Virtual commissioning software allows faster and earlier detection of possible errors when creating or modifying an automated production line. Total engineering time and prototype waste are reduced.
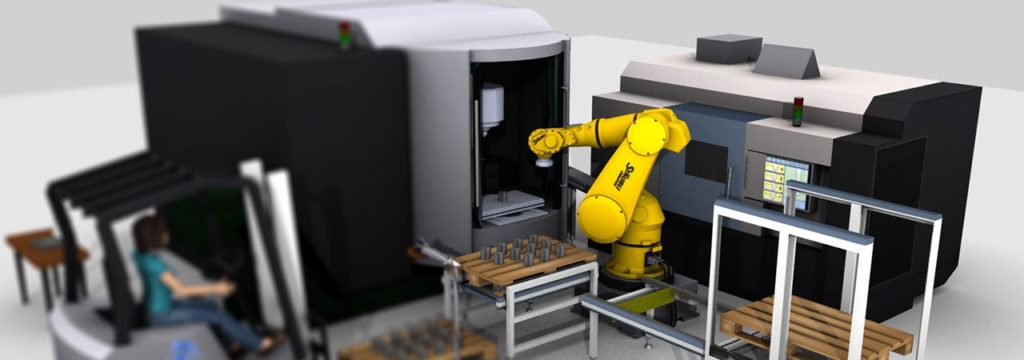
What is virtual commissioning?
Commissioning , typically the last step in the engineering process, can take up to 15-20% of the total delivery time of an automation system project .
Commissioning: mainly devoted to error correction
Unfortunately, almost 2/3 of the time spent on commissioning is spent fixing software errors (1) , because the control software typically only undergoes proper integration testing once all hardware was purchased and assembled .
Because commissioning is typically accomplished in near-impossible time frames, developing custom control software is often rushed , even though debugging it at this stage can damage the hardware.
Resolving these issues earlier in the process can thus save a lot of time and effort , which could in turn be spent on optimizing or delivering the project earlier.
Virtual commissioning: to prevent errors
Virtual commissioning provides a solution to move a significant portion of commissioning tasks to an earlier phase of the project, away from the critical path . During virtual commissioning, a simulation model of the system is created to replace the real plant. The virtual factory is then connected to the real control system, so that simulation can be used simultaneously with procurement and assembly to verify the design and test the control system. This allows for faster detection of possible errors.
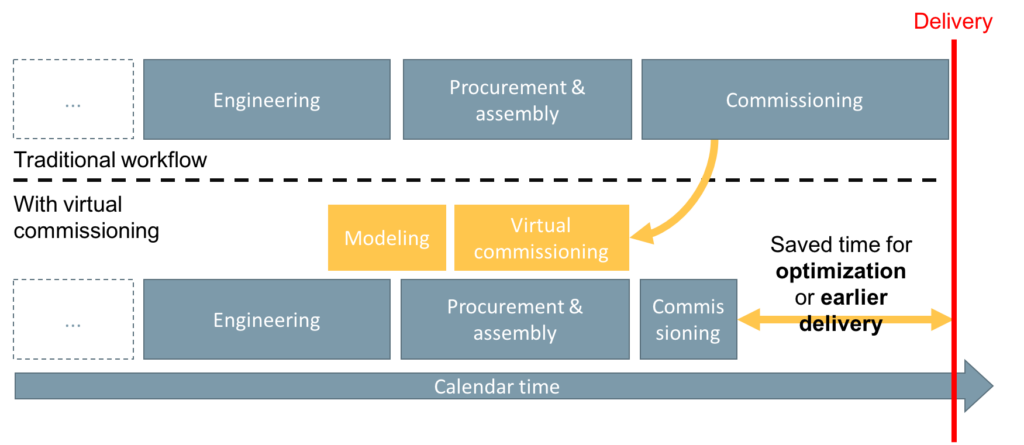
Figure 1: Engineering project with and without virtual commissioning.
Virtual commissioning provides a solution to move a significant portion of commissioning tasks to an earlier phase of the project, away from the critical path.
You can also apply virtual provisioning to a single subsystem, such as a work cell or a single machine at a time, depending on the use case . Simulated and real machines can also be used in parallel (a method known as hybrid commissioning), allowing the process to gradually move from virtual to real.
The simulation responds to control system outputs and provides simulated inputs as the real system would. This allows engineers or even the customer to see how the system actually behaves through interactive 3D visualization , not just the variables in the control programs .
Compared to common more primitive testing of control software, interactive visualization is a big advantage, as such tests are usually performed simply with code or by manually setting inputs or outputs based on the programmer's understanding of the machine real. Additionally, such tests are difficult or impossible to run in reality without risking damage to machines or personnel can be run in simulation , resulting in better software quality and, above all, increased security.
