
En este estudio de caso, le mostraremos cómo MIDEA, el mayor productor de electrodomésticos importantes del mundo, utilizó Visual Components para mejorar la capacidad y la flexibilidad de una línea de ensamblaje de lavadoras de alta gama y al mismo tiempo reducir los costos en un 15 %.
El mayor productor mundial de electrodomésticos importantes
Fundado en 1968 y con sede en el sur de China, Midea Group es el mayor productor mundial de grandes electrodomésticos y el número uno en productos de tratamiento de aire, refrigeradores de aire, hervidores y ollas arroceras. La división de electrodomésticos para lavandería incluye un Centro Digital, el cual está conformado por un equipo de ingenieros de simulación que se encargan de verificar el diseño de productos, moldes y equipos, así como la robótica, logística e implementaciones de fábricas.
Un proyecto único con solicitudes complejas
En 2018, Midea Group inició un proyecto para poner en marcha una línea de montaje flexible que produciría lavadoras de alta gama. Esta nueva línea de montaje se iba a construir en las instalaciones de Wuxi de la división de electrodomésticos de lavandería de Midea en Wuxi, China. Además de producir lavadoras de alta calidad y gama alta, Midea quería que la línea fuera escalable para dar cabida a pedidos de lavadoras personalizadas.
El equipo de simulación fue responsable de verificar los diseños y la disposición de la línea de montaje e informar sobre cómo podría optimizarse.
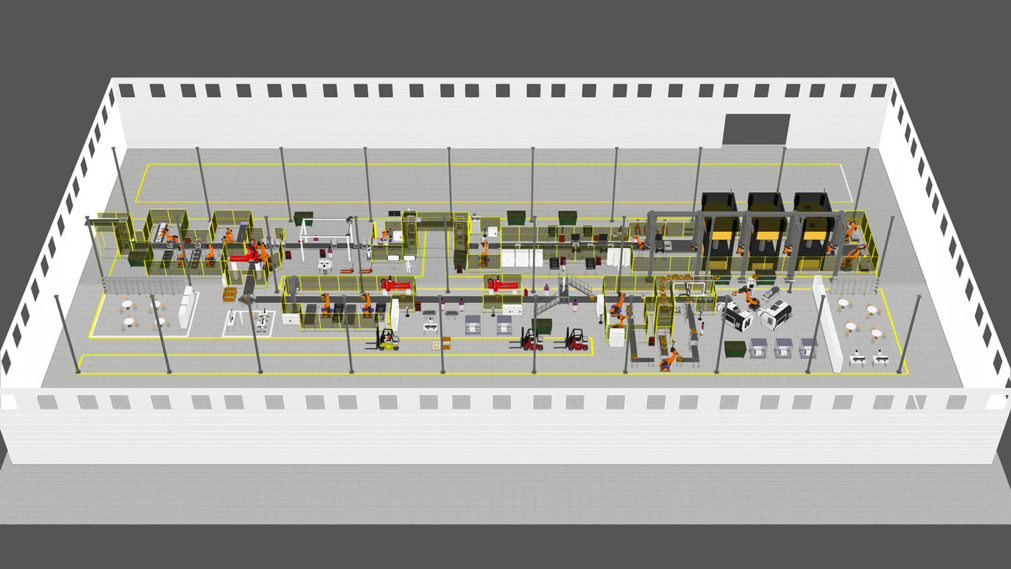
Si bien el margen de estas lavadoras de alta gama era mayor en comparación con las lavadoras que Midea ya producía, los requisitos de producción se estaban volviendo más estrictos. Hubo mayores requisitos de control técnico en términos de materiales, procesos y productos terminados. Debido a los complejos requisitos de producción y planificación, la línea de montaje necesitaba hacer un mayor uso de las capacidades de fabricación inteligente y proporcionar una capacidad de producción flexible.
