Visual Components OLP: Offline-Programmierung von Robotern
Die Offline-Roboterprogrammierungssoftware der nächsten Generation basierend auf leistungsstarker Technologie von Delfoi Robotics.
Maximieren Sie das Potenzial Ihrer Roboter mit einer schnellen, präzisen und fehlerfreien Programmierlösung.
Akronym: OLP (Offline-Programmierung) – PHL (Offline-Programmierung)
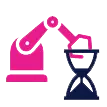
Minimieren Sie die Ausfallzeiten des Roboters
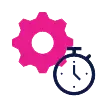
Reduzieren Sie die Programmierzeit
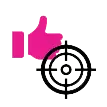
Überlegene, wiederholbare Genauigkeit
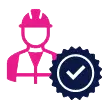
Erhöhen Sie die Sicherheit in der Werkstatt
All-in-One-PHL-Software
Eine Software für alle Prozesse
Programmieren Sie Ihre Roboter für verschiedene Industrieprozesse wie Schweißen, Bearbeiten oder Spritzen mit einer einzigen Software.
Schweißen
Visual Components OLP deckt Prozesse wie Lichtbogenschweißen, WIG-Schweißen, Laserschweißen, Punktschweißen und Nieten ab.
Verfahren
Deckt Prozesse wie Schleifen, Polieren, Polieren, Schleifen, Entgraten, Entgraten, Plasmaschneiden und Laserschneiden ab.
Malen
Umfasst Prozesse wie Nasslackieren, Spritzbeschichten, thermisches Spritzen und Kaltspritzen.
Dadurch können Sie versteckte Probleme erkennen und Investitionsrisiken minimieren.
Kompatibel mit den wichtigsten Marken von Industrierobotern
Robotermarken
17 Marken von Postprozessoren in einem Produkt … Und in Zukunft werden noch weitere hinzukommen!
Controller
Über 40 Versionen von Robotersteuerungen, darunter ältere Roboter und neuere Modelle.
Programmieren Sie Ihre Roboter unabhängig von ihrer Marke oder ihrem Typ. Eliminieren Sie die Notwendigkeit, mehrere Software für verschiedene Marken zu verwenden. Visual Components OLP unterstützt 17 der gängigsten Robotermarken.
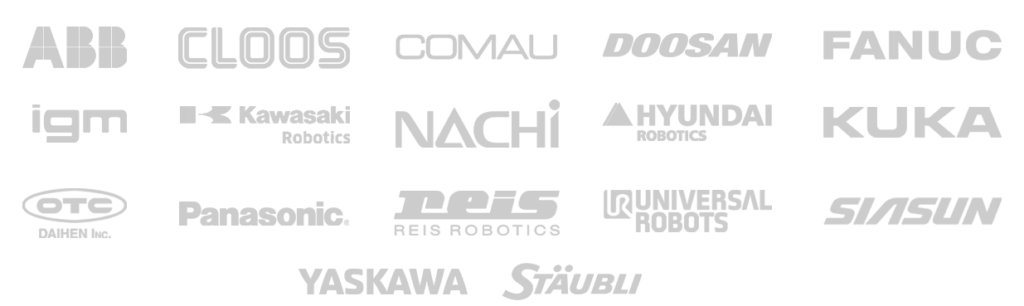
Schnelle, zuverlässige und präzise Programme
Erstellen Sie schnell Programme in virtuellen Roboterzellen, überall auf der Welt.
Lassen Sie die Software Programme validieren und optimieren, bevor Sie sie an die Produktion senden, um kostspielige Fehler zu vermeiden.
Programmierung mit einem Klick
Programmieren Sie Ihre Roboter mit wenigen Klicks
Zeitoptimierung
Speichern Sie Ihre Programme, um sie jederzeit für andere Projekte wiederzuverwenden.