The Benefits of Virtual Commissioning
There are many benefits to using virtual commissioning throughout the engineering process: total engineering time and prototype loss are reduced, errors are less costly to correct because they are detected earlier and the quality of the software is considerably improved .
As an example, in a field study conducted with a small PLC controlled system with 17 sensors and 10 actors (active components), virtual commissioning was found to increase quality (defined as meeting requirements ) by 37% to 84%, while simultaneously reducing actual time-to-service by 75% and total time-to-market by 15% (2).
By creating visualizations of the proposed system early in the quoting phase and then building a progressively more comprehensive simulation model during design, you can also achieve much greater synergy between engineering teams and project stakeholders simply because that an interactive 3D simulation conveys ideas and behavior far better than a stack of design documents ever can.
This will help reduce miscommunication of design goals, desired system behavior, and required information between engineering teams and the customer.
Commissioning and virtual simulation software
Virtual commissioning places great demands on the simulation software. It must support accurate simulation of a variety of systems, from simple sensors and actuators to transportation systems, robotic applications, and MES-level control of production facilities. Additionally, the time spent creating simulation models should be as small as possible to achieve the goal of reducing the overall engineering effort.
This requires an easy-to-use software package and allows your engineers to leverage their existing knowledge and skills . Visual Components family of 3D production simulation products was created to do just that.
The simulation model must accurately emulate the behavior of the real system , but it is also crucial that the same control system and control software can be used with both the simulation and the real automation system. In practice, this means that the same hardware or software PLC or robot controller selected for the real system must also be used for virtual commissioning.
However, any modification to the control software should be avoided so that automation engineers can use the familiar controllers, associated software, and development workflow to develop the control software and then be able to connect it to the simulation engine.
(1) Liu Z, Diedrich C, Suchold N. Virtual commissioning of automated systems [Internet]. INTECH Open Access Editor; 2012 [cited July 13, 2015]. Available here.
(2) Reinhart G, Wünsch G. Economic application of virtual commissioning to mechatronic production systems. Eng. Prod. November 8, 2007;1(4):371-9
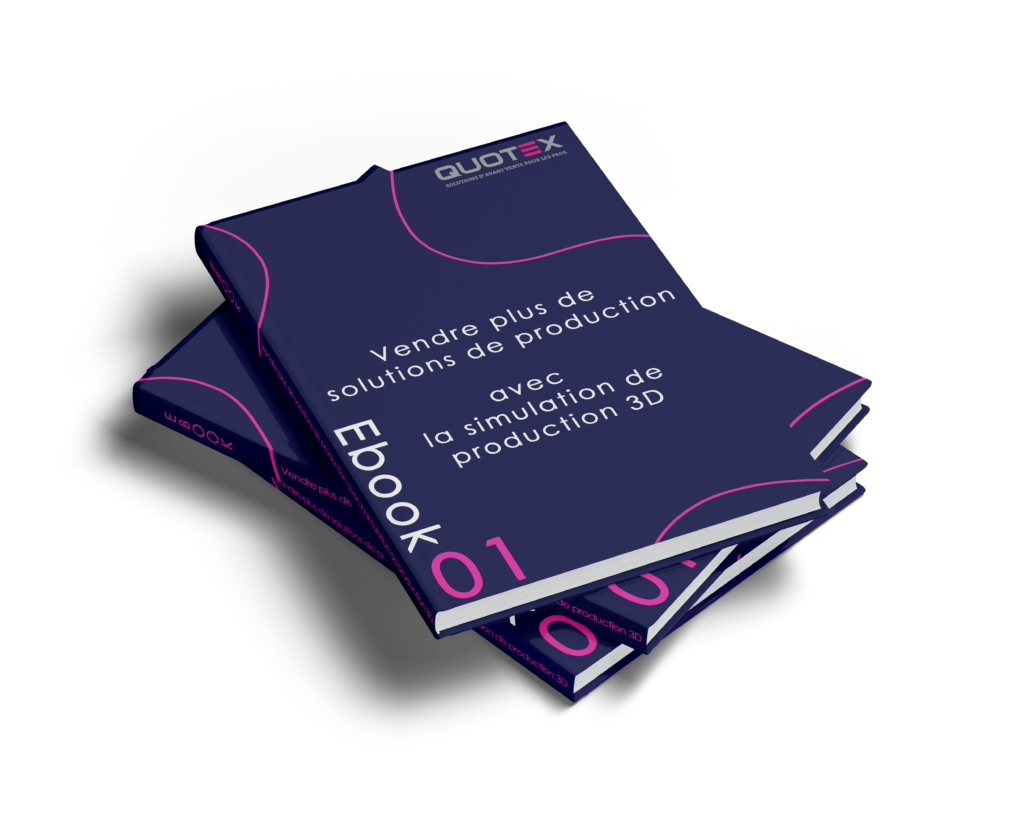