Un aspecto específico de este proyecto es el hecho de que esta línea de montaje necesitaba producir más de 10 plataformas de productos diferentes, así como más de 100 SKU al mismo tiempo. Todo esto de forma aleatoria, teniendo cada producto sus propios tiempos de ciclo, requisitos de materiales y procedimientos de control de calidad. Esto implicó reorganizar más de 100 procesos, que eran completamente diferentes de los modelos de producción en masa utilizados hasta ahora.
Dando el paso con componentes visuales
"Como herramienta de simulación integral y profesional, Visual Components jugó un papel muy importante en este proyecto", dijo Kong Fanshi, Ph.D, ingeniero de simulación del equipo del Centro Digital. “Anteriormente, usábamos tres programas de software diferentes para crear diseños 3D y verificar el equipo, la logística y la capacidad de producción. »
El software que Kong y su equipo utilizaron para crear modelos CAD y planos 3D era engorroso, especialmente al modelar maquinaria y equipos complejos. La extensa biblioteca de modelos paramétricos y reutilizables incluida en el catálogo electrónico de Componentes Visuales simplificó la creación de modelos para Kong y su equipo.
Otro desafío al que se enfrentaron fue la falta de compatibilidad entre su software CAD y su software de simulación de equipos; Importar modelos no fue fácil. Una vez que pudieron importar la geometría, modelar los movimientos y el comportamiento de los modelos fue complejo. Experimentaron desafíos similares con su herramienta de simulación logística; programación compleja y largo trabajo. Descubrieron que modelar componentes y crear procesos con componentes visuales era mucho más rápido y sencillo. También les gustaron los gráficos de alta calidad y la reproducción de vídeo.
Después de un breve período de prueba, el equipo de Kong estaba utilizando Visual Components como su principal herramienta de simulación.
"Como las ventajas adicionales que ofrecían Visual Components en comparación con otro software eran obvias, gradualmente recurrimos al software para simular la mayoría de los casos de nuestros proyectos", explica Kong.
