3D production simulation is one of the major trends in Industry 4.0. Learn about the different types of production simulation, simulation methods and their benefits in our comprehensive article.
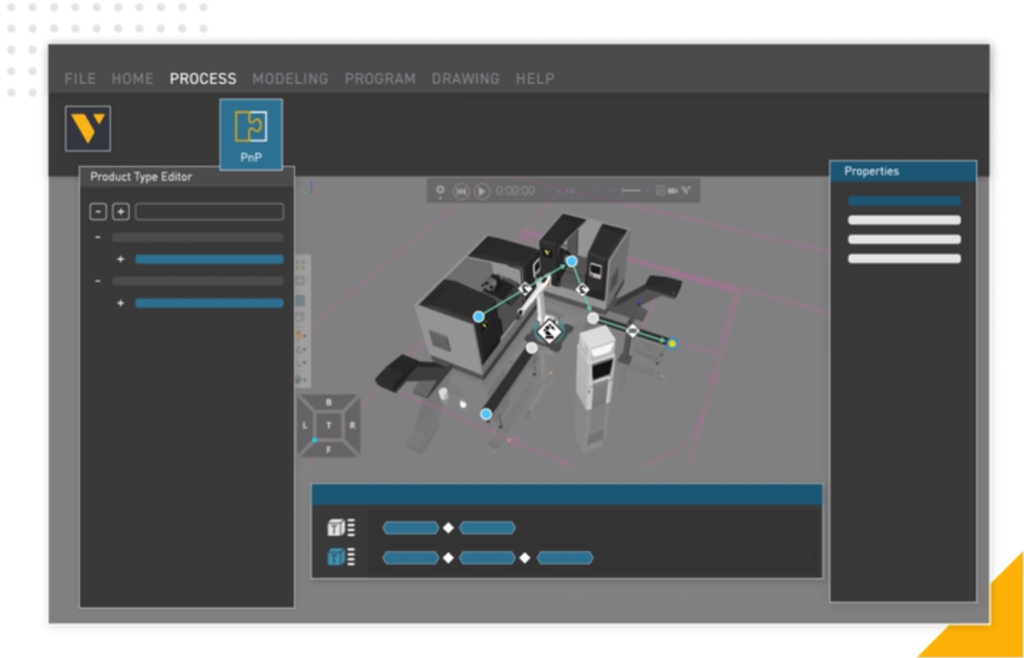
Purchasing manufacturing machinery and setting up production lines and warehouses is not one of the easiest jobs in the world. Decisions made during the planning stages will establish and limit costs and capacities for years to come . Get it wrong and you cede the advantage to your competitors, but get it right and your business will flourish.
So how do you determine which equipment to purchase and which layout to use? Using 3D production simulation .
Simulation is a powerful way to reduce risk by evaluating multiple alternatives . 3D production simulation tools, like those from Visual Components , allow manufacturers to experiment with alternative layouts and configurations.
They make it possible to quantify the results of variability and uncertainty. They provide insight into opportunities for improvement and are powerful tools for communicating ideas and proposals.
Additionally, these tools help facilitate decision-making with valid arguments and improved forecasts that simplify key planning obstacles .
The idea of simulating manufacturing operations is not new, but only recently has sufficient computing power become available to make it practical, accurate and efficient. This article provides an introduction to 3D production simulation for those unfamiliar with it, describes the different types of simulation, and explains the benefits that accrue from its use.
The importance of production simulation
Manufacturing operations are often very complex. In many installations, work comes to a machine in batches. Let's assume that in this case the machine processes one item at a time. When the entire batch has been processed, it moves to the next machine. Now multiply that by a dozen steps in the manufacturing process and fifty different product batches that require different combinations of operations to pass through the same factory .
It's difficult to understand different workflows and queues, but it 's even more difficult to determine where to make changes that will reduce costs or increase capacity . This is where production simulation can help highlight bottlenecks and streamline daily operations.
Different ways to simulate production environments
Simulation involves building a model to reproduce the time-dependent behavior of the production environment . This could be done with wooden blocks and cardboard. This is often attempted with spreadsheets, or it can be done with software developed specifically for the task. Once built, the model is run through as many production runs as necessary to answer the question at hand.