Entdecken Sie die verschiedenen Prozesse, die von Visual Components OLP verwaltet werden, im Video
Verschiedene OLP-Prozesse
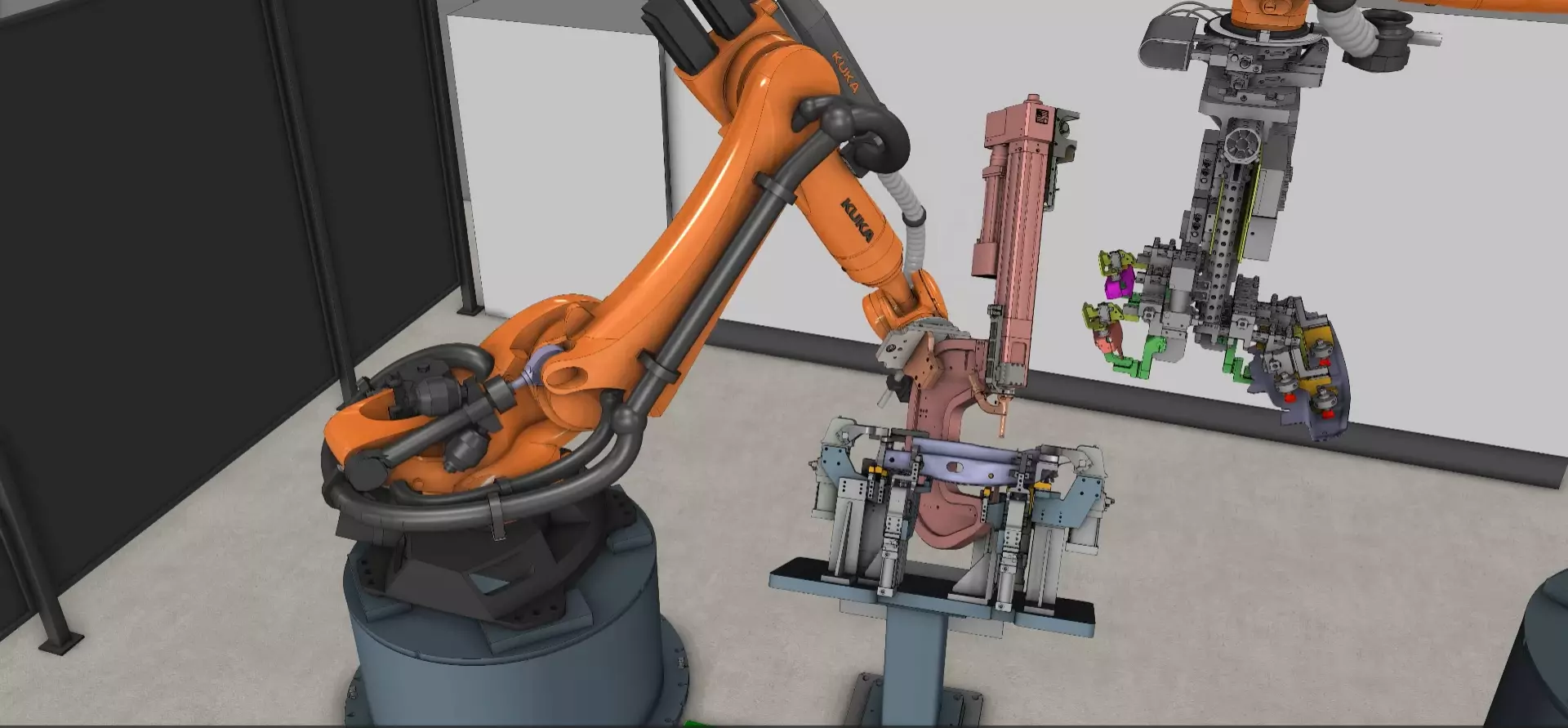
0:11