Kong y su equipo utilizan Visual Components para diseñar, optimizar y verificar los procesos y la viabilidad de producción del diseño del proyecto de la lavadora, así como para presentar dinámicamente el diseño de la línea de montaje y los flujos logísticos a los gerentes de Midea y a las partes interesadas del proyecto.
"Como herramienta de simulación integral y profesional, Visual Components jugó un papel muy importante en este proyecto".
Kong Fanshi, Ph.D, ingeniero de simulación del equipo del Centro Digital, Grupo Midea
Verificación del Diseño e Implementación de la Línea de Montaje
Se deben ensamblar más de 100 componentes para producir una lavadora de alta gama. Todo el proyecto de la línea de montaje incluyó 3 líneas de montaje principales.
1. El tanque
El conjunto de la tina se forma colocando una tina interior en una tina trasera y luego sellándola con una tina delantera.
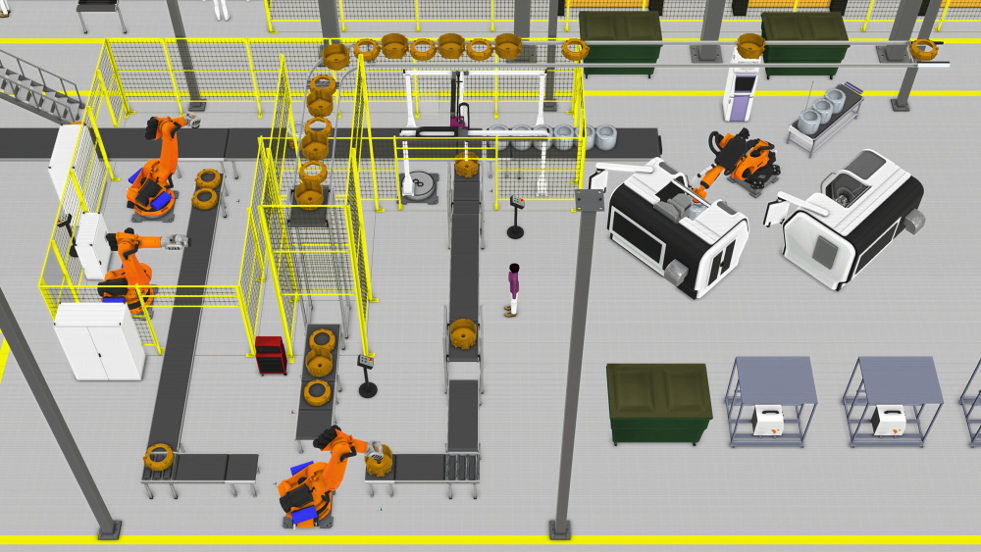
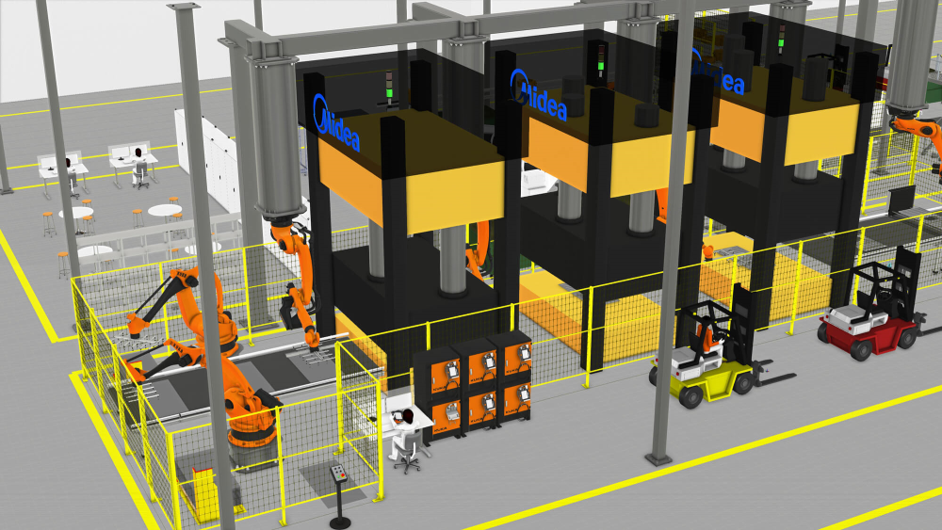
2. Montaje de caja
Una placa de acero se convierte en una caja de acero utilizando una punzonadora horizontal. Accesorios como tubos flexibles y cables se instalan en la caja, formando el conjunto de la caja.
3. Montaje de lavadoras
Los conjuntos de tanque y caja, junto con el bloque de equilibrio, el panel de control, la puerta y la placa superior, se ensamblan para formar el producto terminado.
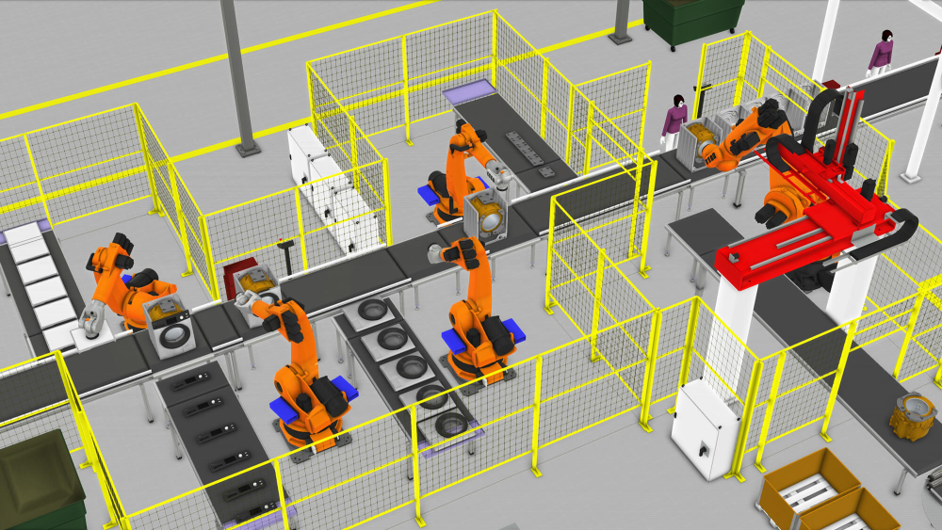
Kong y su equipo enfrentaron dos problemas importantes con este proyecto. El primero era cómo detectar problemas durante la fase de diseño y evitar encontrarse con problemas durante la construcción e implementación, cuando costaría mucho más solucionarlos. La simulación fue esencial para superar este problema. "Utilizamos la simulación para verificar nuestro diseño", dice Kong. “Buscamos activamente riesgos en el diseño y utilizamos la simulación para minimizar o eliminar sus efectos. »
El segundo problema era encontrar la mejor solución para cumplir con los requisitos y objetivos agresivos del proyecto. El equipo de Kong utilizó la simulación para optimizar su diseño. Por ejemplo, ejecutaron más de 100 casos de simulación para encontrar la mejor asignación para los operadores.
