In this case study, we'll show you how KONE, a global leader in the elevator and escalator industry, uses Visual Components to improve productivity and reduce time to market.
Key benefits:
- Faster decision making and more effective communication with stakeholders
- Save time during the development process
- Reduced time to market
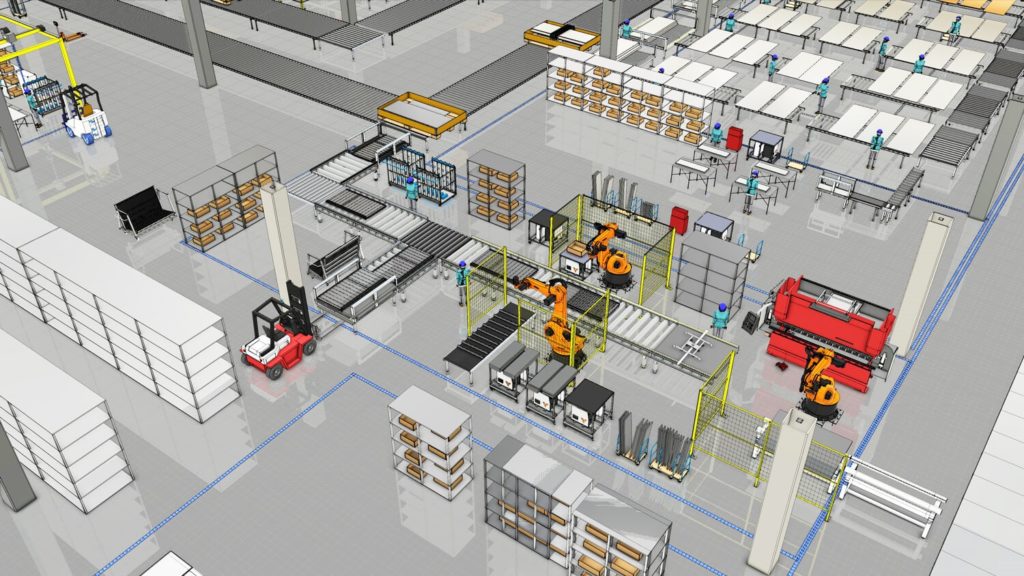
Looking for a 3D layout and simulation tool
With 14 factories, 55,000 employees and a turnover of 8.9 billion euros in 2017, KONE is a global leader in the elevator and escalator industry. The Finnish company provides elevators, escalators and automatic building doors, as well as solutions for maintenance and modernization, which add value to the life cycle of any building.
As KONE has grown over the years, so has the demand for its factories.
“A little over a year ago, we recognized the need to change the way we communicated with our stakeholders about the implementation of assembly cells,” said Miikka Ahola, head of manufacturing solutions for KONE for KSU Manufacturing Solutions.
“New production processes are complex and difficult to explain via CAD and Excel, especially with robotics. »
Miikka and his team decided it was time to look for a solution that could not only help them plan and design new production solutions, but also improve their communication with partners during process implementation and development.
“We were mapping out potential solutions for the simulation and layout of our factories and we wanted to have 3D plans because they help a lot in visualizing the layout and space requirements,” Miikka said.
“While researching potential suppliers, we found Visual Components software. »
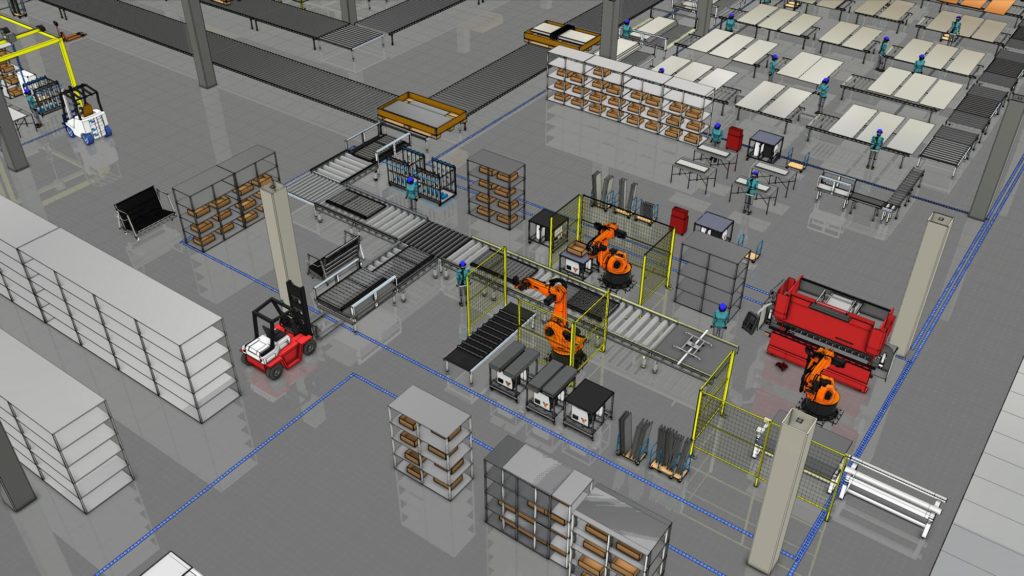
After conducting an evaluation of potential software, Miikka and his team decided to move forward with Visual Components.
