Componentes visuales OLP: programación fuera de línea de robots
El software de programación de robots fuera de línea de próxima generación basado en la potente tecnología de Delfoi Robotics.
Maximiza el potencial de tus robots con una solución de programación rápida, precisa y sin errores.
Acrónimo: OLP (Programación sin conexión) – PHL (Programación sin conexión)
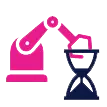
Minimiza el tiempo de inactividad del robot
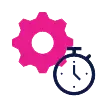
Reducir el tiempo de programación
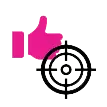
Precisión superior y repetible
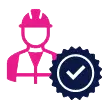
Aumentar la seguridad en el taller
Software PHL todo en uno
Un software para todos los procesos
Programe sus robots para diversos procesos industriales como soldadura, procesamiento o pulverización utilizando un único software.
Soldadura
Visual Components OLP cubre procesos como soldadura por arco, soldadura Tig, soldadura láser, soldadura por puntos y remachado.
Proceso
Cubre procesos como esmerilado, pulido, pulido, lijado, desbarbado, desbarbado, corte por plasma y corte por láser.
Pintar
Cubre procesos como pintura húmeda, recubrimiento por pulverización, pulverización térmica y pulverización en frío.
Esto le permite detectar problemas ocultos y minimizar los riesgos de inversión.
Compatible con las principales marcas de robots industriales.
Marcas de robots
17 marcas de postprocesadores en un solo producto… ¡Y se agregarán más en el futuro!
Controladores
Más de 40 versiones de controladores de robots, incluidos robots más antiguos y modelos más nuevos.
Programa tus robots sin importar su marca o tipo. Elimine la necesidad de utilizar varios software para diferentes marcas. Visual Components OLP admite 17 de las marcas de robots más comunes.
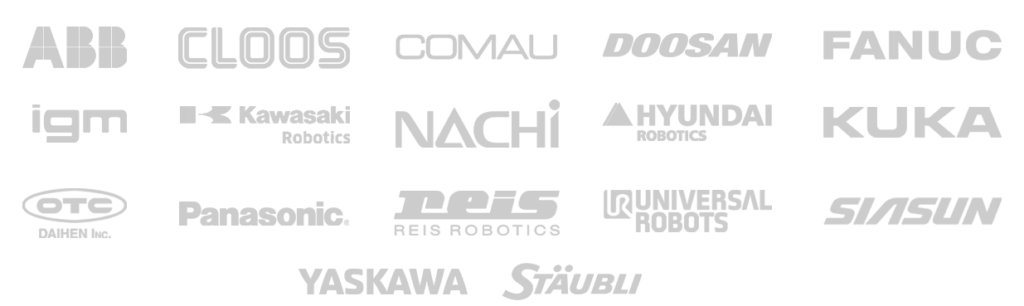
Programas rápidos, fiables y precisos.
Genere rápidamente programas en células robóticas virtuales, en cualquier parte del mundo.
Deje que el software valide y optimice los programas antes de enviarlos a producción para evitar errores costosos.
Programación con un clic
Programa tus robots en unos pocos clics
Optimización del tiempo
Guarde sus programas para reutilizarlos en cualquier momento para otros proyectos.