"Los métodos que utilizamos para superar estos desafíos eran antes inimaginables", dice Kong. “No era fácil encontrar soluciones sin construir y probar la línea. »
“Con Visual Components, podemos diseñar, simular y verificar fácilmente todo tipo de soluciones en un entorno virtual. »
Kong Fanshi, Ph.D, ingeniero de simulación del equipo del Centro Digital, Grupo Midea
Más allá de los objetivos del proyecto
Con un enfoque incesante en la optimización y la mejora, el equipo de Kong pudo lograr mejoras y ahorros significativos con respecto a su diseño original, comenzando con un uso más eficiente del espacio.
"Redujimos el espacio de la línea de montaje en un 10% y al mismo tiempo aumentamos la capacidad de producción en un 10%", dice Kong. “La línea tenía capacidad suficiente para producir 500.000 unidades al año. »
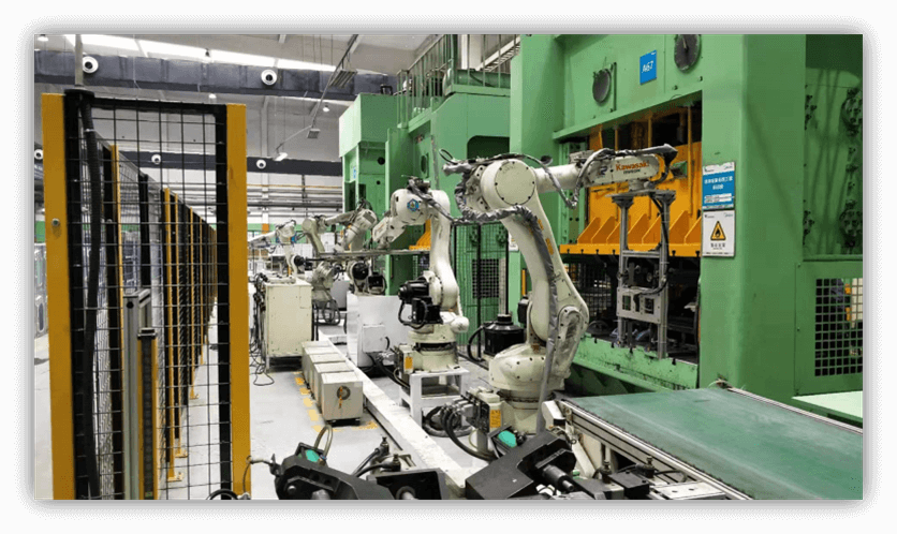
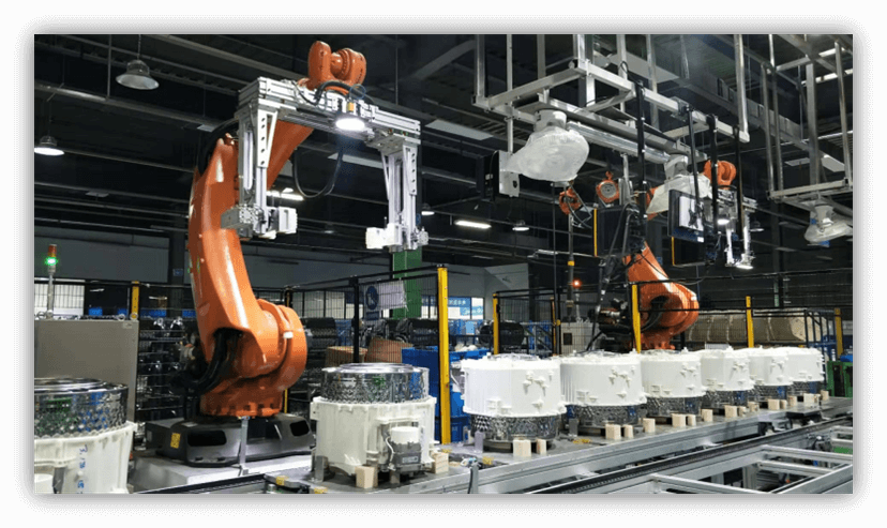