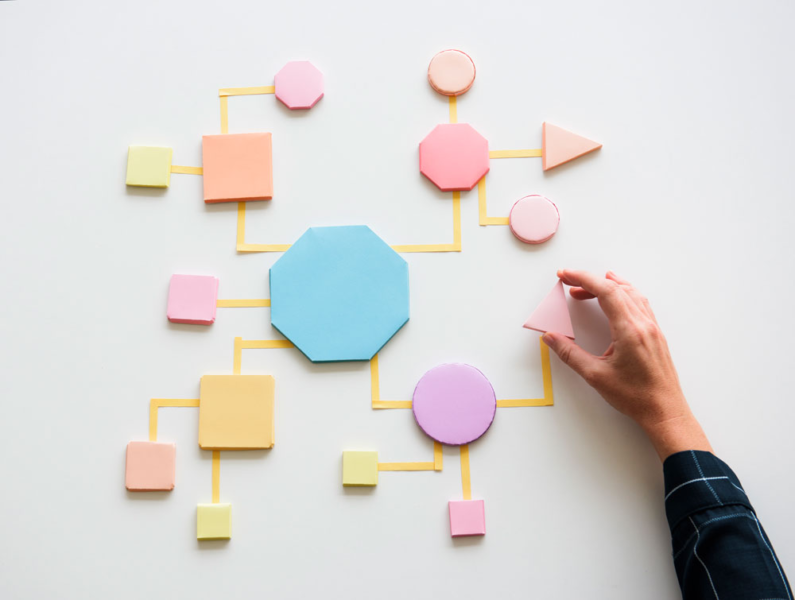
Physical mockups can be an effective way to understand a layout or workflows on a particular machine , but they are quickly overwhelmed by complexity and it is impractical to anticipate more than a few cycles.
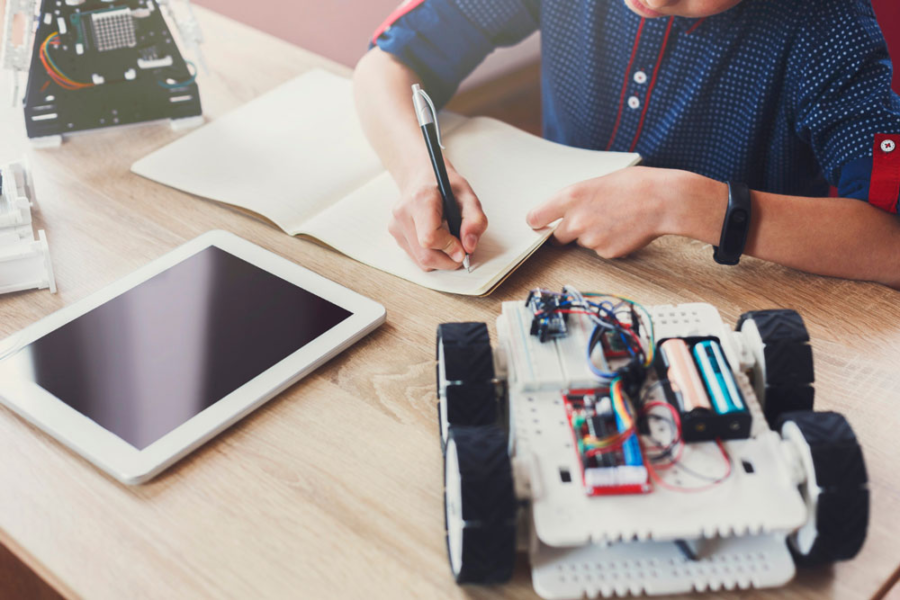
Spreadsheets are best suited for examining the impact of variability and for modeling multi-step operations . However, they have several limitations.