Descubre los diferentes procesos gestionados por Visual Components OLP en vídeo
Diferentes procesos OLP
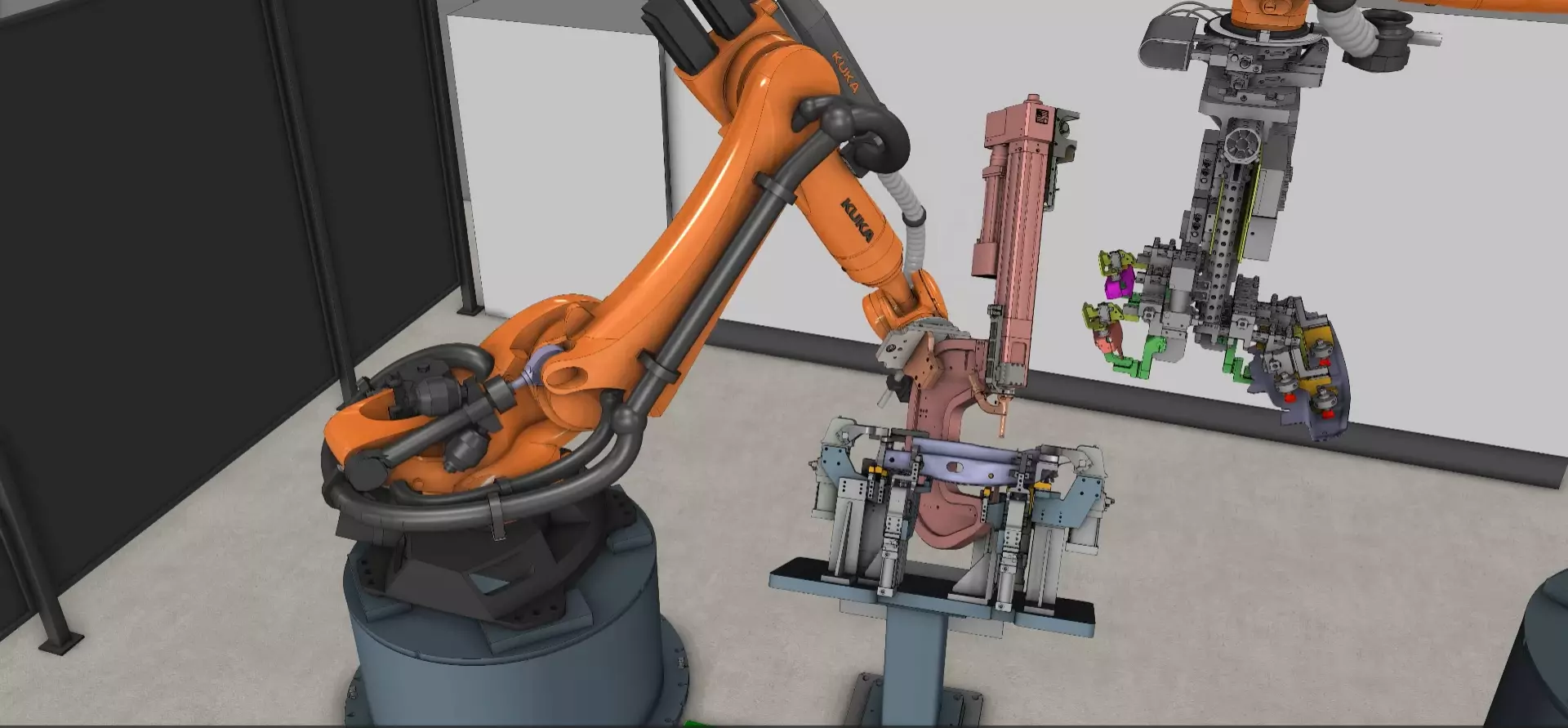
0:11
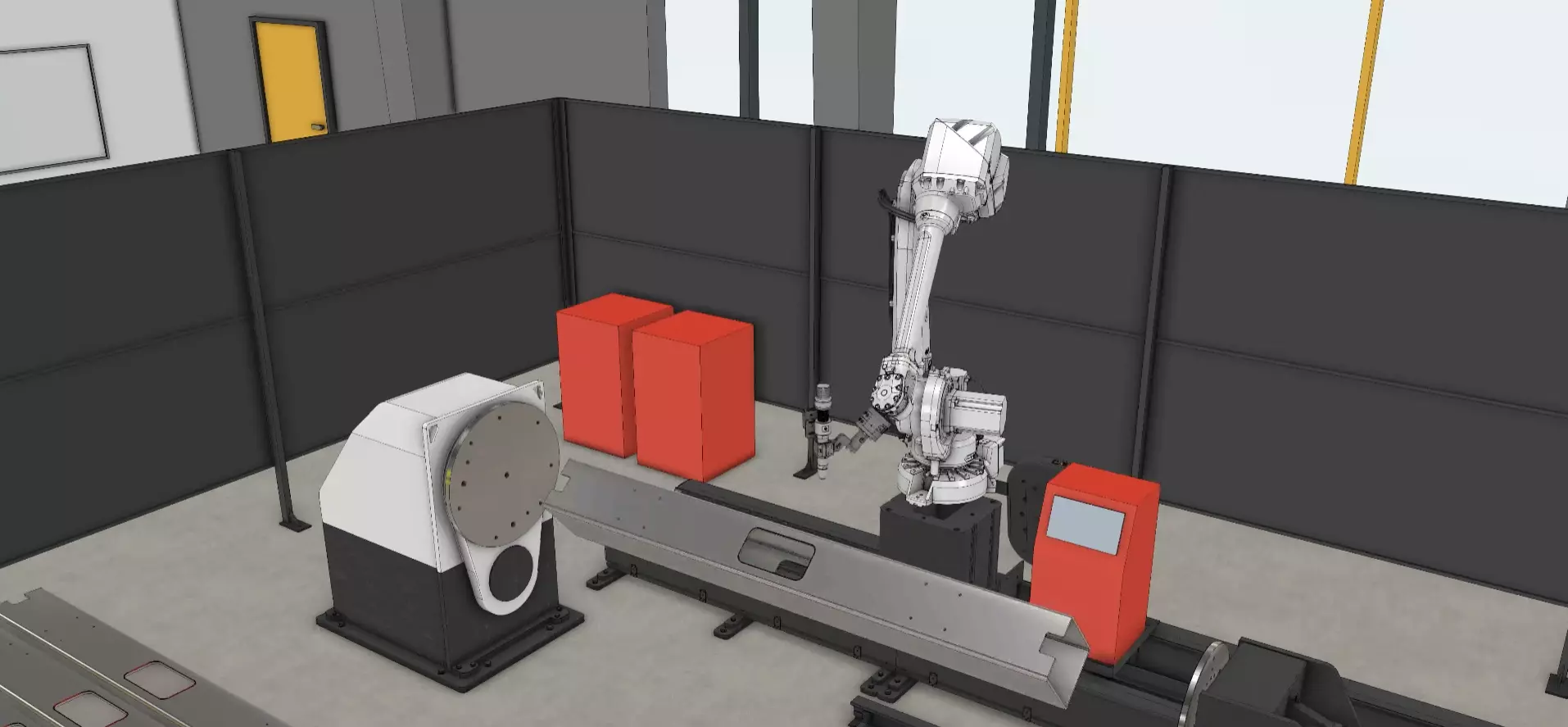
0:11
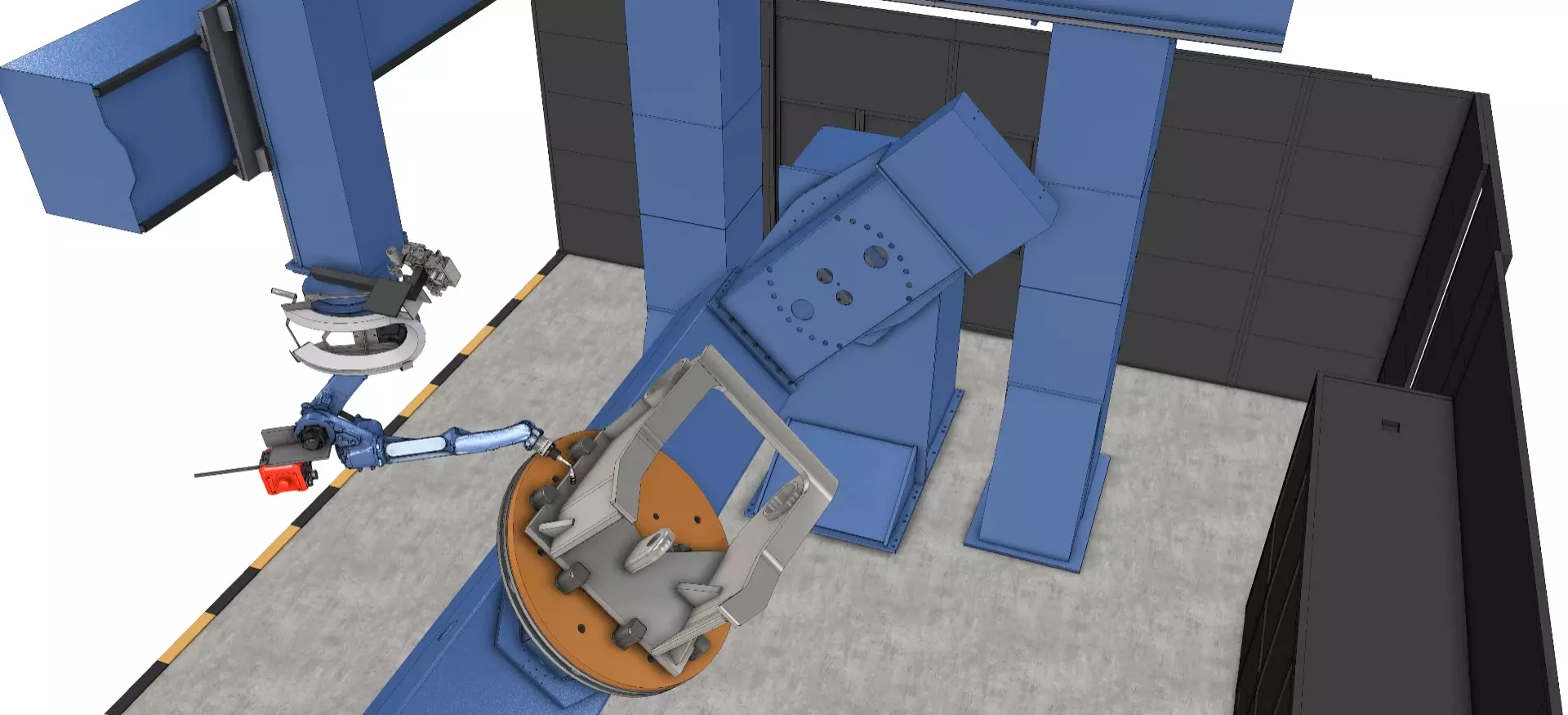
0:10
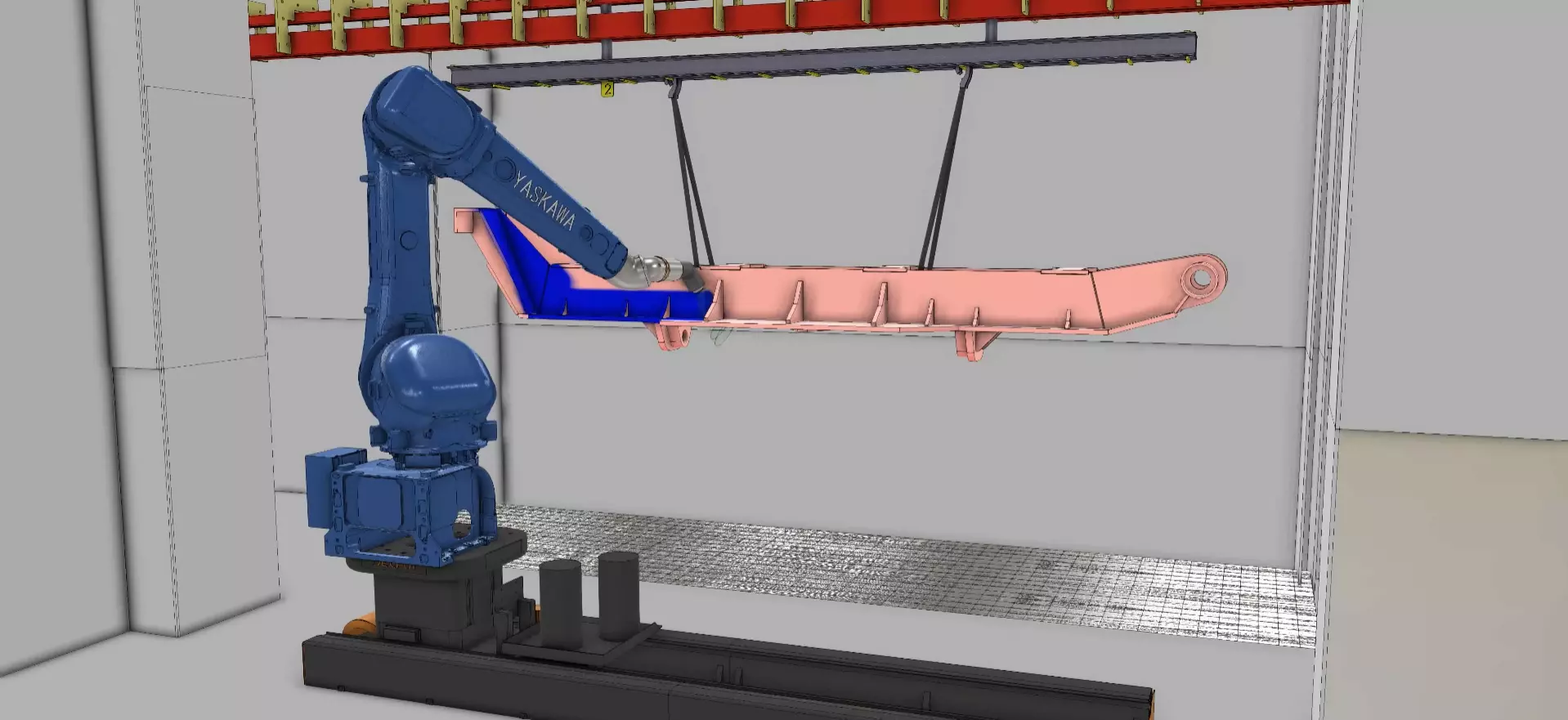
0.14
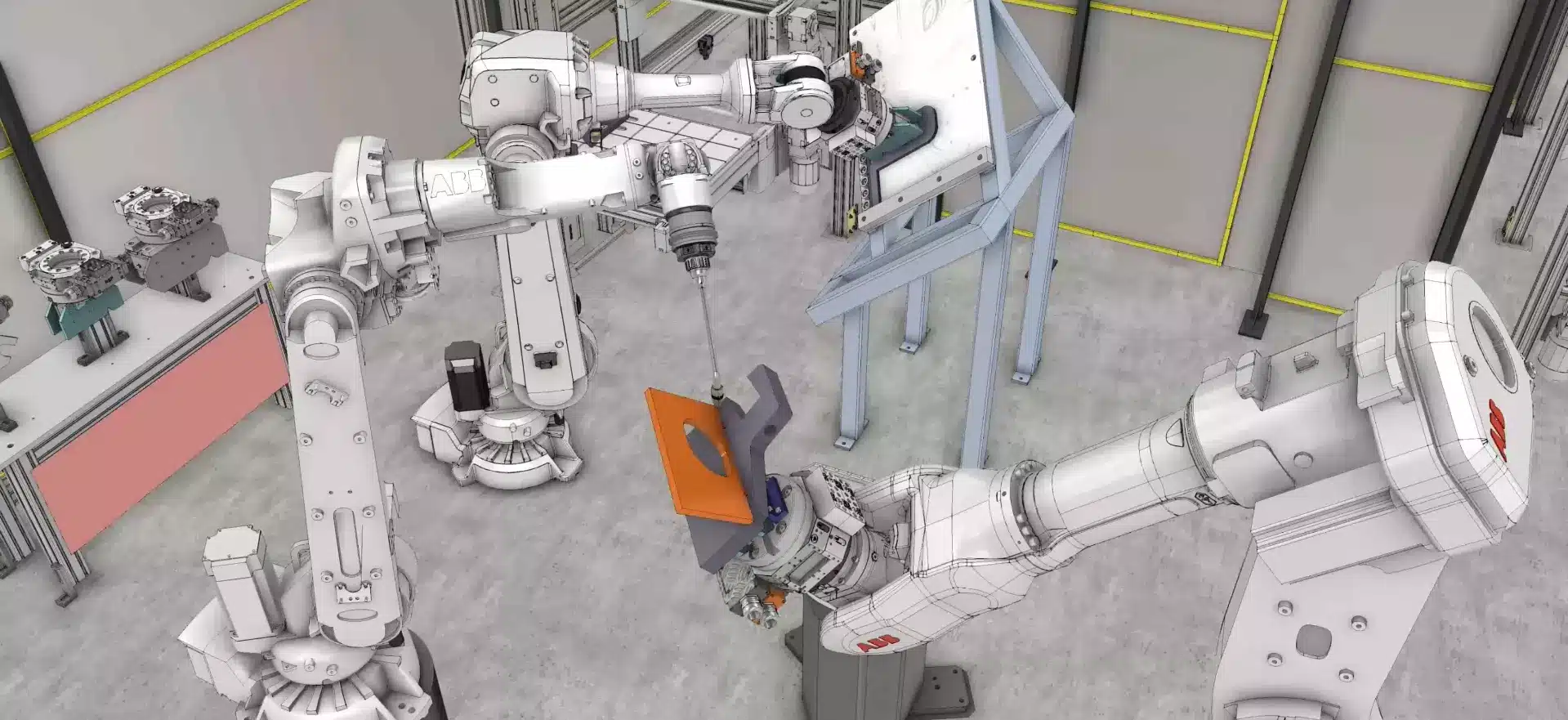
0.14
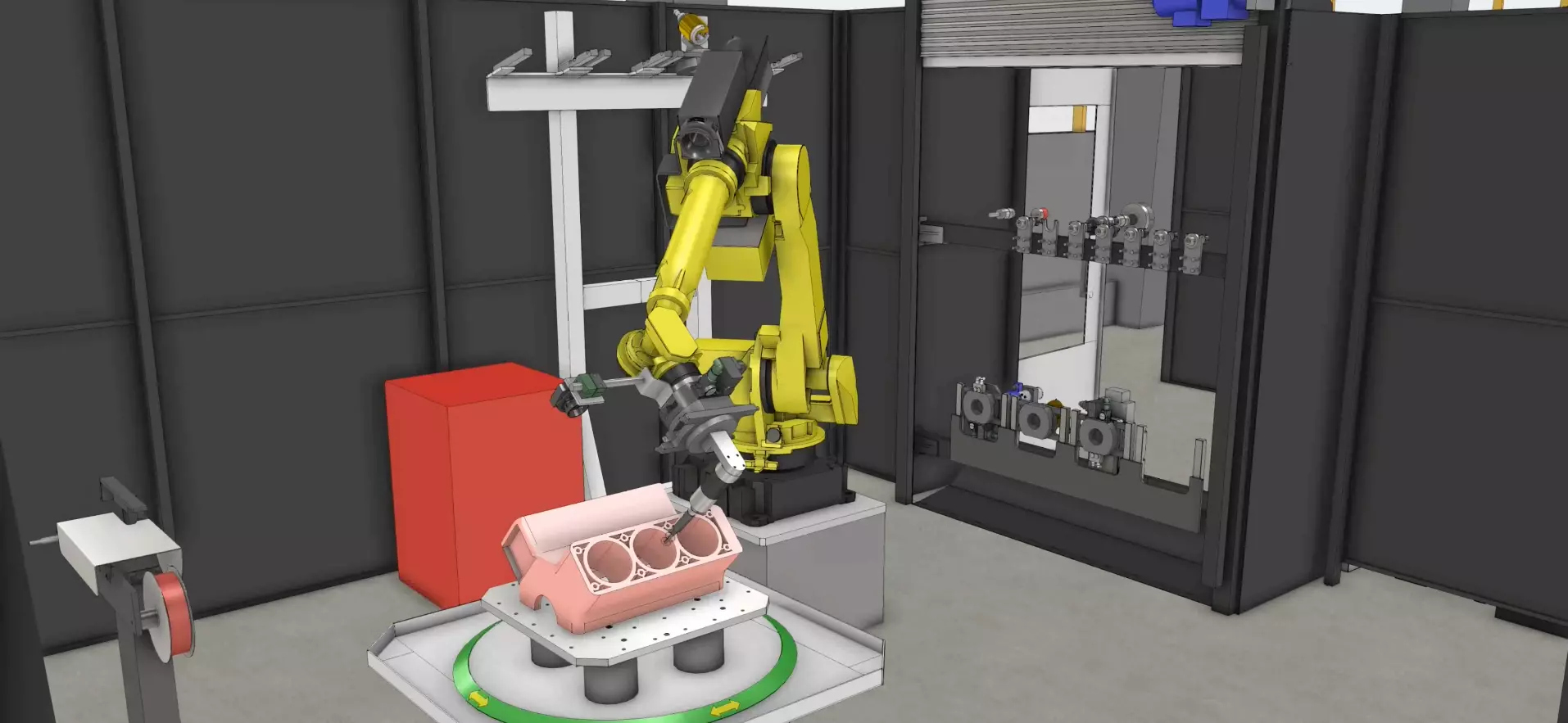
0.11
Durante un vídeo de 30 minutos, nuestro integrador experto de VISUAL COMPONENTS hará un balance de sus prácticas de diseño de líneas y estimará el tiempo que podría ahorrar gracias a Visual Components.