La línea pudo acomodar una producción de flujo mixto de más de 100 SKU, en comparación con las 5-10 SKU normales. A pesar del proceso de producción más complejo, la línea también estaba más equilibrada. "El saldo de la línea ha mejorado en un 20%, llegando a más del 90%", afirma Kong.
Kong y su equipo también pudieron lograr ahorros significativos mediante una gestión y utilización más eficiente del personal, como operadores, logísticos y técnicos de calidad.
"Pudimos mejorar la calidad del producto, reduciendo la tasa de rechazo en 1200 defectos por millón a 120 dpm", dice Kong.
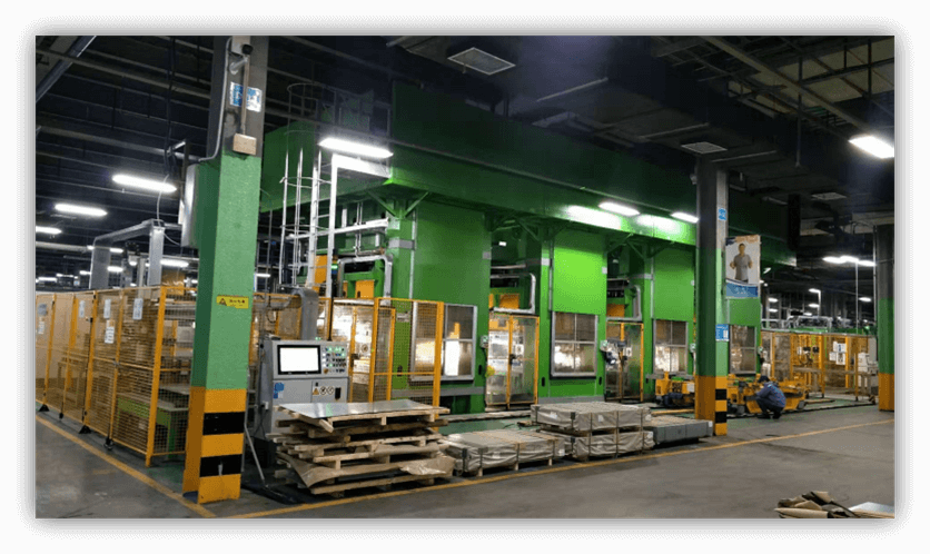
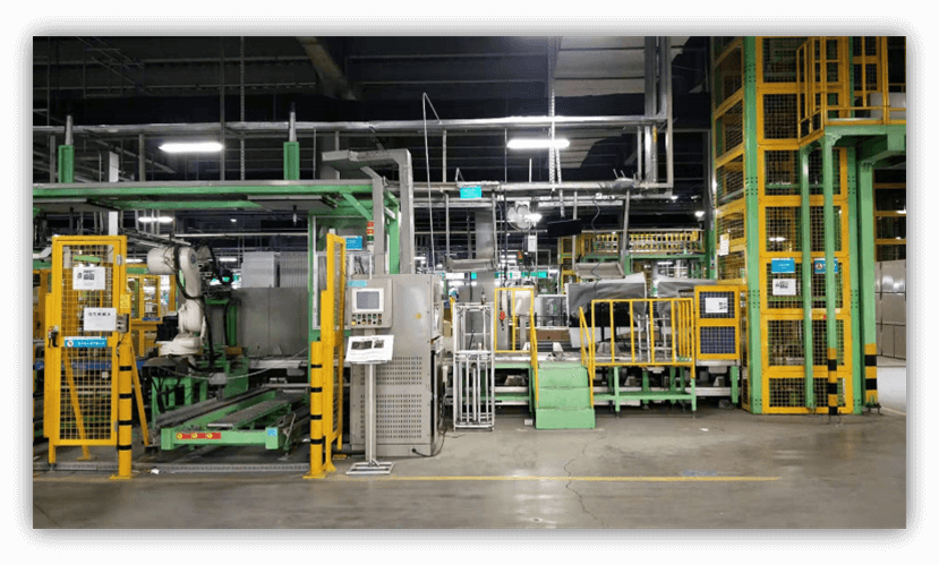
Finalmente, Kong y su equipo pudieron acelerar la construcción e instalación de la línea de montaje completa.
"Redujimos el período de construcción de 15 a 12 semanas, logrando un ahorro del 20% en el cronograma", dice Kong. Los ahorros totales para el proyecto fueron aproximadamente $879,000.
