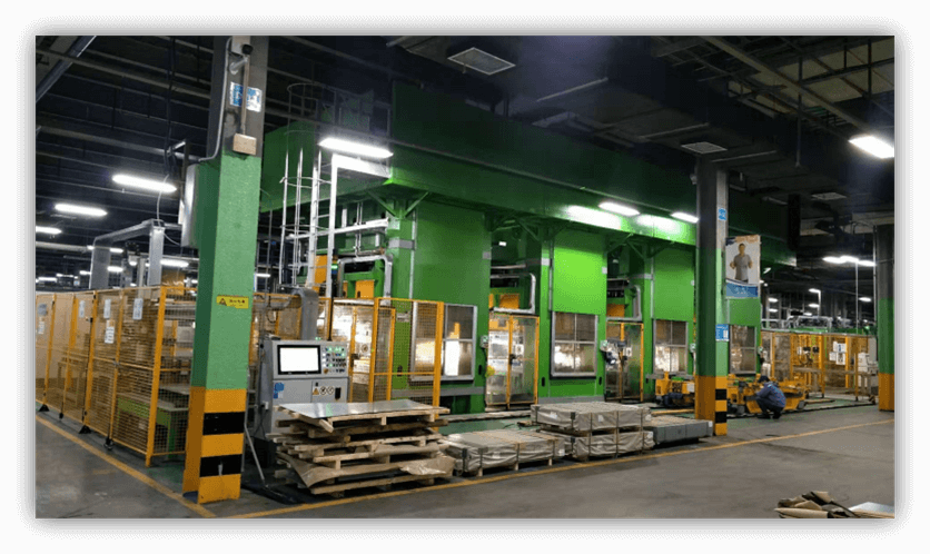
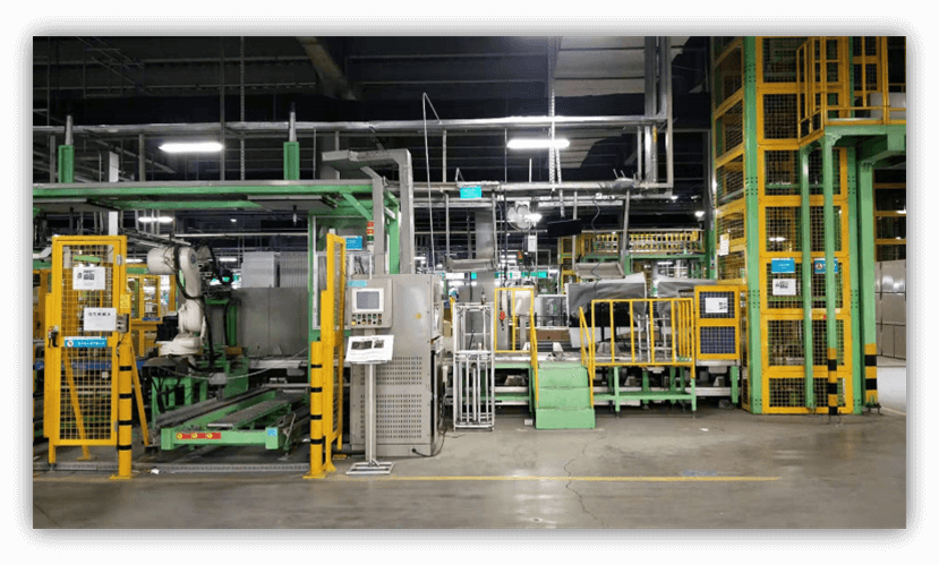
Schließlich konnten Kong und sein Team den Bau und die Installation der kompletten Montagelinie beschleunigen.
„Wir haben die Bauzeit von 15 auf 12 Wochen verkürzt und so eine Einsparung von 20 % gegenüber dem Zeitplan erzielt“, sagt Kong. Die Gesamteinsparungen für das Projekt beliefen sich auf etwa 879.000 US-Dollar.
„Durch den Einsatz von Visual Components konnten wir die Kapitalkosten senken und deutliche Effizienzsteigerungen feststellen“, sagt Kong. „Dadurch konnten die gesamten Projektkosten um etwa 15 % gesenkt werden. »
Nachdem die Linie gebaut war, stellte der Projektmanager einen großen Fernseher in der Nähe der Montagelinie auf, um zu zeigen, welche Auswirkungen Visual Components auf das Projekt hatte. Es spielt kontinuierlich eine Schleife von 3D-Layouts und Simulationsaufzeichnungen ab, die Kongs Team für das Projekt erstellt hat.
