In this case study, we'll show you how AGCO, one of the world's leading agricultural machinery manufacturers, used Visual Components to model complex production equipment and workflows with the digital twin. This made it possible to optimize production cells, improve processes and simulate improved workflows.
Key benefits:
- Accessibility studies without stopping production
- Realistic cycle time analysis
- The digital twin facilitates future optimizations
A growing population: a problem for the agricultural sector
How can the world ensure food supplies for its ever-growing population in the future? The agricultural sector must provide increasing quantities of cereals, feed crops and other food products. And it must do so within the framework of partly contradictory objectives – on the one hand profitable, on the other ecological. These goals can only be achieved with modern agricultural machinery, because only modern technology can guarantee good yields at reasonable costs through precise sowing, targeted fertilization and optimal plant protection.
AGCO, the global tractor manufacturer
AGCO is one of the world's leading manufacturers of tractors, combine harvesters and other agricultural machinery sold under well-known brands such as Fendt and Massey Ferguson . The Fendt factory in Asbach-Bäumenheim , Bavaria, produces driving cabins for tractors and self-propelled harvesting and crop protection machines . Nearly 1,200 employees manufacture, weld, paint and assemble cabins of various models in this factory. Additionally, Fendt tractor assembly cabs are delivered Just-In-Time and Just-In-Sequence , meaning the parts are built in the same order as they are needed on the line. assembly plant at the Fendt factory near Marktoberdorf.
The essential part of a driver's cab is a structure made of bent and welded tubes. The tubes are automatically fed from a storage system and routed to a laser cutter. Then the tubes are fed to bending machines, loaded and unloaded automatically by robots. Finally, the last step before welding, the tubes are cut to their final contour by a 3D laser; this is also done automatically. After that, the tubes are welded together to form the cabin frames. The latest welding technologies and innovative welding robots are used for this . Thanks to modern precise cutting and welding processes, it is possible to manufacture ergonomic cabins with curved windshields.
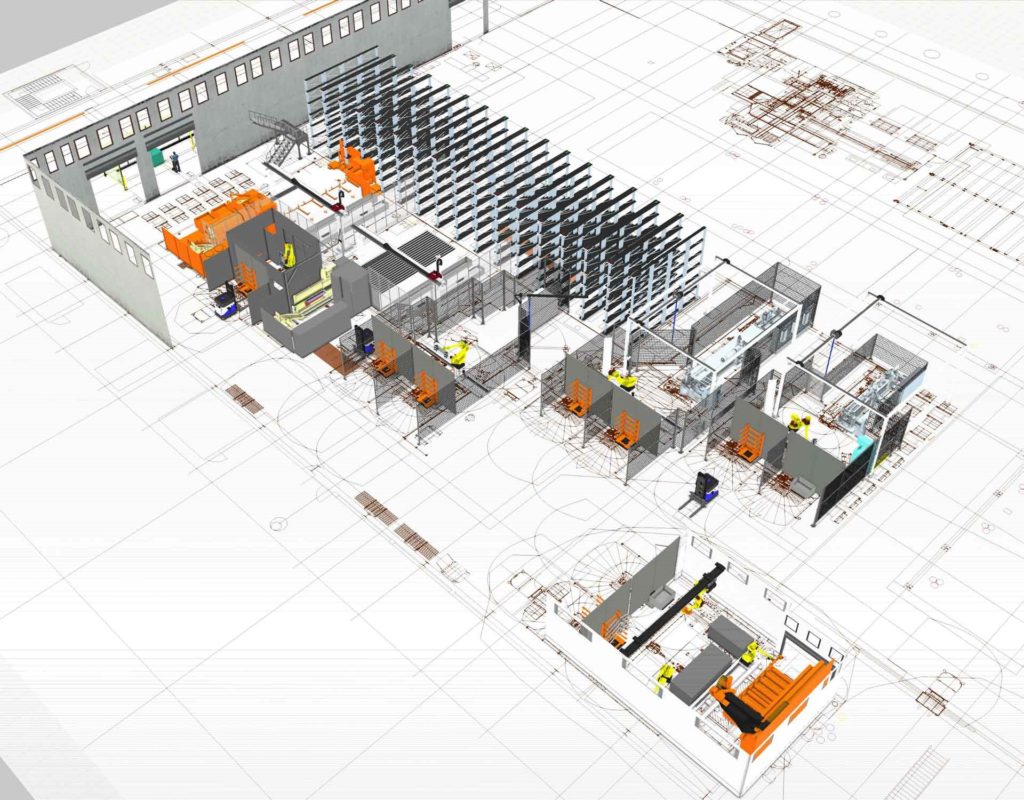
AGCO's engineering department is responsible for process optimization and procurement of manufacturing equipment . They wanted tube processing workflow Additionally, the tubes are processed by a total of six interconnected systems with a high degree of automation. Previously, to carry out such investigations and assess possible improvements, production had to be stopped, which resulted in high costs. Therefore, the engineering department looked for a better alternative.