"Al utilizar Visual Components, pudimos reducir los costos de capital y encontrar mejoras significativas en la eficiencia", dice Kong. “Como resultado, los costos totales del proyecto se redujeron en aproximadamente un 15%. »
Una vez construida la línea, el director del proyecto instaló un televisor grande cerca de la línea de montaje para mostrar cómo los componentes visuales impactaron el proyecto. Reproduce continuamente un bucle de diseños 3D y grabaciones de simulación que el equipo de Kong creó para el proyecto.
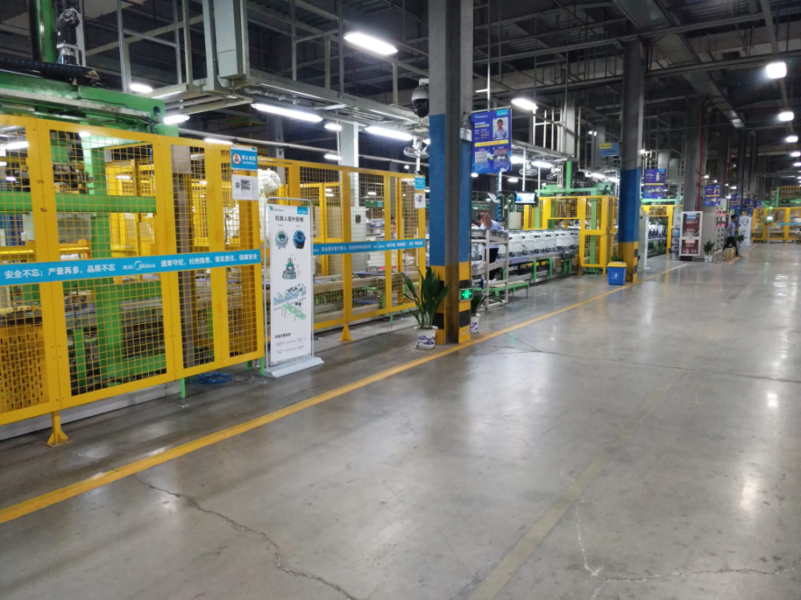
Aspecto futurista con componentes visuales
Tras el éxito de este proyecto, Midea planea explorar cómo pueden seguir utilizando Visual Components en el diseño y puesta en marcha de sus sistemas de producción.
Kong y su equipo quieren personalizar aún más el software para sus aplicaciones y desarrollar sus propios complementos y complementos. "La plataforma abierta y las interfaces de Visual Components nos dan la libertad de ampliar la gama aplicada de herramientas de simulación", afirma Kong.