“Using Visual Components was much easier compared to other products we evaluated. It was very important for us,” Miikka said.
A global planning and development team
KONE's global development and planning team is headquartered in Espoo, Finland. It is a large international team that extends to all 14 factories.
“We have an international development team responsible for technology and process development, which is supported by local teams in each factory, with their own development engineers,” explains Miikka.
“Most of the development of lines, processes and technologies is carried out by the international team, while the implementation and fine-tuning of solutions is done in coordination with the local teams. »
All new R&D projects are first reviewed by the international team. They examine investments, technology and feasibility of projects in the first place, then transfer the product from R&D to production and supervise the implementation in KONE factories.
“We work in the middle, ensuring that all plans and investments are made, and that everything is ready to start production,” explains Miikka.
Integration of Visual Components into the planning process
For Miikka and his team, it was easy to incorporate Visual Components into their planning process.
“Typically, we use Visual Components in the early stages of new product implementation projects. This helps us present to our partners a clear picture of the type of cell or production line as well as the space required to achieve production targets,” explains Miikka.
New investment projects within the international development team generally begin with the creation of line or cell mock-ups.
“We start by defining what we are going to do and develop a mock-up that includes all the necessary assembly lines and cells, but which might not be defined based on the specific needs of the product. This helps us define the space needed to start,” says Miikka
Once they have chosen a design that they think will work, they move on to creating the layout.
“We start by refining individual cells and improving ergonomics,” explains Miikka.
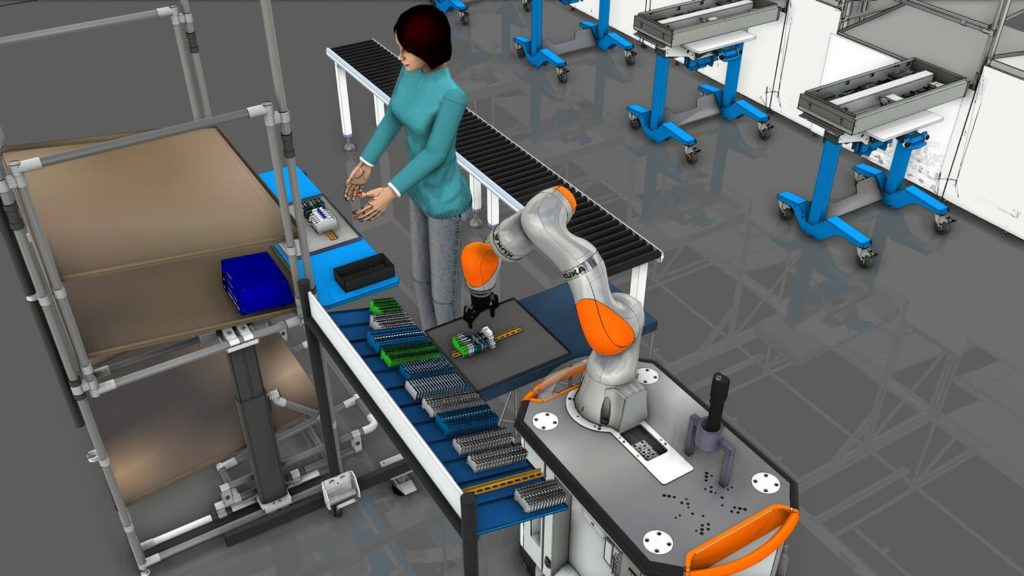
Next, they simulate the production flow, validating production calculations and space requirements, and look for opportunities for optimization and cost reduction. Having a visual tool to communicate these tradeoffs with partners was particularly helpful for Miikka and her team.
