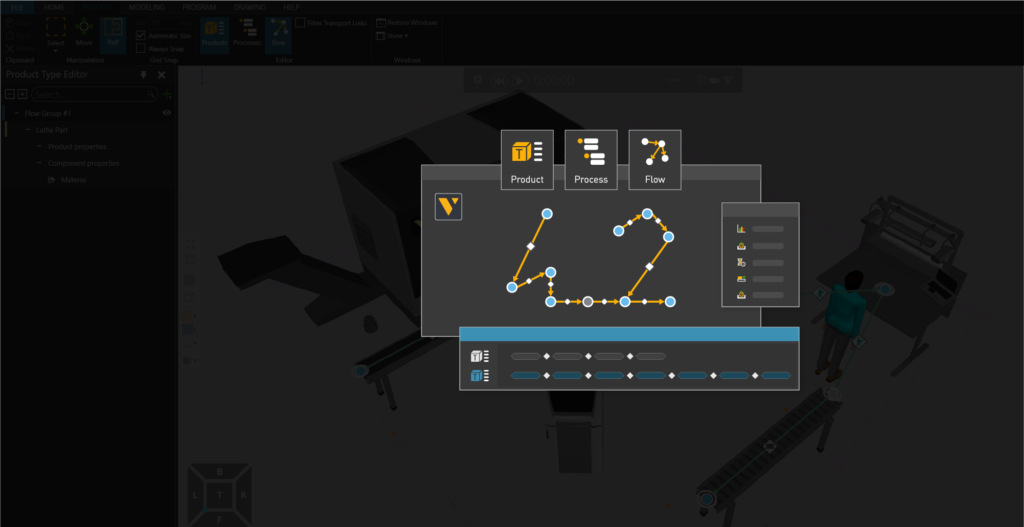
In this article, we will briefly introduce you to the concept and functionality of process modeling, a major new feature in Visual Components 4.2.
A major new feature that was introduced in Visual Components 4.2 is Process Modeling: a fast, simple, and visual way to define and manage products, processes, and process flow in your implementations. This new feature offers many important benefits, such as simplifying layout creation and simulation setup, streamlining workflow modeling and simulation, and improving simulation performance.
To help you better understand workflow modeling and simulation, and the concepts and features behind process modeling in Visual Components, here is a short introductory article.
Process Modeling
Does the workflow in process modeling resemble the way it is done in the real world? The answer in 5 steps:
1: Design your layout.
2: Define the products, their visualization, their structure and their properties.
3: Define processes: machines, workstations, inventories and buffer zones using task instructions.
4: Define flow by creating process sequences that products must complete.
5: Run the simulation, collect KPIs, make necessary changes to achieve your goals.
Does the workflow in process modeling resemble the way it is done in the real world? The answer in 5 steps:
1: Design your layout.
2: Define the products, their visualization, their structure and their properties.
3: Define processes: machines, workstations, inventories and buffer zones using task instructions.
4: Define flow by creating process sequences that products must complete.
5: Run the simulation, collect KPIs, make necessary changes to achieve your goals.

In order to visually follow what we are saying, follow each step in more detail, using the reference example of a small machining and painting cell.
Design your layout
The first step in the workflow is to design or configure your production layout. It can be created using full electronic library components and/or CAD data, which you can import directly into the software. Equipment must be placed in the correct positions and orientations, but also stations, pedestrian and buffer zones, tools and spacing requirements must all be considered in the design.
For our reference example, an implementation with 2 processes: machining and painting was created. A robot to load/unload parts into the lathe and a human to manually perform painting on a workbench. Conveyors have also been added to facilitate the transport of products between processes.