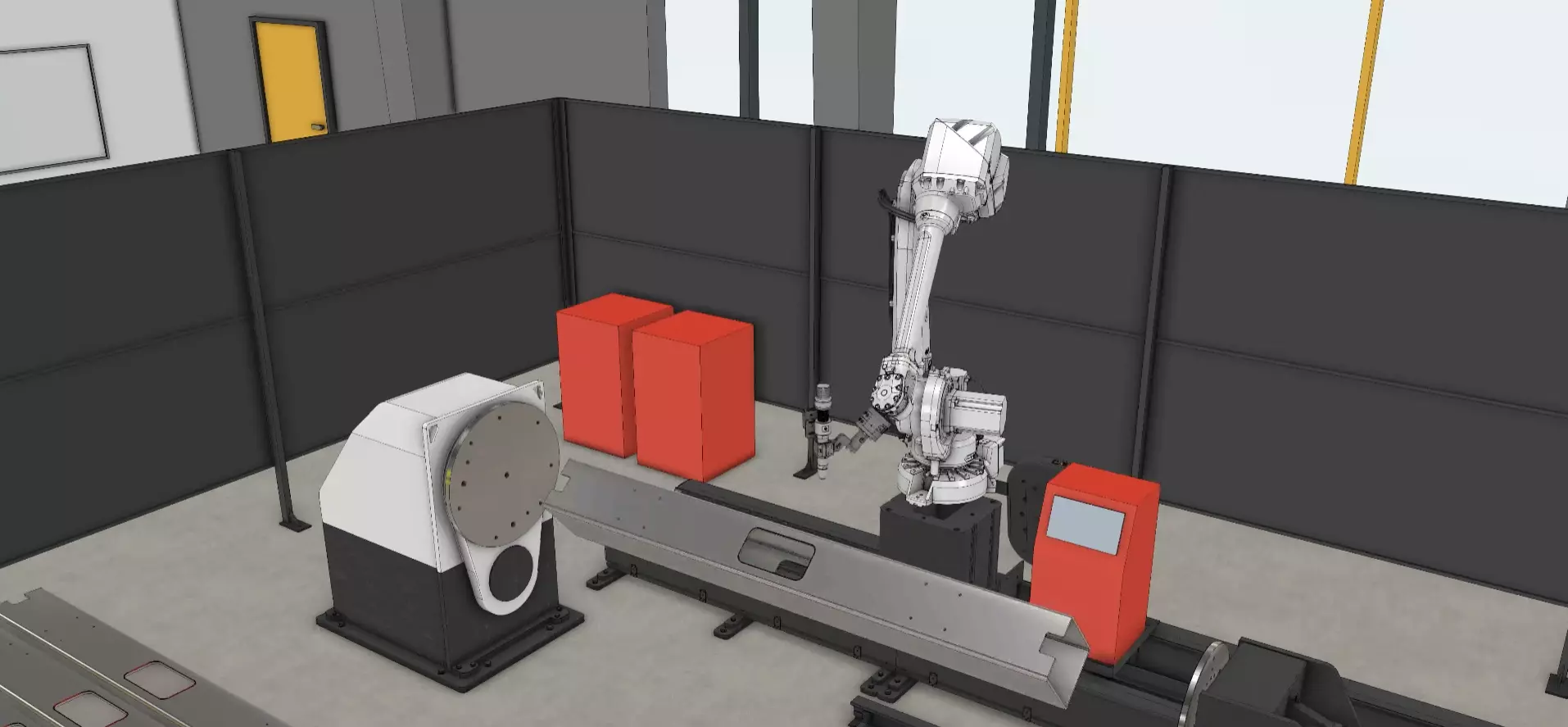
0:11
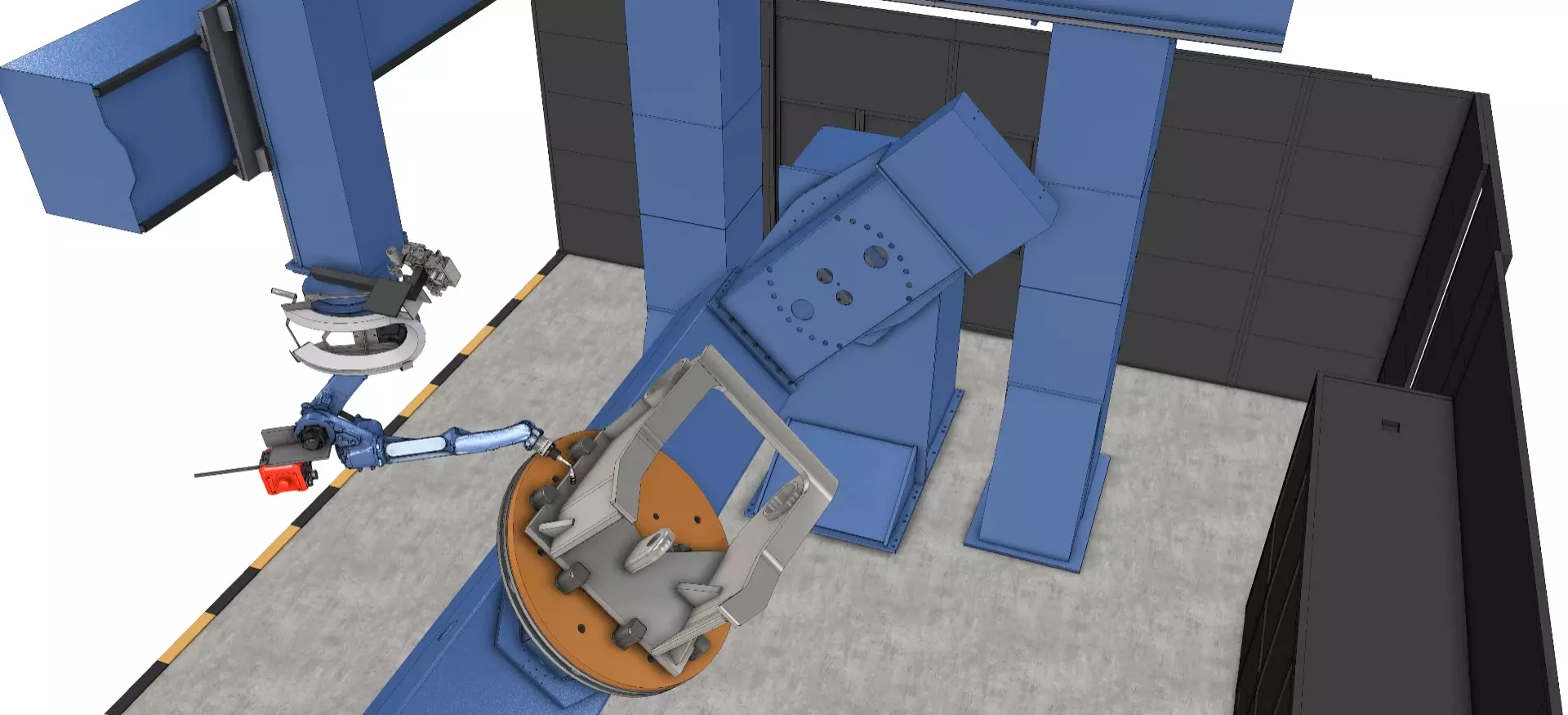
0:10
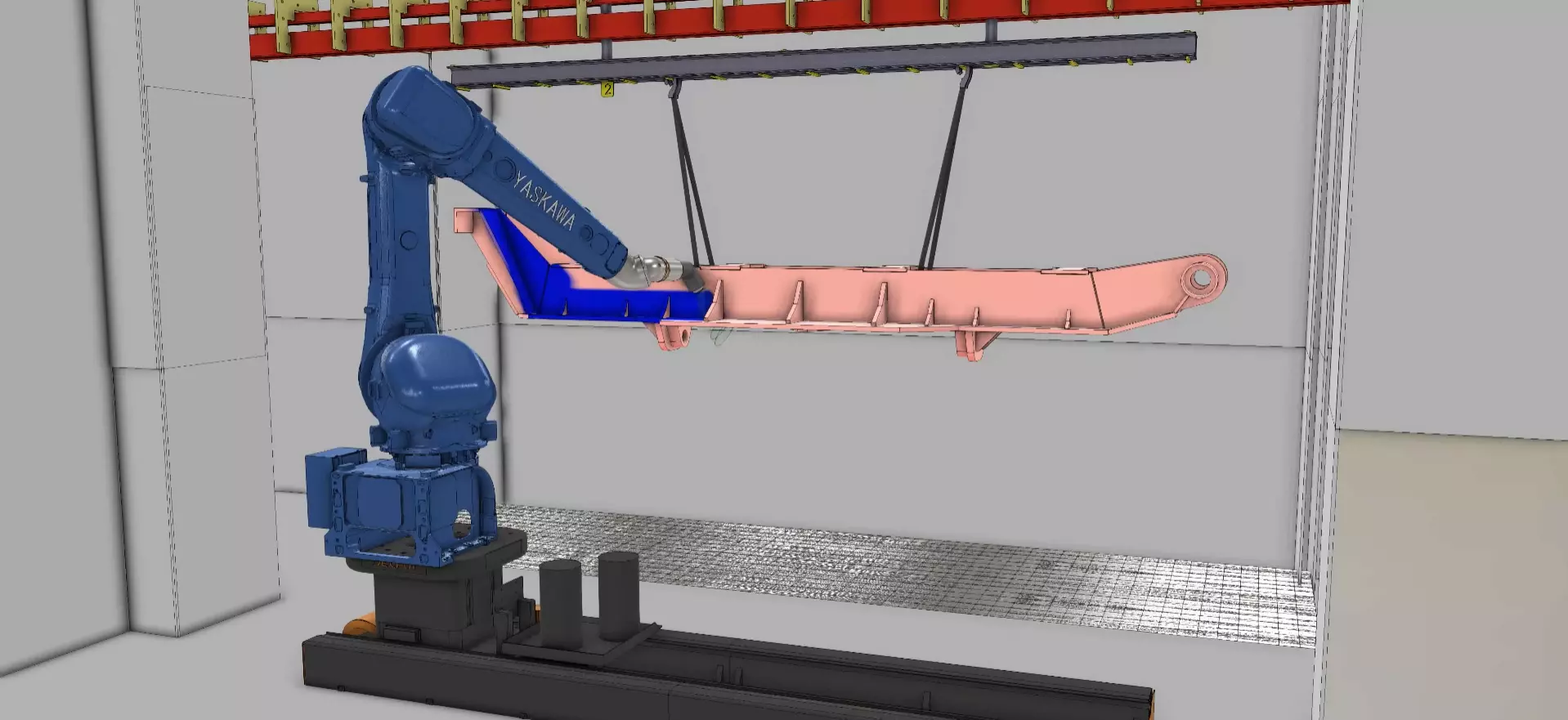
0.14
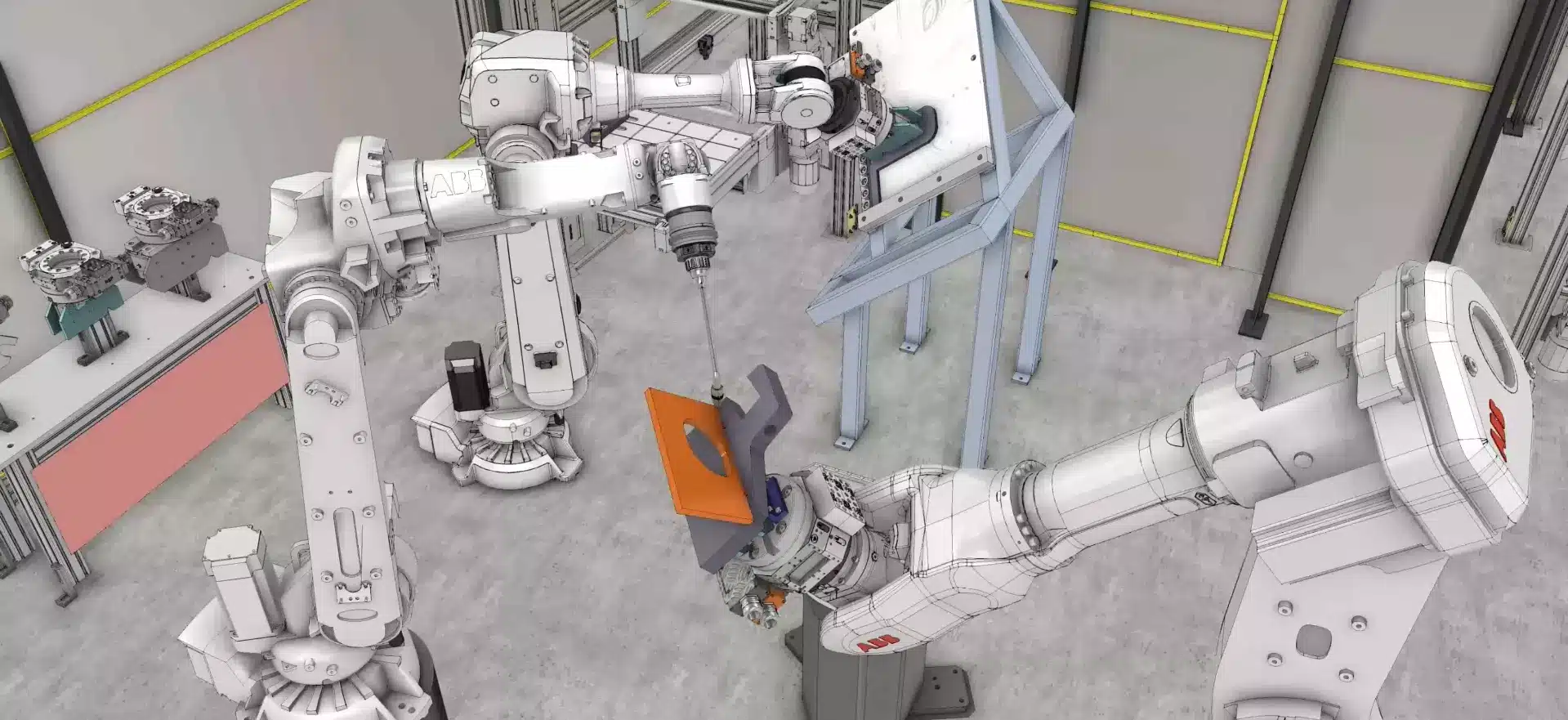
0.14