“We can visually show our partners in R&D, product development, quality and operations how changes in design can reduce labor and equipment costs,” says Miikka.
After gaining approval from management to proceed with the project, they use Visual Components export files, such as simulation videos, 3D PDFs, and 2D drawings, to facilitate communication with factories during production. implementation and deployment.
Work with suppliers to develop the electronic catalog
For Miikka and his team, it was easy to incorporate Visual Components into their planning process.
“Typically, we use Visual Components in the early stages of new product implementation projects. This helps us present to our partners a clear picture of the type of cell or production line as well as the space required to achieve production targets,” explains Miikka.
New investment projects within the international development team generally begin with the creation of line or cell mock-ups.
“We start by defining what we are going to do and develop a mock-up that includes all the necessary assembly lines and cells, but which might not be defined based on the specific needs of the product.
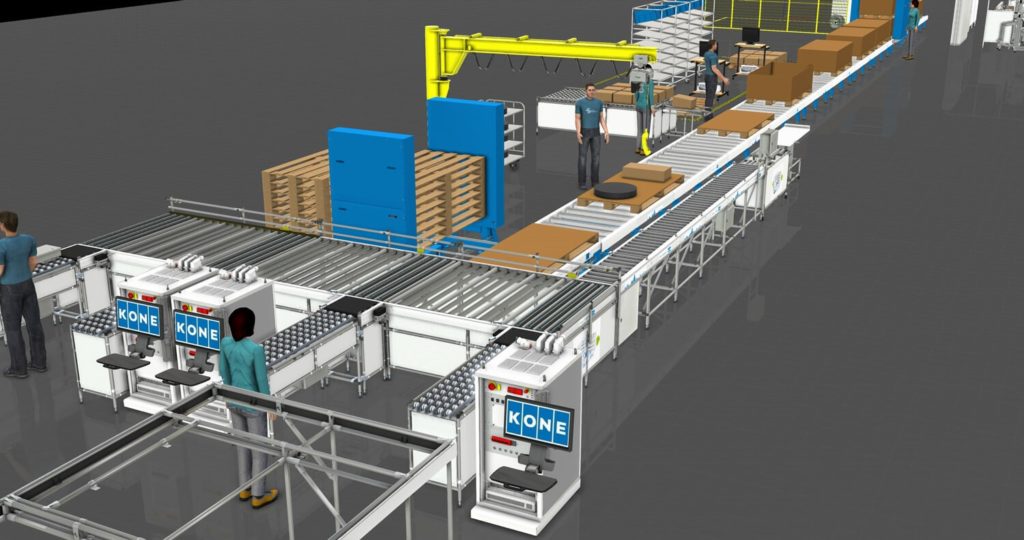
This gave Miikka and his team reference implementations that they can use to easily start new projects, but also allowed them to evaluate new equipment and solutions developed by the integrator and improved their collaboration during planning new projects. »
“In this arrangement, both parties benefit,” explains Miikka.
Thanks to KONE's partnership with their system integrator, Miikka and his team have a constant flow of components and layouts that they can use in their development planning process. They are also better informed about the latest technologies and production processes.
“We get a regularly updated library of components and layouts, to help us with our planning, and they have project opportunities in our factories around the world,” explains Miikka
Improved productivity, reduced time to market
For Miikka, the biggest benefit that Visual Components software brings to KONE is the time savings in the development process. It facilitates faster decision-making and more effective communication with partners. This also helps them reduce time to market.
“Visual Components helps us start the production development process much earlier than before and reduce critical time to market,” explains Miikka.
Miikka and his team juggle a lot of simultaneous projects, from planning new factories in India to testing future technology concepts. Visual Components helps them be more productive so they can meet the growing demand for KONE products.
In the future, Miikka hopes to expand the use of Visual Components to all factories around the world.
“We plan to implement Visual Components in our factories, so that local development engineers can use it to highlight changes, ideas and suggest lean improvements with simulations,” explains Miikka.