Some of the disadvantages include:
- They can quickly become extremely complex
- It is impossible to integrate every variable and sequence step for every product, such as physical characteristics, for example, product flow between different processes, spacing issues, manual actions between processes, etc. These issues are commonly seen in the manufacturing environment and many times they are identified as the real bottlenecks in the production processes
- It is very difficult to explain the conclusions drawn from spreadsheet modeling
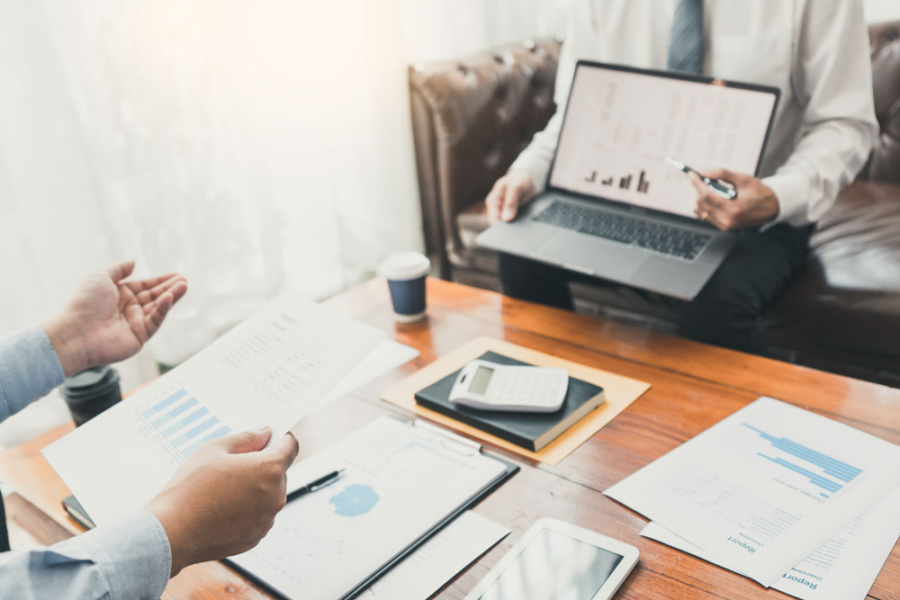
The simulation software uses graphics and animations to display the results of the intensive mathematics taking place “under the hood.” This allows the user to see what is going to happen, which is more impactful than scrolling through rows and columns of results .
Production simulation begins by building a model of the manufacturing operation, line, cell, or factory . This must reflect reality as closely as possible: any errors will reduce the precision and value of the results. When simulating an existing operation, validating model accuracy is simple: enter or load a recent production schedule or machine specifications and see how closely the simulation results match those actually obtained .
Where things get complicated is building a layout or operation model that does not yet exist. This is something that could be done to assess the flow of materials in an as yet unbuilt warehouse or packing hall. Under such conditions, it is very important to test hypotheses and gather as much data as possible to ensure accuracy . In such cases, even if the model cannot be verified against real data, different scenarios or approaches can still be compared to each other to obtain the "most likely solution".
2D vs 3D production simulation
Early simulation tools provided a 2D view of the layout or area being modeled. The processes were represented as blocks with predefined process times and the material throughput was calculated based on these cycle times.
While it was a huge advance over spreadsheet modeling, the 2D layout was only a crude approximation of the physical implementation . This made material flows difficult to track or untangle and inventory quantities difficult to see.
Additionally, unintuitive graphics an audience of the merits of a proposition ; remember that the simulation lacked resources such as humans, vehicles, etc. And perhaps of greatest importance, this hindered the ability of those to use the model to make quick and effective investment decisions.