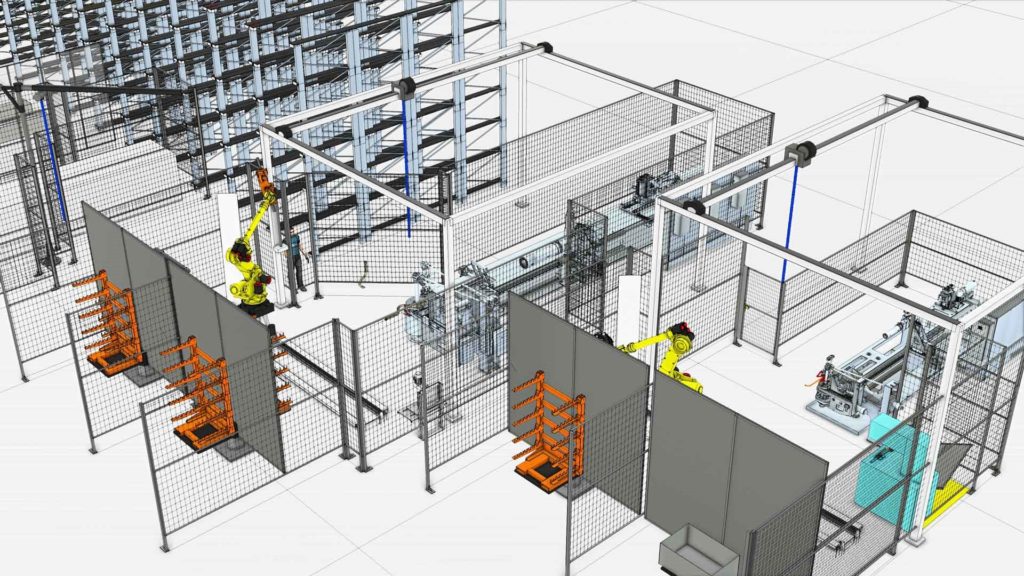
AGCO turns to the digital twin to optimize its production
It was decided to model the rather complex production equipment and workflow with the digital twin . Then, the digital twin improves processes, optimizes production cells and simulates improved workflows . Finally, the digital twin also provides a basis for discussion for future optimizations, in case other activities in a cell need to be carried out by the robot.
AGCO manufacturing engineers found the solution in 3D factory simulation software from Finnish solutions provider Visual Components . On the one hand, Visual Components simulation can be used to design and optimize complete manufacturing systems, including offline programming of robots. On the other hand, the software simulates the entire manufacturing process and the smooth cooperation between robots, laser cutting machines and tube benders. Furthermore, simulation makes it possible to minimize non-productive time and study problems such as robot accessibility and collision avoidance.
“In the first step, it was not important to model all the systems down to the smallest detail. Only the machines that we thought should be changed were important. The result of the simulation was very satisfactory. For example, we were able to carry out accessibility studies on certain equipment that we would not have been able to carry out previously without a production stoppage. And we were able to realistically analyze cycle times that previously could only be estimated. »
Norbet Pritzl, Project Manager at AGCO
Visual Components powerful software for AGCO
The project gradually expanded as AGCO engineers learned more about the capabilities of Visual Components software. They started with a small area they wanted to optimize and gradually rolled out the simulation across all of the automated equipment . And in the future, other areas of manufacturing will also be optimized with the simulation solution from Visual Components.
When introducing a new software solution, it is generally expected that managing the still unfamiliar tool will pose some challenge. But not in this case, because the good communication and training received from Visual Components helped the employees a lot.