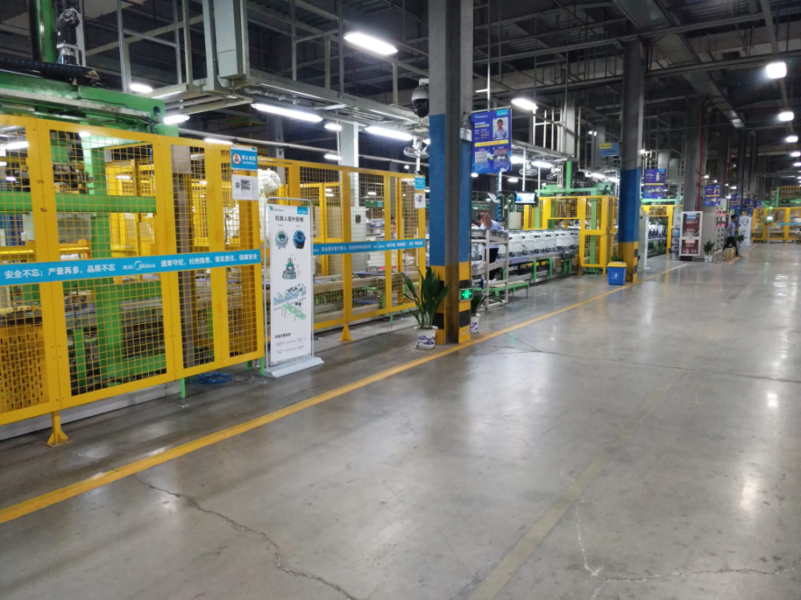
Futuristischer Look mit visuellen Komponenten
Nach dem Erfolg dieses Projekts plant Midea zu prüfen, wie sie Visual Components weiterhin bei der Konstruktion und Inbetriebnahme ihrer Produktionssysteme einsetzen können.
Kong und sein Team wollen die Software weiter an ihre Anwendungen anpassen und eigene Plug-Ins und Add-Ons entwickeln. „Die offene Plattform und Schnittstellen von Visual Components geben uns die Freiheit, das Anwendungsspektrum der Simulationstools zu erweitern“, sagt Kong.
Industrie 4.0 ist eine weitere Priorität für das Team von Kong und Midea. Sie wollen ihre Produktion digitalisieren und ihre Fabriken stärker vernetzen.
„Wir wollen einen digitalen Zwilling unserer Produktion erstellen“, sagt Kong.
„Wir planen, Daten über die Maschinen, die Logistik und die Produktion der Fabrik zu sammeln und diese in Visual Components zu visualisieren. »
„Wir möchten auch untersuchen, wie wir die SPS-Schnittstellen von Visual Components nutzen können, um unsere Produktionsanlagen zu steuern. »
Über Midea
Midea wurde 1968 gegründet und ist der weltweit größte Hersteller von großen Haushaltsgeräten und die Nummer 1 bei Luftbehandlungsprodukten, Luftkühlern, Wasserkochern und Reiskochern. Das Unternehmen ist auf die Bereiche Luftaufbereitung, Kühlung, Wäscherei, große Kochgeräte, große und kleine Küchengeräte, Wassergeräte, Bodenpflege und Beleuchtung spezialisiert.
Midea hat seinen Hauptsitz im Süden Chinas und ist ein wirklich globales Unternehmen mit mehr als 100.000 Mitarbeitern und Niederlassungen in mehr als 200 Ländern. Das Unternehmen verfügt weltweit über 21 Produktionsstandorte und 260 Logistikzentren.
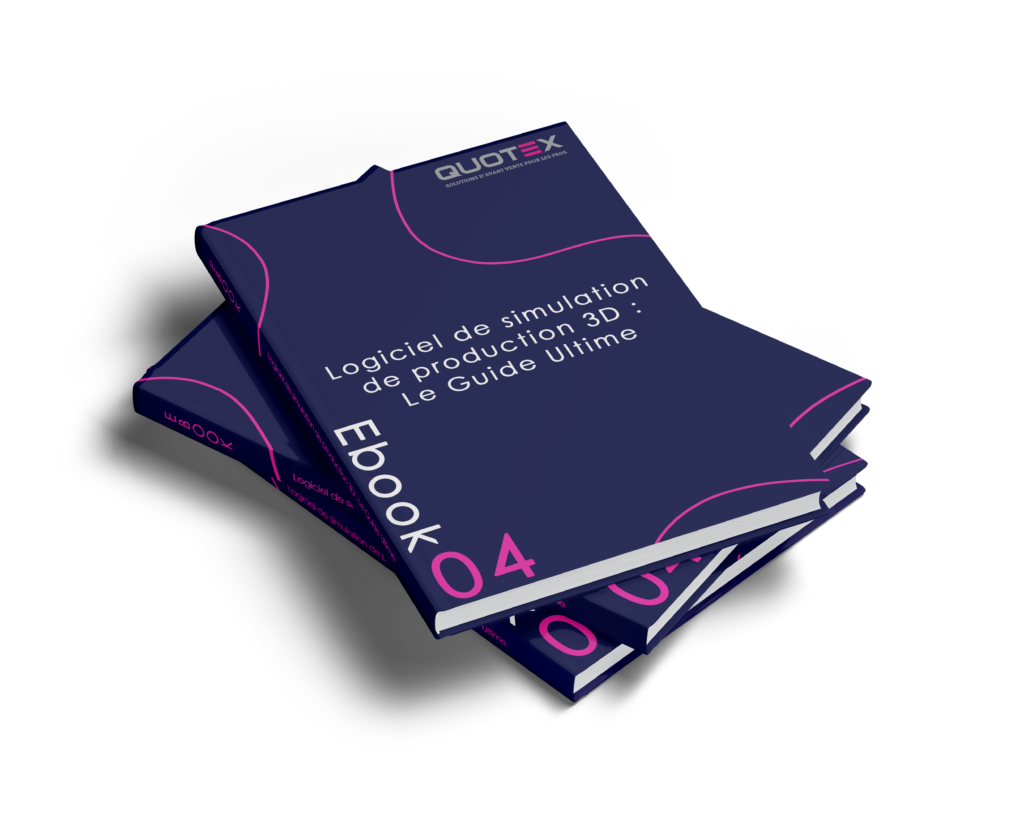