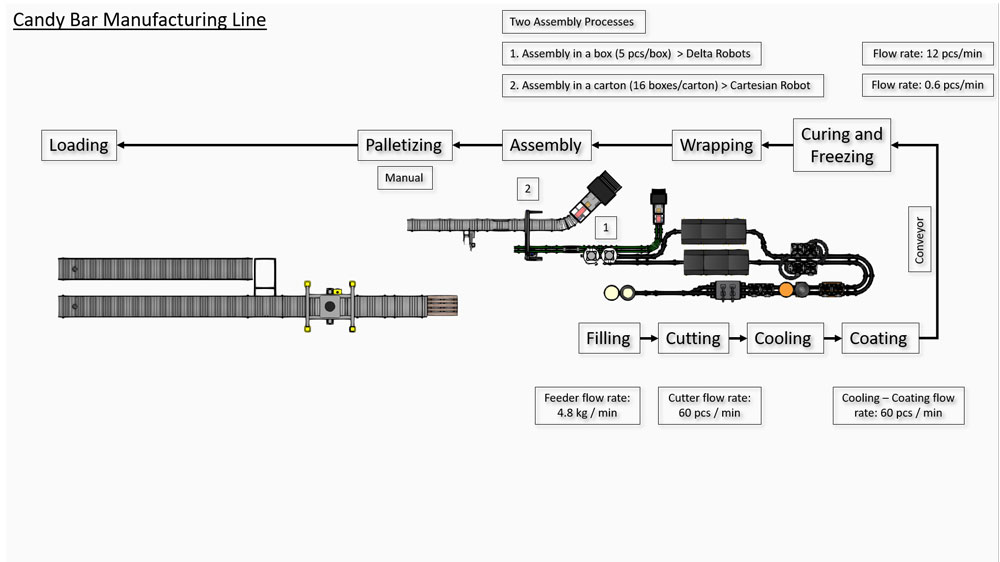
2D simulation of a chocolate bar manufacturing line.
As the name suggests, 3D simulation tools provide a more accurate and even more realistic representation of the model's subject . 3D allows you to see stocks rising and falling and material flows are clear. The simulation that is being modeled needs minimal explanation for others to understand what it is telling them.
Production simulation with visual components software
Visual Components simulations are configured with an easy, simple-to-use workflow and ready-to-use 3D models from a library.
Plug-and-play features enable faster layout design and visual process modeling capabilities allow users to manage process flows without complex programming .
Predefined simulation behaviors in components enable easier adaptation to the technology by users of all skill levels . At the same time, the open architecture and simple user interface allow easier customization in situations where it is necessary to simulate special use cases .
Types of production simulation
The simulation is performed in different ways, depending on the application and the question asked. Heat transfer, circulation and control of industrial processes can all be simulated, but require different tools to do so.
The main types of simulation are:
- Discrete event simulation
- Monte Carlo analysis
- Continuous simulation
- Agent-based simulation
The technique most often used to model manufacturing operations is discrete event simulation . This describes a process as a sequential series of events with emphasis on what the event does, when it occurs, and how it affects other events.
Monte Carlo analysis applies probabilities to computational algorithms that transform inputs into outputs. This allows the model generator to determine the most likely outcomes for a given set of input conditions.
Continuous simulation is used in flow processes. Feedback control in pumping systems is a technical example, but it could also be used to model business processes.
Agent-based simulation models how different parts of a system interact with each other. This could be thought of as “If X happens, then Y will result” inside an agent. An agent-based simulation is used in situations where there are many independent agents. Health provides many examples, as does logistics.
A closer look at discrete event simulation (DES)
An event is pre-programmed at the moment something happens in the simulation and a model is made up of a series of sequential events.
Each event is defined as an instantaneous change of state, rather than taking a finite duration, and one event can trigger or reschedule other events. This simplifies the model by avoiding the need to simulate repetitive or dynamic activities between events that have no impact on the model results .
In the model, “entities” pass through the process and are influenced by events. In a discrete manufacturing event simulation, entities can be work packages. Each batch or entity may be a different size and require different processing steps or events. It is not necessary to model the time it takes to machine each component in the batch. Instead, the event instantly changes the state of the entity from, for example, unmachined to machined. However, a record is kept of the time it would take to machine the batch, thus creating an event when machining is complete.
Manufacturing takes many forms, batch production being just one. Discrete event simulation is applicable to all types of manufacturing, from single-piece production to mixed and continuous production processes .
Visual Components introduced process modeling capabilities in November 2019 with its Discrete Event Simulation (DES)-based version 4.2. In DES, every event occurs at a certain time and the simulation records the events and reacts accordingly.
Challenges that benefit from 3D production simulation
In manufacturing, there are two main reasons to use discrete event simulation: to assess how an operation will respond to changes in input or operating conditions and to reduce the risks of reorganization or investment in new equipment . More precisely, the types of problems benefiting from simulation can be divided into:
- Identifying factors limiting throughput, especially in high-SKU environments where bottlenecks may scale with product mix
- Data-driven decision making — for example, optimizing the layout of new lines or facilities to minimize material handling and transportation distances
- Maximize asset utilization – find the highest ROI among competing approaches
- Communicate ideas – the graphical nature of 3D simulation makes problems and opportunities easily visible, even to non-technical observers
- Minimize WIP or production money – every unfinished product, every part in stock, every product in the warehouse, even every worker not fully utilized, is idle money.