The extensive component library provided was also extremely useful : almost all robots and other equipment used in the pipe bending, cutting and welding process were already available in the library. Then, if components were not available, they were either improvised or modeled in the CAD system and then imported into Visual Components. It is very helpful here that Visual Components has interfaces to a large number of CAD systems.
“With Visual Components, we can run scenarios in our production process that could previously only be realized with a production shutdown and through extensive testing on the production line”
“It also allows us to model and simulate accurately new concepts so that they can be used to obtain quotes, for example from equipment manufacturers. This saves us a lot of time in project management. In the past, we had to try to reach a common consensus with numerous on-site meetings, elaborate presentations and detailed descriptions. Visual Components allows us to communicate much more easily with international OEMs. »Norbet Pritzl, Project Manager at AGCO
A bright future with Visual Components' digital twin
Feedback within the company regarding the capabilities of Visual Components has been very positive ; many engineers were waiting for such a tool. This is also a great benefit for production equipment suppliers, as they can more easily understand what the requested equipment is supposed to do .
Will AGCO continue to use Visual Components solutions in the future? Norbert Pritzl has specific ideas: “We will also use Visual Components in other projects. We are currently working on projects such as the development of a new welding hall and the optimization of assembly . Now we can visualize and simulate an optimized concept quickly and easily. This will lead to many other projects and therefore further optimization of our production.”
State-of-the-art automation in manufacturing ensures the perfect quality of every tractor cabin at the highest level. Finally, Visual Components' digital twin has played a major role in helping to manufacture cabins for tractors and other agricultural machinery with exceptional quality at competitive prices .
Are you interested in the 3D simulation software, Visual Components? Contact us for a free demonstration.
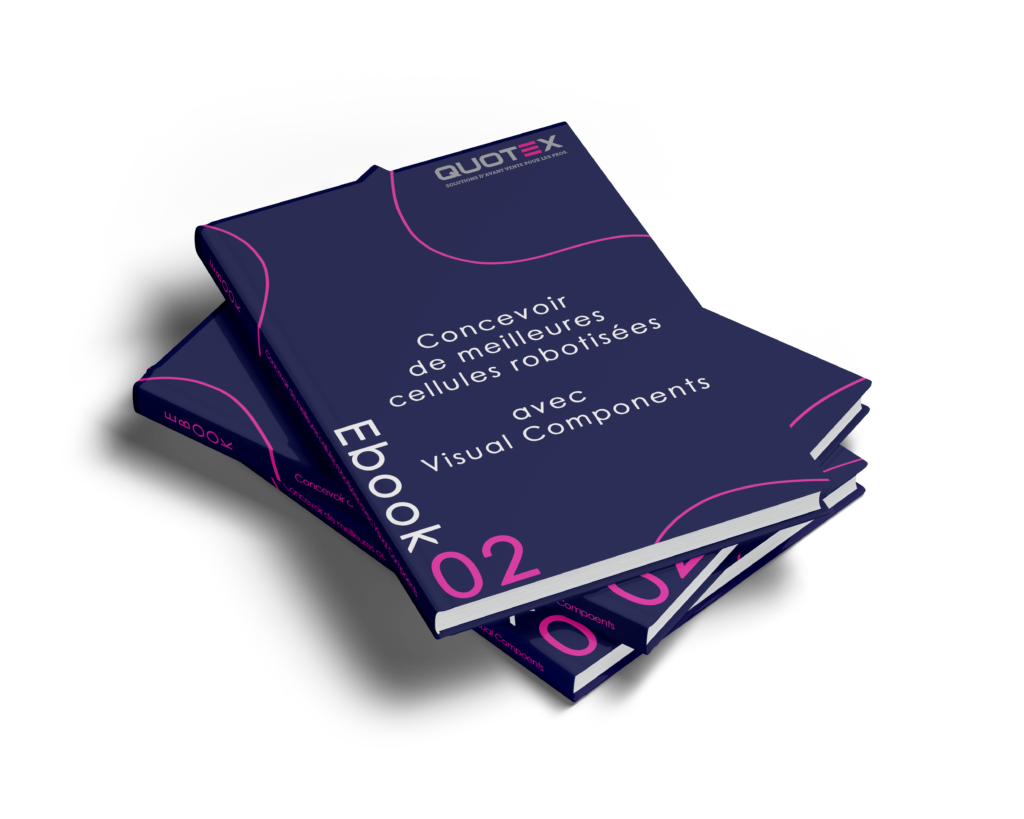