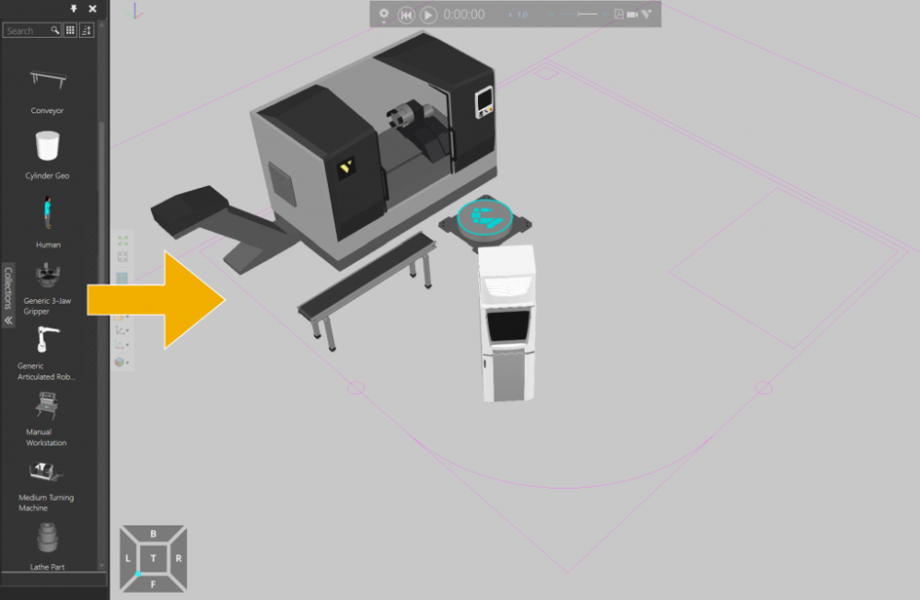
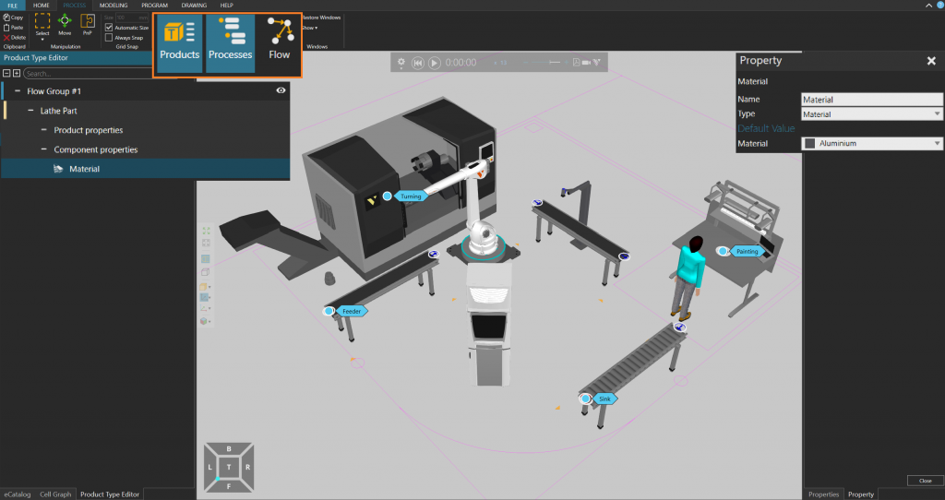
Define Products
A product is an entity that goes through a certain process in an implementation. Products that undergo processes can be defined in this phase. In the Product Type Editor, you can configure and manage the following:
1: Product flow group: which is the grouping of product types sharing the same production flow. Let's call the first flow group "Flow Group #1".
2: Product type name: It can be a brief description of the product, such as cylinder, car tire, engine plate, etc. In this case, the product is a “Lathe Part”, so let’s keep that name.
3: Product Properties: These may include parameters such as dimensions, weight, material, etc. We want to specify that this tower part is “Aluminium”.
4: 3D Product Geometry: A 3D geometry can be imported and selected as a product like in this example, where we added “Lathe Part” as an external CAD file.
Define Processes
A process is a representation of a machine, a work phase, an inventory, a buffer zone or another production step. In process modeling, a process is expressed as a set of instructions, which assign certain behaviors to a product. Processes are created from instructions using the Process Editor. With routines and instructions, machines can be configured to behave like their real-world counterparts, such as opening and closing machine doors, processing times, product geometries changing with processes, attaching parts , etc.