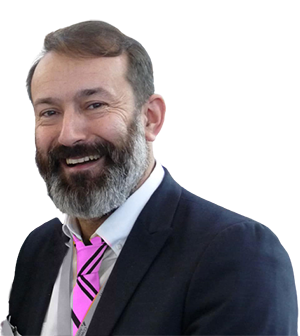
Preguntas frecuentes sobre la programación de robots fuera de línea
La programación de robots fuera de línea (PHL u OLP en inglés) es un método de generación de programas de robots en software de computadora (entorno virtual) basado en datos CAD 3D.
Una vez que el programa del robot se genera y verifica en el software, se puede descargar al robot físico.
Imaginemos que un robot está programado para soldar una pieza circular sobre una pieza metálica.
El robot debe mover el soplete de soldadura en un arco 3D alrededor de la circunferencia de la pieza, manteniendo al mismo tiempo una orientación precisa con respecto a la superficie. Puedes hacerlo enseñando puntos usando un colgante, pero necesitarás una gran cantidad de puntos y llevará mucho tiempo. Lo más probable es que el espacio entre las antorchas varíe, al igual que la orientación de la antorcha. Además, la celda del robot no estará disponible para producción hasta que complete la programación. Este cierre puede durar días o incluso semanas. Con PHL es mucho más