Visual Components OLP : Programmation hors-ligne de robots
Le logiciel de programmation de robots hors ligne de nouvelle génération basé sur la puissante technologie de Delfoi Robotics.
Maximisez le potentiel de vos robots grâce à une solution de programmation rapide, précise et sans erreur.
Acronyme: OLP (Offline Programming) – PHL (Programmation Hors-ligne)
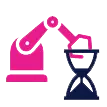
Minimisez les temps d'arrêt du robot
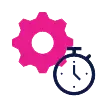
Réduisez le temps de programmation
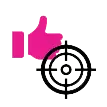
Précision supérieure et reproductible
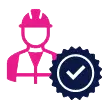
Augmentez la sécurité dans l'atelier
Le logiciel de PHL tout-en-un
Un seul logiciel pour tous les processus
Programmez vos robots pour divers processus industriels tels que le soudage, le traitement ou la pulvérisation à l’aide d’un seul logiciel.
Soudage
Visual Compontents OLP couvre des procédés tels que le soudage à l’arc, le soudage Tig, le soudage au laser, le soudage par points et le rivetage.
Process
Couvre des processus tels que le meulage, le polissage, le lustrage, le ponçage, l’ébavurage, l’ébarbage, la découpe au plasma et la découpe au laser.
Peinture
Couvre des procédés tels que la peinture humide, le revêtement par pulvérisation, la pulvérisation thermique et la pulvérisation à froid.
Cela vous permet de repérer les problèmes cachés et de minimiser les risques d’investissement.
Comptatibles avec les principales marques de robots industriels
Marques de robots
17 marques de post-processeurs dans un seul produit… Et d’autres seront ajoutés à l’avenir !
Contrôleurs
Plus de 40 versions de contrôleurs de robots, y compris les anciens robots et les modèles plus récents.
Programmez vos robots indépendamment de leur marque ou de leur type. Éliminez la nécessité d’utiliser plusieurs logiciels pour différentes marques. Visual Components OLP prend en charge 17 des marques de robots les plus courantes.
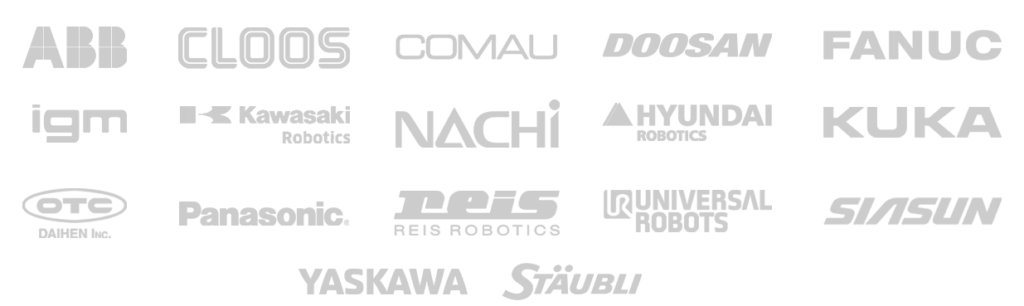
Des programmes rapides, fiables et précis
Générez rapidement des programmes dans des cellules robotisées virtuelles, où que vous soyez dans le monde.
Laissez le logiciel valider et optimiser les programmes avant de les envoyer en production afin d’éviter des erreurs coûteuses.
Programmation en un clic
Programmez vos robots en quelques clics
Optimisation du temps
Sauvegarder vos programmes pour les réutiliser à tout moment pour d’autres projets.