How Users Benefit from 3D Production Simulation
A risk-free experiment
It is extremely difficult to experiment in a production environment. Each test or trial takes time to organize and execute and will almost always result in some degree of production downtime. If the experience involves reorganizing physical assets, this can be both costly and time-consuming.
Simulation allows for risk-free experimentation, and by not disrupting existing operations and due to the speed of model execution, it allows more options to be explored . This allows users to refine and optimize equipment modifications or configurations before implementation.
Deal more quickly with uncertainty
Many users find simulation useful in formulating plans for dealing with change . The impact of product range changes, new packaging formats or different working hours can all be assessed before being introduced. For any management team undertaking contingency planning, simulation is a powerful and effective tool.
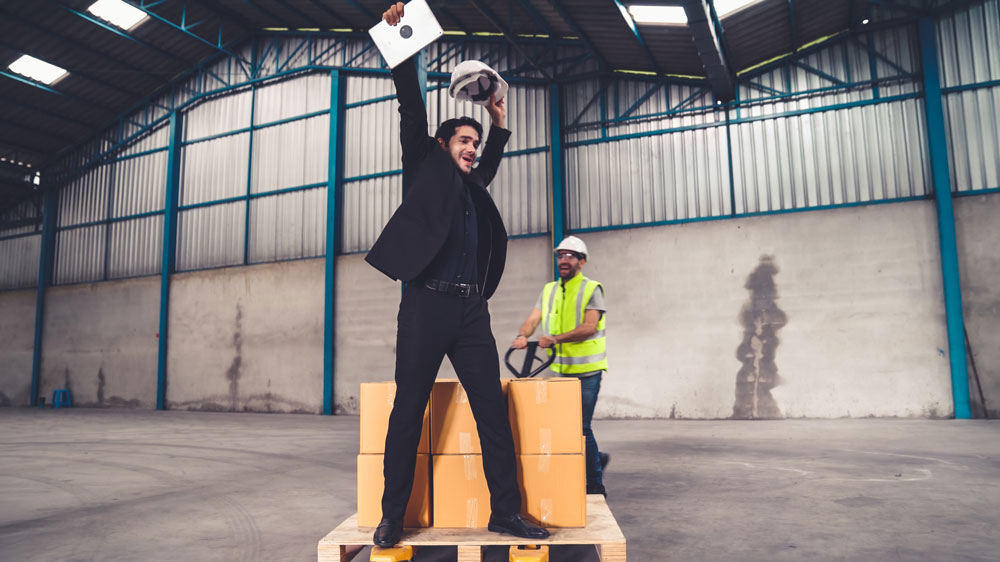
Better sell your projects internally
Another advantage of simulation is its power of persuasion . Everyone knows that images convey more than words: when these images are animated, the message is amplified several times. For anyone trying to explain concepts or sell ideas, simulation helps clarify both what is being proposed and the impact it will have.
Less risk, better ROI
Anyone who has ever wondered whether they could improve the organization of production, a factory or a warehouse will benefit from 3D production simulation. Better than building physical models or complex spreadsheets, simulation provides answers to “what if” questions. » .
It facilitates a better understanding of existing operations, supports efforts to optimize processes and implementations and communicates proposals. More importantly, it reduces the risk of trying to improve what already exists .