fácil producir el programa del robot. Importe un archivo CAD de la celda de soldadura al software OLP y muestre la ruta que desea que tome la antorcha. Una vez completado, el software genera el programa del robot y comprueba posibles colisiones. Una vez verificado, el programa se descarga en el controlador del robot, se ejecuta una vez a baja velocidad para una doble verificación y la celda está lista para reanudar el trabajo.
Cada aplicación robótica es candidata a PHL;
la única condición es contar con modelos digitales de la celda de trabajo, piezas, utillajes y fijaciones. (Hoy en día, todo está diseñado en CAD, lo que no debería ser un problema). Sin embargo, los beneficios son mayores a medida que las trayectorias del robot se vuelven más complejas y es necesario enseñar más puntos. Con estos puntos en mente, estos son algunos de los mejores casos de uso de PHL:
Soldadura : el acceso y la orientación son desafíos particulares que aborda PHL, y cordones de soldadura complejos pueden requerir una gran cantidad de puntos.
Recubrimiento (pintura) : al igual que con la soldadura, la orientación es importante, al igual que el espesor de la pintura y la distancia de separación, lo que garantiza que se pueda alcanzar y pintar todas las áreas de manera óptima.
Eliminación: muchas operaciones de ensamblaje requieren la eliminación de cordones de adhesivo largos y complejos: PHL permite crear trayectorias de herramientas rápidamente fuera de línea con una calidad constante.
Procesamiento (superficial) : aplicaciones como granallado y desbarbado a menudo requieren recorridos largos y complejos que requieren una gran cantidad de puntos.