Découvrez les différents processus gérés par Visual Components OLP en vidéo
Différents processus OLP
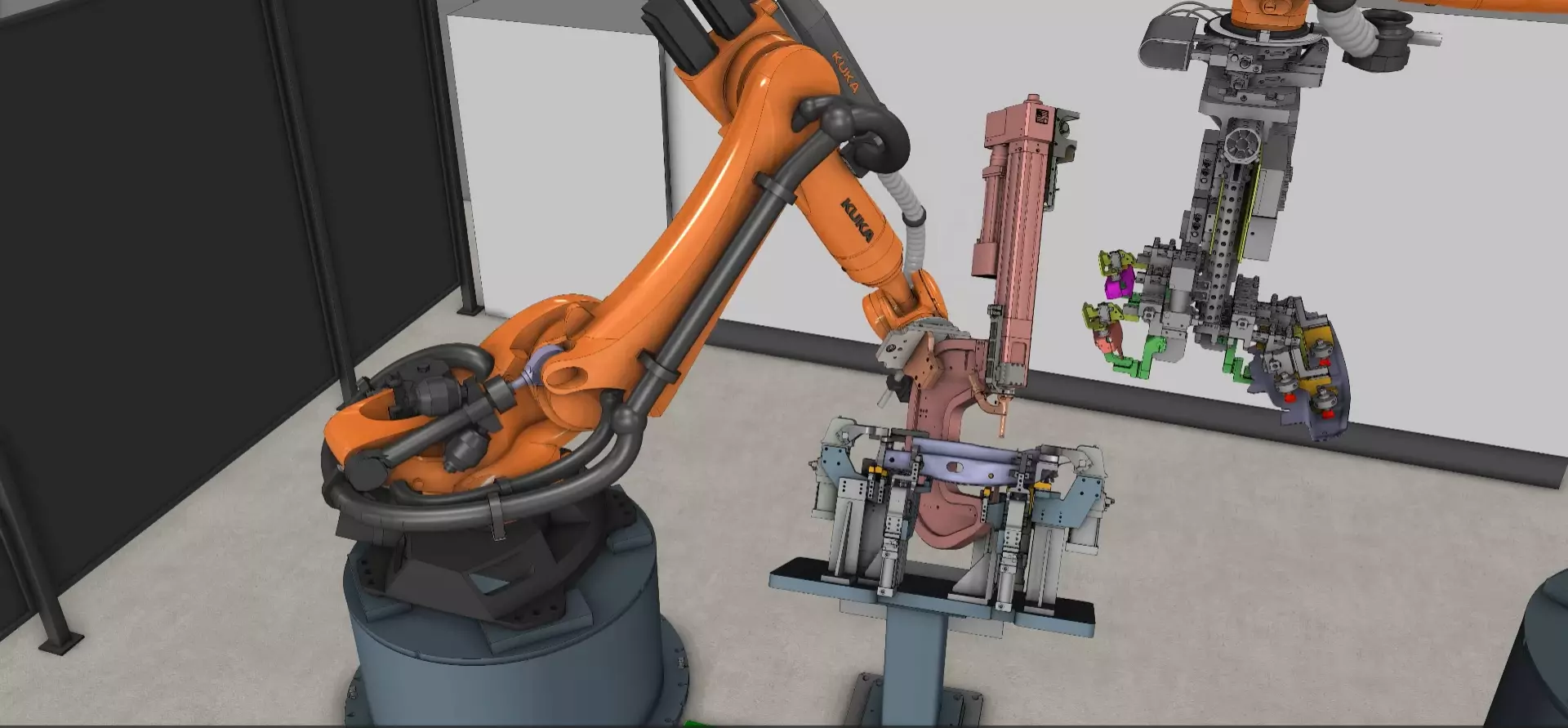
0:11
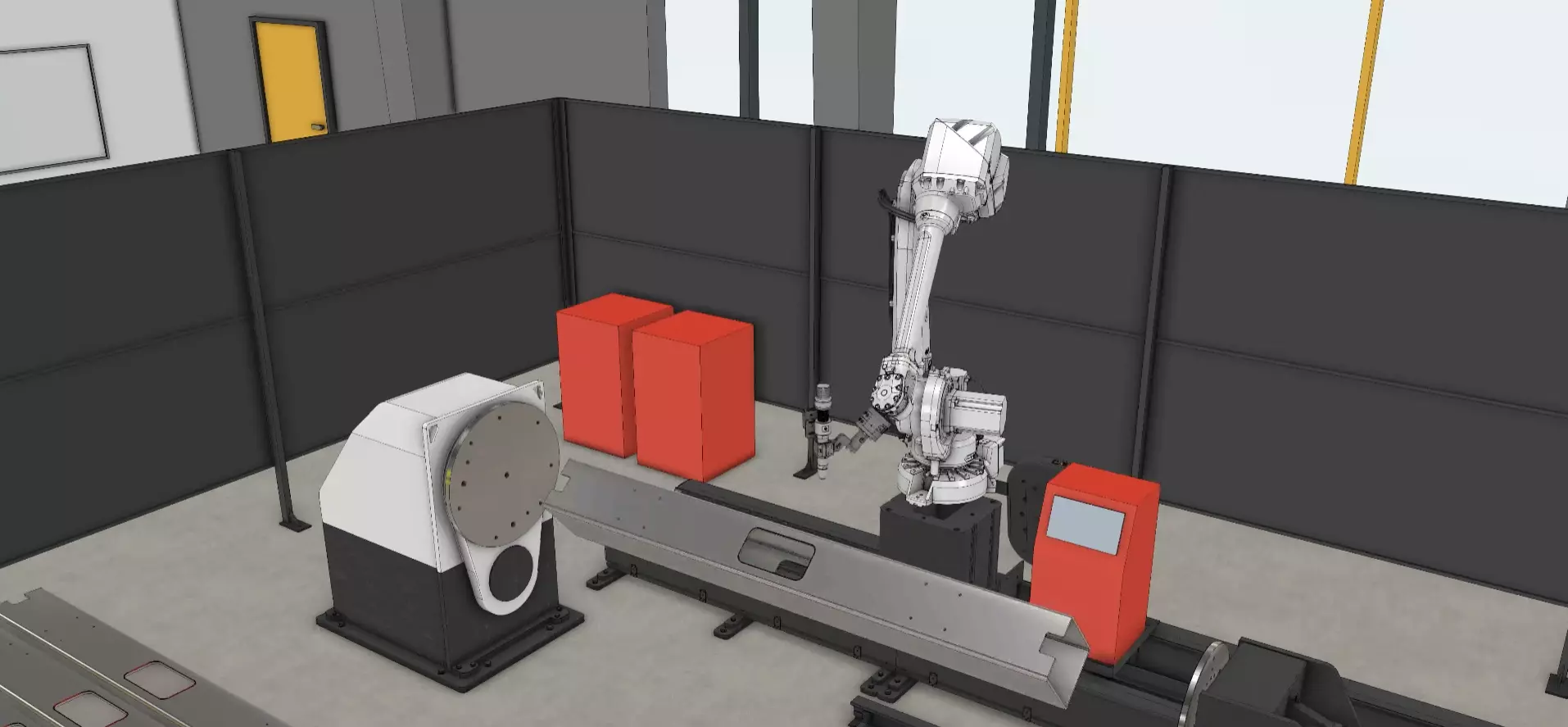