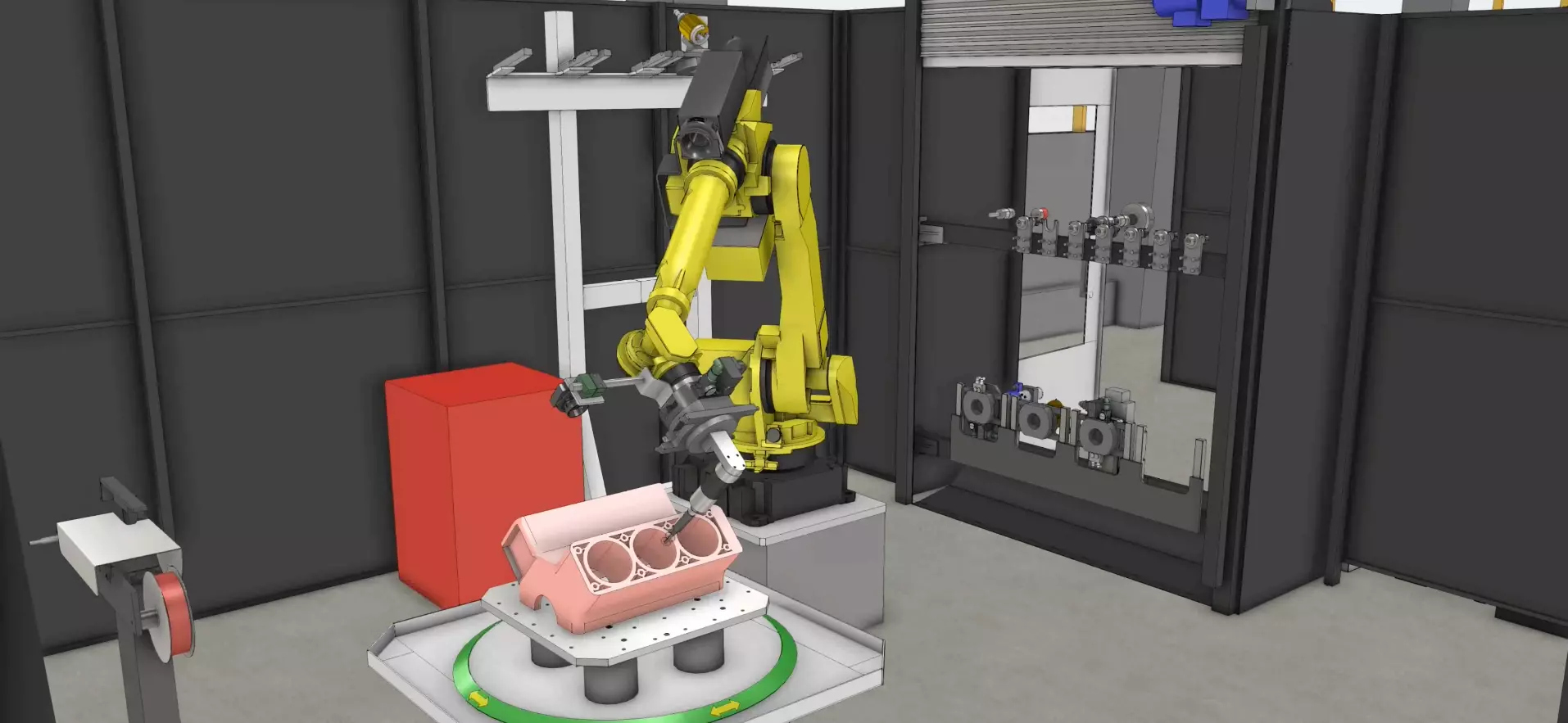
0.11
Während eines 30-minütigen Videos zieht unser fachkundiger Integrator von VISUAL COMPONENTS eine Bestandsaufnahme Ihrer Liniendesignpraktiken und schätzt die Zeit ein, die Sie dank Visual Components einsparen könnten
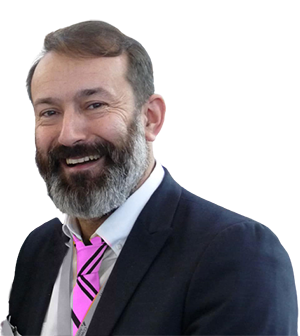
Häufig gestellte Fragen zur Offline-Roboterprogrammierung
Offline-Roboterprogrammierung (PHL oder OLP auf Englisch) ist eine Methode zur Generierung von Roboterprogrammen in Computersoftware (virtueller Umgebung) auf der Grundlage von 3D-CAD-Daten.