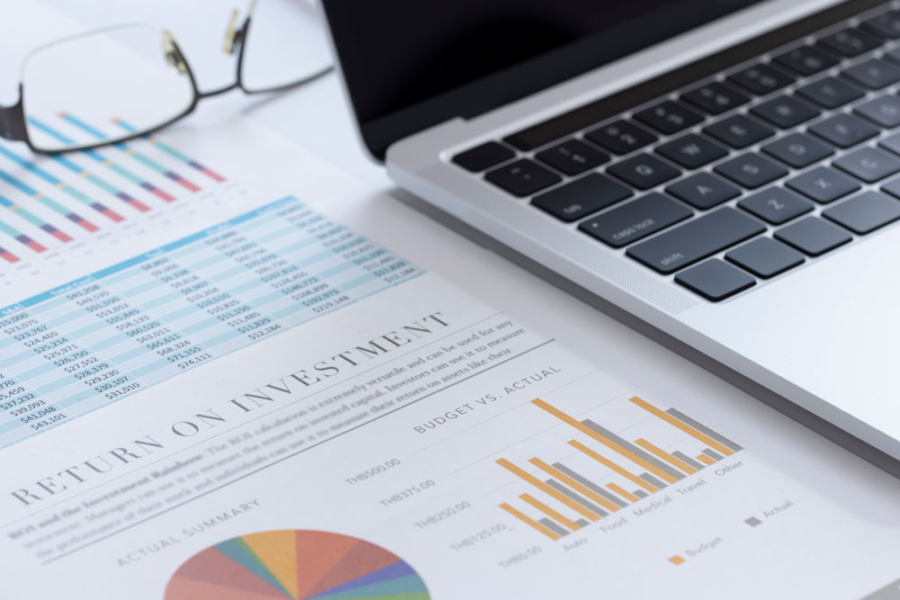
If you are looking for a tool that will help you model your production operations and determine which changes will generate the greatest return on investment, you should use 3D production simulation. Contact us to get a free demo and understand how Visual Components can help you.
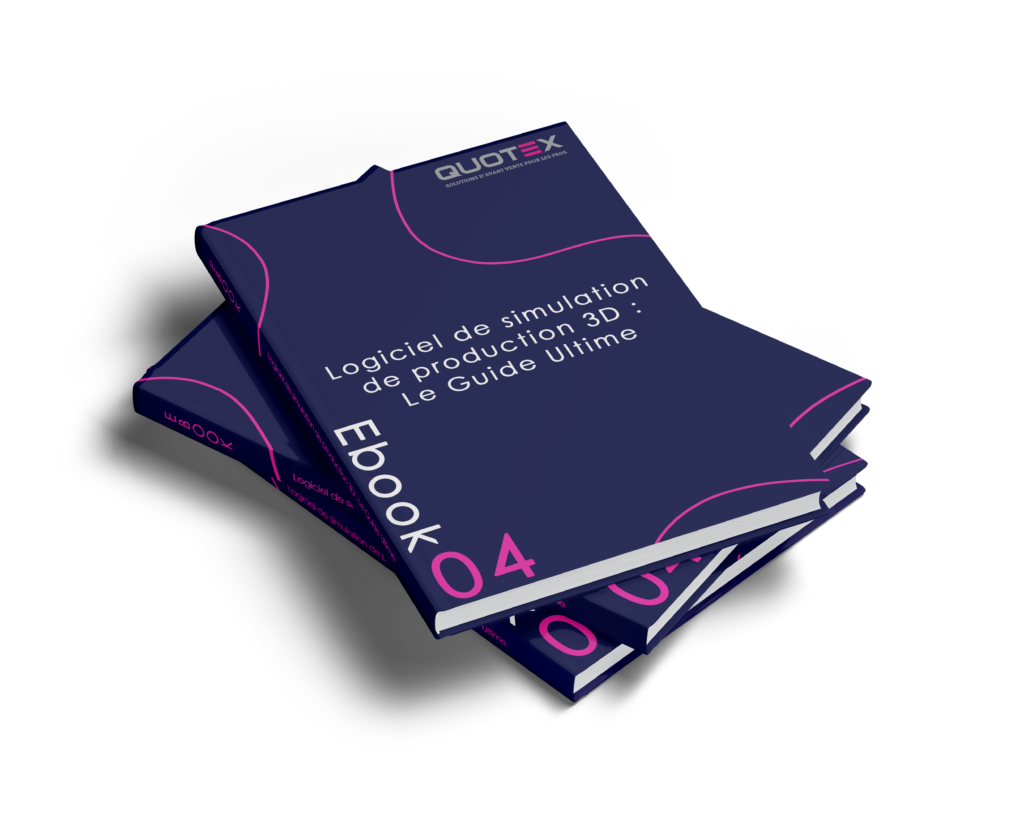