0:11
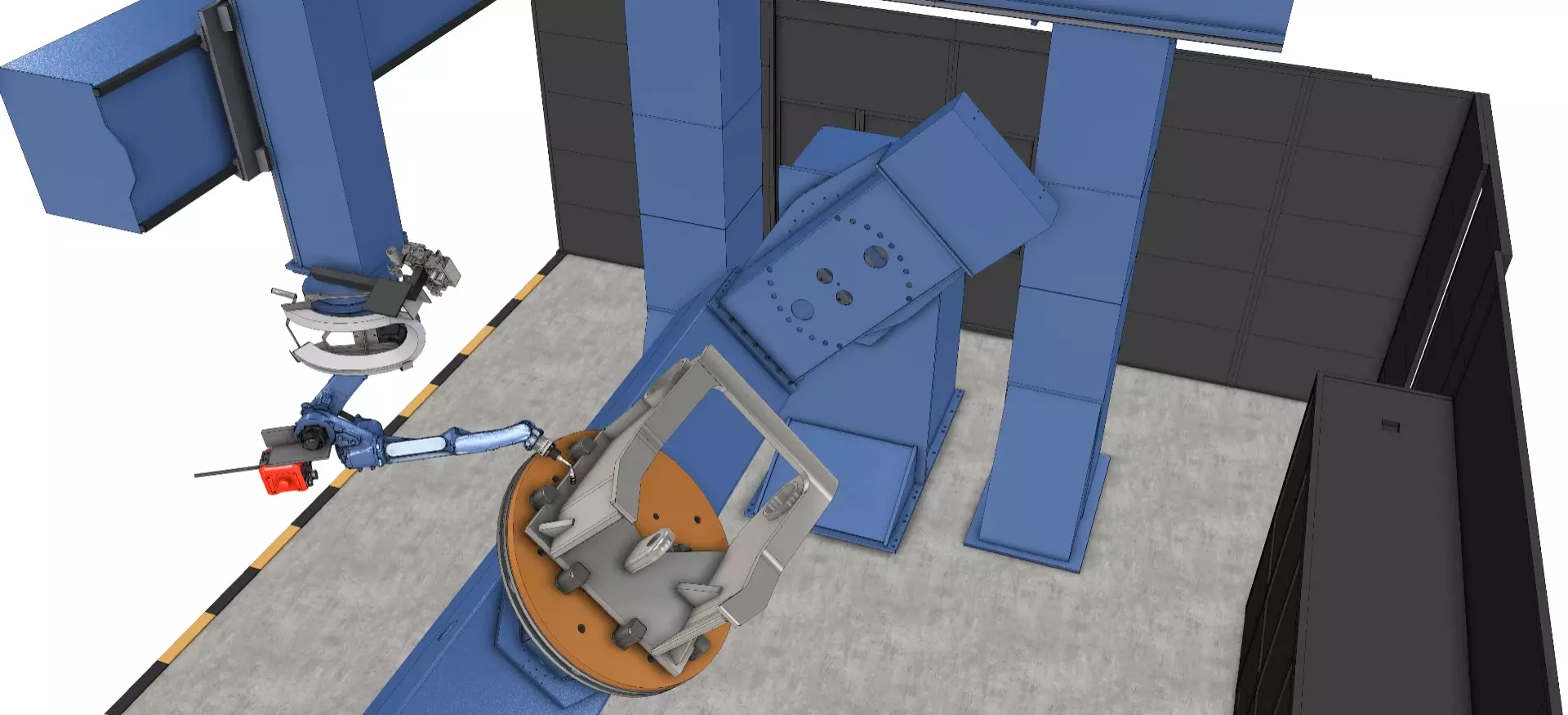
0:10
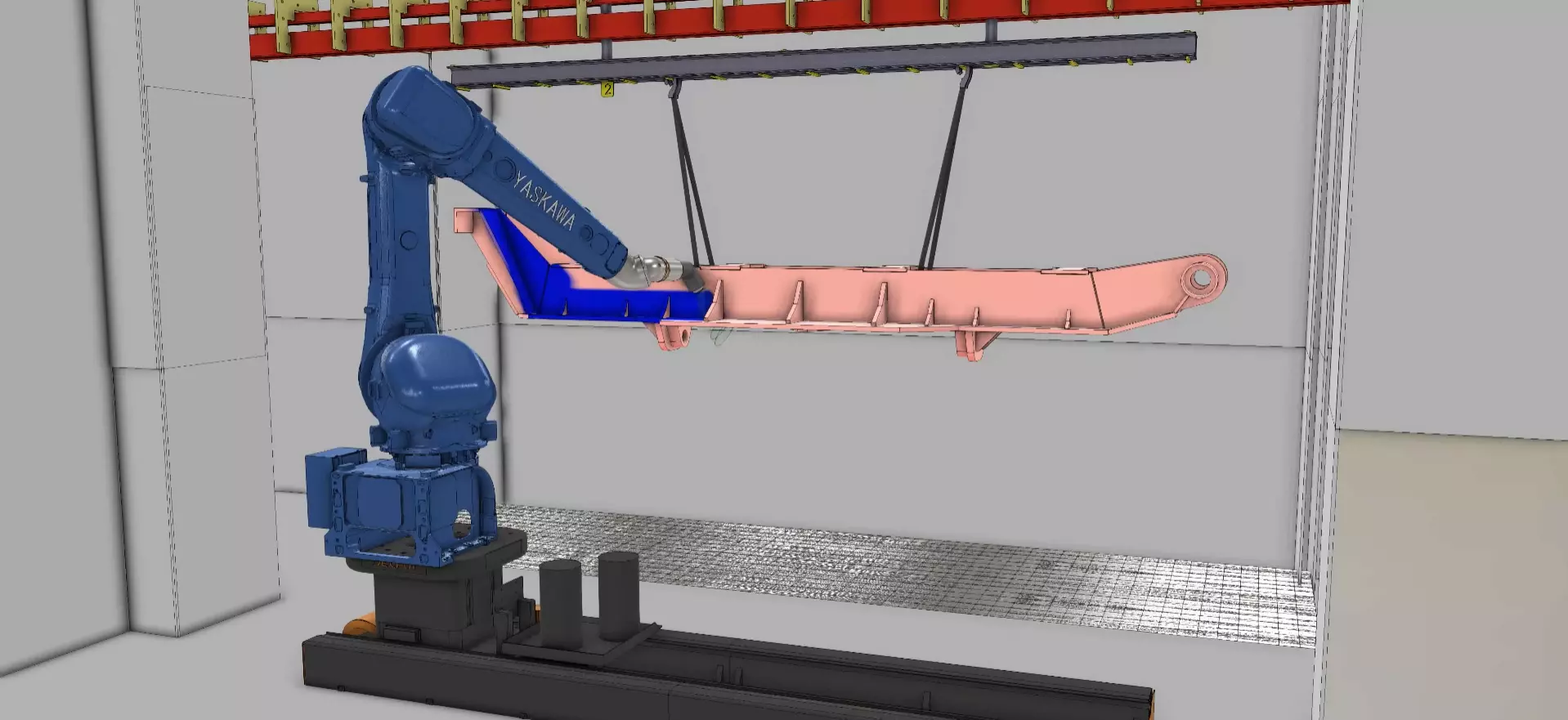
0.14
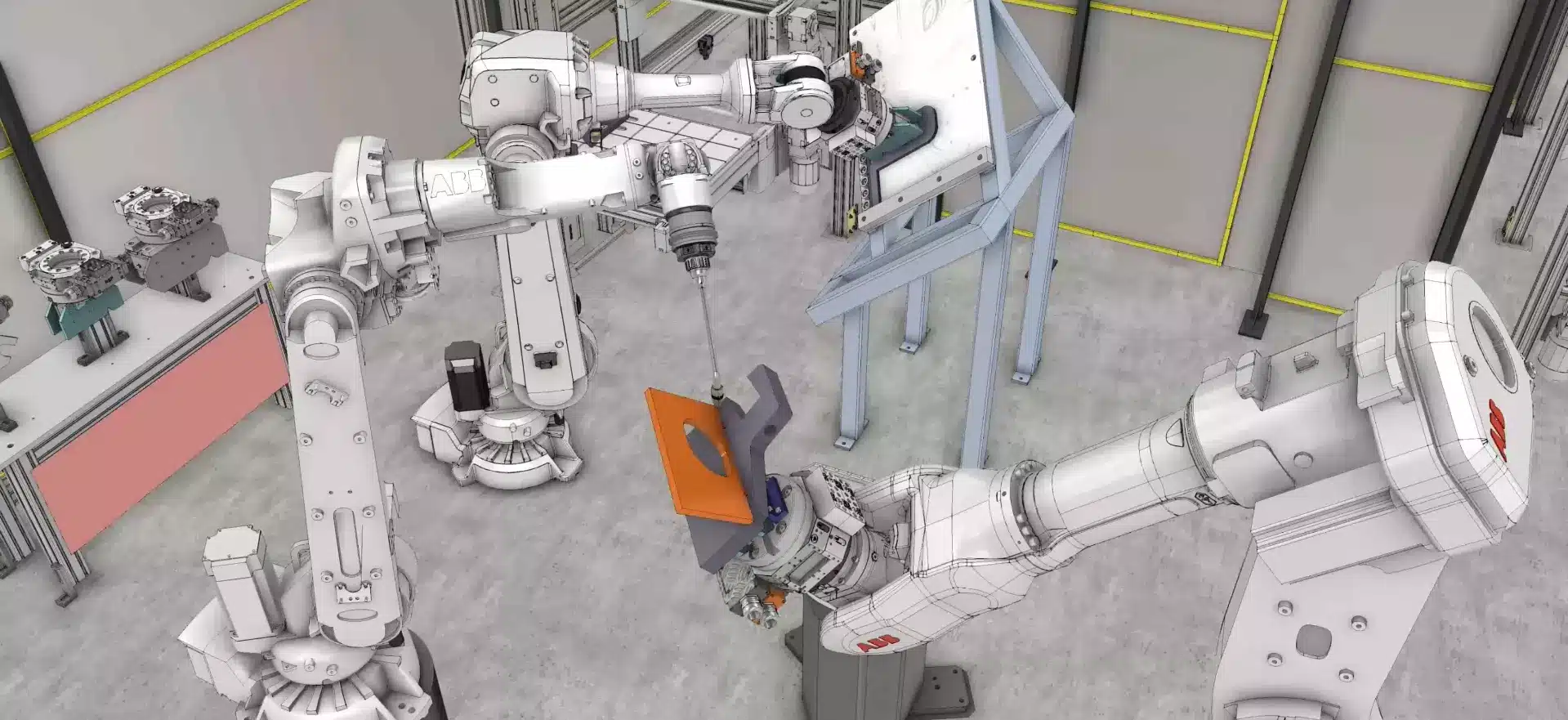
0.14
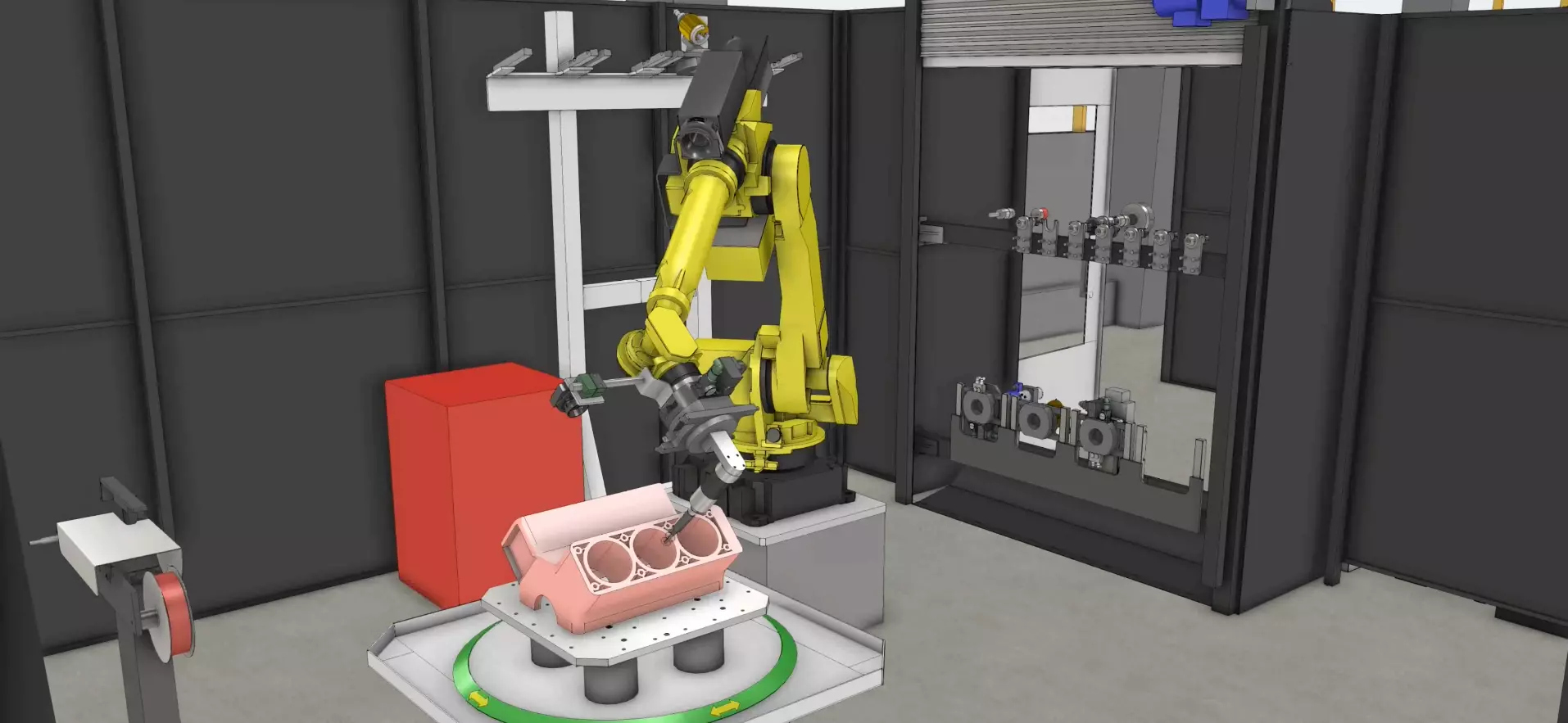
0.11
Lors d’une visio de 30 minutes, notre intégrateur-expert VISUAL COMPONENTS fera l’état des lieux de vos pratiques en matière de conception de lignes et estimera le temps que vous pourrez gagner grâce à Visual Components
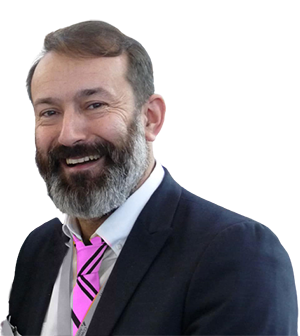
Questions fréquentes sur la programmation hors ligne de robots
La programmation hors ligne des robots (PHL ou OLP en angalis) est une méthode de génération de programmes de robots dans un logiciel informatique (environnement virtuel) basé sur des données de CAO en 3D.