Sobald das Roboterprogramm in der Software generiert und verifiziert ist, kann es auf den physischen Roboter heruntergeladen werden.
Stellen wir uns vor, dass ein Roboter so programmiert ist, dass er ein rundes Teil an ein Metallteil schweißt.
Der Roboter muss den Schweißbrenner in einem 3D-Bogen um den Umfang des Teils bewegen und dabei eine präzise Ausrichtung relativ zur Oberfläche beibehalten. Sie können dies tun, indem Sie Punkte mithilfe eines Anhängers einlernen, allerdings benötigen Sie dafür eine große Anzahl an Punkten und es wird lange dauern. Der Abstand zwischen den Brennern wird höchstwahrscheinlich variieren, ebenso wie die Ausrichtung des Brenners. Darüber hinaus steht die Roboterzelle erst dann für die Produktion zur Verfügung, wenn Sie die Programmierung abgeschlossen haben. Dieser Shutdown kann Tage oder sogar Wochen dauern. Mit PHL ist es viel einfacher, das Roboterprogramm zu erstellen. Importieren Sie eine CAD-Datei der Schweißzelle in die OLP-Software und zeigen Sie den Weg an, den der Brenner nehmen soll. Nach Abschluss generiert die Software das Roboterprogramm und prüft auf mögliche Kollisionen. Nach der Überprüfung wird das Programm in die Robotersteuerung heruntergeladen, zur doppelten Überprüfung einmal mit niedriger Geschwindigkeit ausgeführt und die Zelle ist dann bereit, ihre Arbeit fortzusetzen.
Jede Roboteranwendung ist ein Kandidat für PHL;
Die einzige Voraussetzung besteht darin, über digitale Modelle der Arbeitszelle, der Teile, Werkzeuge und Befestigungen zu verfügen. (Heutzutage wird alles im CAD entworfen, was kein Problem darstellen sollte.) Allerdings sind die Vorteile größer, da Roboterpfade komplexer werden und mehr Punkte eingelernt werden müssen. Unter Berücksichtigung dieser Punkte sind hier einige der besten Anwendungsfälle für PHL:
Schweißen – Zugang und Ausrichtung sind besondere Herausforderungen, die PHL angeht, und komplexe Schweißnähte können eine große Anzahl von Punkten erfordern.
Beschichten (Lackieren) – Wie beim Schweißen kommt es auch hier auf die Ausrichtung, die Lackdicke und den Abstand an, damit alle Bereiche optimal erreicht und lackiert werden können.
Entfernung – Bei vielen Montagevorgängen müssen lange, komplexe Klebstoffraupen entfernt werden: Mit PHL können Werkzeugwege schnell und offline mit gleichbleibender Qualität erstellt werden.
(Oberflächen-)Bearbeitung – Anwendungen wie Strahlen und Entgraten erfordern oft lange, komplexe Wege, die eine große Anzahl von Punkten erfordern.
Montageanwendungen (ohne Vorrichtung) – Greif- und Einlegebewegungen erfordern eine präzise Steuerung der Ausrichtung des Greifers, was mit PHL auf einem höheren Niveau möglich ist.
Materialtransportanwendungen – PHL ermöglicht es dem Programmierer, den schnellsten Abstand zwischen zwei Standorten zu bestimmen, der nicht immer der offensichtlichste Weg ist.
Schneiden – Plasma-, Laser- oder Wasserstrahlschneiden kann für Standardteile funktionieren, aber für komplexe Geometrien werden Roboter mit präzisen Schnittmustern benötigt, die mit PHL generiert werden können
Hersteller, die OLP-Software verwenden, berichten von zahlreichen Vorteilen:
Keine Ausfallzeiten des Roboters.