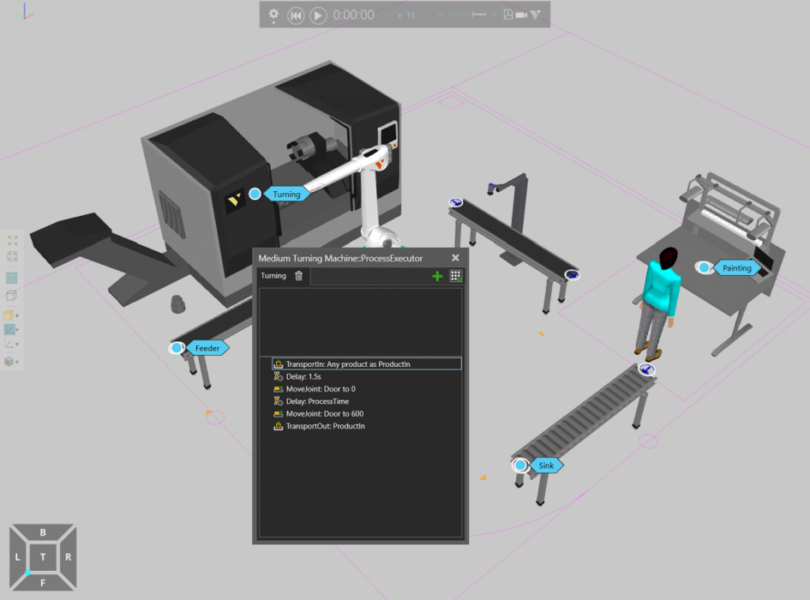
Before defining processes, it is important to consider how products should evolve during production. In our reference cell, our products undergo two different processes
Process 1 is turning, where products are machined in a machine.
Process 2 is painting, where the products are painted gray.
Now we need to define the production steps for each process. For process #1, the following steps are specified:
1: A robot picks up the incoming product from the conveyor and transports it to the machine. The TransportIn statement is used to express this step, and it appears as the first step in the Process Executor.
2: Next, a short delay is programmed so that the robot arm can exit the machine before the process begins. A delay of 1.5s is added.
3: Before the turning process begins, it is best to ensure that the machine doors are tightly closed. The MoveJoint instruction to move the door joints to close it takes care of this.
4: Now the machine needs to start the turning process, so another delay instruction is added but as ProcessTime this time.
5: Once the turning process is complete, another MoveJoint is used to make the machine doors open so the robot can retrieve the part.
6: Once the doors are opened, the robot transports the product out of the machine, using TransportOut.
The production steps of the painting process can be defined following a similar workflow. Once processes are defined with process modeling, production steps can be managed via the ProcessExecutor action panel and adjustments can be easily made.
Process editor showing production steps of process #1 – Turning
Define feeds
A flow is the sequence of processes that products follow in a factory. In process modeling, products are defined into groups based on the path they follow during simulation. These groups are called flow groups. Using the Process Flow Editor, you can define flow groups and the production flow for each product. You can also define transportation links, which determine how products are transported between two processes during the simulation. A resource, such as a human, robot, or AGV, can be assigned to each transportation link, which then transports products based on its capabilities.
In our reference cell, we only have one flow group (we previously named it “Flow Group #1”), because all products follow the exact same path. Before you define the route for this flow group in the Process Flow Editor, you need to plan the route it should take:
1: First of all, a source to produce products in the system is necessary. To do this, simply import a “feeder” from the electronic catalog and add it at the start of the first conveyor.
2: The first process that the products undergo is turning. The robot picks up the products at the end of the first conveyor and places them into the machine for this process.
3: Then the robot grabs the products from the machine and places them on the adjacent conveyor, which transports them to the paint.
4: Once the products reach the end of the conveyor, the human resource collects them and transports them to the workbench for painting.
5: Once the products are painted, the human transports them to the exit conveyor.
6: So that the finished products leave the simulation at the end of this conveyor, simply add a “Sink” process here.
Once the route is planned, flows can be defined easily in the Process Flow Editor, using your mouse to create links by selecting/clicking on processes and resources in the 3D world.
Run the simulation
When your model is configured, it is ready for simulation. Basic media controls can be used to play simulations, collect KPIs, make changes, and export in a variety of formats.
Simulation playback with workflow view enabled
In this article, we briefly introduced you to the concepts and capabilities of process modeling, a major new feature in Visual Components 4.2. Process modeling presents a simple but powerful way to manage processes and workflow in your operation. It also provides an improved user experience by simplifying layout creation and simulation configuration, streamlining workflow modeling and simulation, and improving simulation performance.
If you'd like to learn more about process modeling or other new features in Visual Components 4.2, contact us to schedule a free, personalized web demo!