Aplicaciones de montaje (sin plantilla): los movimientos de agarre e inserción requieren un control preciso de la orientación de la pinza, lo que es posible a un nivel superior con PHL.
Aplicaciones de manipulación de materiales : PHL permite al programador determinar la distancia más rápida entre dos ubicaciones, que no siempre es la ruta más obvia.
Corte : el corte por plasma, láser o chorro de agua puede funcionar para piezas estándar, pero para geometrías complejas, se necesitan robots con patrones de corte precisos que se puedan generar con PHL.
Los fabricantes que utilizan el software OLP informan de numerosos beneficios:
No hay tiempo de inactividad del robot
. El tiempo de programación se puede reducir hasta en un 80 % y la utilización del robot aumenta hasta en un 95 %, lo que aumenta la productividad del programador y reduce el tiempo de inactividad de la celda.
Tiempos de configuración rápidos.
Se necesita menos tiempo para lanzar un nuevo producto a producción: la programación se realiza simultáneamente en lugar de secuencialmente.
Mayor seguridad
Menor riesgo de accidentes y lesiones
Calidad más alta y repetible
Los programas de robot están mejor optimizados (tiempos de ciclo más cortos, mayor precisión y consistencia), lo que da como resultado una calidad de producción más alta y repetible.
Independiente de la marca y el proceso del robot
Independientemente de la marca del robot o el tipo de proceso, el software OLP avanzado puede cubrir todas las aplicaciones.
No más sorpresas
Se evitan cambios de última hora en tornillería y herramientas.
Aunque cualquier fabricante que utilice robots puede beneficiarse del PHL, las mayores ganancias se observan cuando los tamaños de lote son pequeños y los ciclos de producción cortos.
El problema es que al programar el robot, los cambios y ajustes frecuentes reducen el tiempo de actividad y las horas de funcionamiento.
Sin embargo, con Visual Components OLP, los programas se prueban virtualmente y se cargan en los robots mientras se modifican los aspectos físicos de la celda (sujetadores, abrazaderas, etc.).
La prudencia sugiere someter al robot a un ciclo de baja velocidad para comprobar si hay colisiones, tras lo cual la célula está lista para reiniciar la producción. Además, cualquier problema relacionado con el diseño en la documentación o los modelos se identifica con anticipación y puede comunicarse a otros equipos y resolverse sin pérdida de tiempo de producción.
La alternativa al uso de OLP es programar directamente en el robot.
Esta solución plantea al menos tres problemas: 1. Riesgo de retrasos en el proyecto y costos adicionales
2. Preocupaciones de seguridad
3. Pérdida de capacidad de producción
El riesgo de retrasos en el proyecto es importante cuando se realiza la programación en el robot.
En este punto, se han diseñado, construido e instalado todas las herramientas y accesorios. Hay transportadores u otros dispositivos de manipulación en su lugar y las piezas están listas para su uso. Sólo ahora el programador puede empezar a enseñarle los puntos al robot. Es casi seguro que surgirán problemas. Es posible que el robot no pueda llegar a una ubicación particular, que las piezas estén en la ubicación incorrecta o que no se pueda alcanzar el tiempo de ciclo objetivo.
En todos estos casos, la única solución es redefinir los puntos problemáticos de la celda.
Inevitablemente, esto retrasa el inicio de la producción, a veces varias semanas, y genera importantes costes adicionales. Aprender puntos usando un colgante a menudo requiere que el programador ingrese a la celda: a veces esta es la única manera de ver hacia dónde se dirige la herramienta o verificar si hay colisiones.
Poner el robot en modo de “aprendizaje” debería garantizar su seguridad, pero siempre existe el riesgo de que se produzca un movimiento inesperado, ya sea del propio robot o de uno de los otros mecanismos de la celda. Finalmente, mientras el programador va aprendiendo puntos dentro de la celda de trabajo, el robot no puede hacer nada más. Este es un tiempo improductivo hasta que finaliza el programador y se prueba el programa. ¡E incluso los mejores programadores tienden a subestimar el tiempo necesario para realizar la tarea!