La Industria 4.0 es otra prioridad para el equipo de Kong y Midea. Buscan digitalizar su producción y hacer que sus fábricas estén más conectadas.
"Queremos construir un gemelo digital de nuestra producción", afirma Kong.
“Planeamos recopilar datos sobre las máquinas, la logística y la producción de la fábrica y visualizarlos en Visual Components. »
“También queremos explorar cómo podemos utilizar las interfaces PLC de Visual Components para proporcionar controles a nuestros activos de producción. »
Acerca de Midea
Fundada en 1968, Midea es el mayor productor mundial de electrodomésticos importantes y el número uno en productos de tratamiento de aire, enfriadores de aire, hervidores y ollas arroceras. La empresa se especializa en tratamiento de aire, refrigeración, lavandería, grandes electrodomésticos de cocina, electrodomésticos de cocina grandes y pequeños, aparatos de agua, cuidado de suelos e iluminación.
Midea, con sede en el sur de China, es una empresa verdaderamente global con más de 100.000 empleados y operaciones en más de 200 países. La empresa cuenta con 21 centros de producción y 260 centros logísticos en todo el mundo.
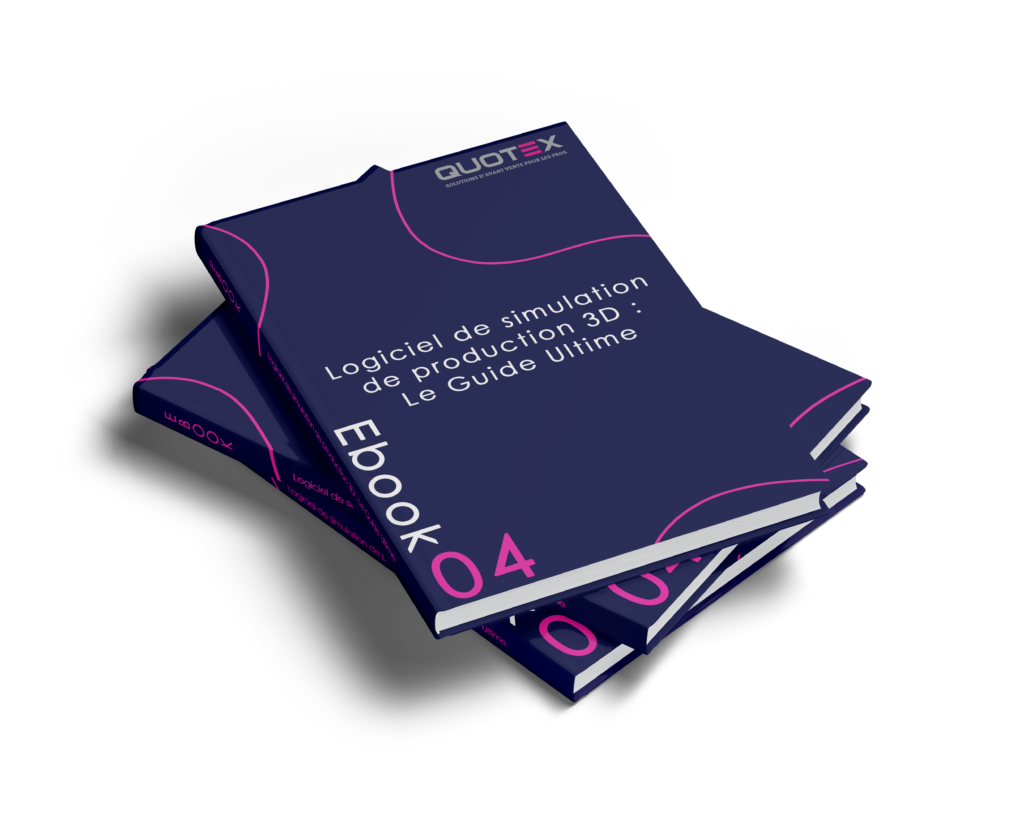