Die Programmierzeit kann um bis zu 80 % reduziert und die Roboterauslastung um bis zu 95 % erhöht werden, was die Produktivität der Programmierer steigert und die Ausfallzeiten der Zelle reduziert.
Schnelle Rüstzeiten
Es wird weniger Zeit benötigt, um ein neues Produkt in die Produktion zu bringen – die Programmierung erfolgt gleichzeitig und nicht nacheinander.
Erhöhte Sicherheit
Reduziertes Unfall- und Verletzungsrisiko
Höhere, wiederholbare Qualität
Roboterprogramme werden besser optimiert (kürzere Zykluszeiten, höhere Präzision und Konsistenz), was zu einer höheren, wiederholbaren Produktionsqualität führt.
Unabhängig von Robotermarke und -prozess
Unabhängig von der Robotermarke oder dem Prozesstyp kann die fortschrittliche OLP-Software alle Anwendungen abdecken.
Keine Überraschungen mehr.
Last-Minute-Änderungen an Befestigungselementen und Werkzeugen werden vermieden.
Obwohl jeder Hersteller, der Roboter einsetzt, von PHL profitieren kann, werden die größten Vorteile bei kleinen Losgrößen und kurzen Produktionszyklen erzielt.
Das Problem besteht darin, dass bei der Programmierung des Roboters häufige Änderungen und Anpassungen die Betriebszeit und Betriebsstunden verkürzen.
Bei Visual Components OLP werden Programme jedoch virtuell getestet und auf die Roboter hochgeladen, während die physischen Aspekte der Zelle (Befestigungselemente, Klemmen usw.) geändert werden.
Prudence schlägt vor, den Roboter einem Zyklus mit niedriger Geschwindigkeit zu unterziehen, um ihn auf Kollisionen zu prüfen. Danach ist die Zelle bereit, die Produktion wieder aufzunehmen. Darüber hinaus werden alle konstruktionsbezogenen Probleme in der Dokumentation oder den Modellen im Voraus identifiziert und können an andere Teams kommuniziert und ohne Verlust von Produktionszeit gelöst werden.
Die Alternative zur Verwendung von OLP besteht darin, direkt am Roboter zu programmieren.
Diese Lösung wirft mindestens drei Probleme auf: 1. Risiko einer Projektverzögerung und zusätzlicher Kosten
2. Sicherheitsbedenken
3. Verlust der Produktionskapazität
Bei der Programmierung am Roboter besteht ein erhebliches Risiko von Projektverzögerungen.
Zu diesem Zeitpunkt sind alle Werkzeuge und Vorrichtungen entworfen, gebaut und installiert. Förderbänder oder andere Handhabungsgeräte sind vorhanden und die Teile sind einsatzbereit. Erst jetzt kann der Programmierer mit dem Teachen der Roboterpunkte beginnen. Es ist fast sicher, dass Probleme auftreten. Möglicherweise kann der Roboter einen bestimmten Ort nicht erreichen, die Teile befinden sich möglicherweise am falschen Ort oder die angestrebte Zykluszeit ist möglicherweise nicht erreichbar.
In all diesen Fällen besteht die einzige Lösung darin, die Problempunkte der Zelle neu zu definieren.
Dies verzögert zwangsläufig den Produktionsstart teilweise um mehrere Wochen und führt zu erheblichen Mehrkosten. Das Erlernen von Punkten mithilfe eines Anhängers erfordert häufig, dass der Programmierer die Zelle betritt: Dies ist manchmal die einzige Möglichkeit, zu sehen, wohin sich das Werkzeug bewegt, oder um nach Kollisionen zu suchen.
Das Versetzen des Roboters in den „Lernmodus“ sollte seine Sicherheit gewährleisten, es besteht jedoch immer die Gefahr unerwarteter Bewegungen, entweder durch den Roboter selbst oder durch einen der anderen Mechanismen in der Zelle. Während der Programmierer schließlich Punkte innerhalb der Arbeitszelle lernt, kann der Roboter nichts anderes tun. Dies ist unproduktive Zeit, bis der Programmierer fertig ist und das Programm getestet ist. Und selbst die besten Programmierer neigen dazu, den Zeitaufwand für die Aufgabe zu unterschätzen!