Une fois le programme de robot généré et vérifié dans le logiciel, il peut être téléchargé sur le robot physique.
Imaginons qu’un robot soit programmé pour souder une pièce circulaire sur une pièce métallique. Le robot doit déplacer la torche de soudage dans un arc 3D autour de la circonférence de la pièce, tout en maintenant une orientation précise par rapport à la surface.
Vous pouvez le faire en enseignant des points à l’aide d’un pendentif, mais vous aurez besoin d’un grand nombre de points et cela prendra beaucoup de temps. L’écart entre les torches variera très certainement, de même que l’orientation de la torche. De plus, la cellule du robot ne sera pas disponible pour la production tant que vous n’aurez pas terminé la programmation. Cet arrêt peut durer des jours, voire des semaines. Avec la PHL, il est beaucoup plus facile de produire le programme du robot. Importez un fichier CAO de la cellule de soudage dans le logiciel OLP et montrez la trajectoire que vous voulez que la torche prenne. Une fois terminé, le logiciel génère le programme du robot et vérifie qu’il n’y a pas de collisions potentielles. Une fois vérifié, le programme est téléchargé dans le contrôleur du robot, exécuté une fois à faible vitesse pour une double vérification, et la cellule est prête à reprendre le travail.
Chaque application robotique est un candidat pour la PHL ; la seule condition est de disposer de modèles numériques de la cellule de travail, des pièces, de l’outillage et des fixations. (Aujourd’hui, tout est conçu en CAO, ce qui ne devrait pas poser de problème.) Toutefois, les avantages sont d’autant plus importants que les trajectoires des robots deviennent plus complexes et que davantage de points doivent être enseignés.
En gardant ces points à l’esprit, voici quelques-uns des meilleurs cas d’utilisation de la PHL :
Soudage – l’accès et l’orientation sont des défis particuliers que la PHL permet de relever, et les cordons de soudure complexes peuvent nécessiter un grand nombre de points.
Revêtement (peinture) – comme pour le soudage, l’orientation est importante, de même que l’épaisseur de la peinture et la distance d’éloignement, tout en veillant à ce que toutes les zones puissent être atteintes et peintes de manière optimale.
Dépose – de nombreuses opérations d’assemblage nécessitent la dépose de perles d’adhésif longues et complexes : La PHL permet de créer les trajectoires d’outils rapidement hors ligne avec une qualité constante.
Traitement (surface) – les applications telles que le microbillage et l’ébavurage nécessitent souvent des trajectoires longues et complexes qui requièrent un grand nombre de points.
Applications d’assemblage (sans gabarit) – les mouvements de préhension et d’insertion nécessitent un contrôle précis de l’orientation du préhenseur, ce qui est possible à un niveau plus élevé avec la PHL.
Applications de manutention – La PHL permet au programmeur de déterminer la distance la plus rapide entre deux emplacements, ce qui n’est pas toujours le chemin le plus évident.
Découpe – La découpe au plasma, au laser ou au jet d’eau peut fonctionner pour les pièces standard, mais pour les géométries complexes, des robots sont nécessaires avec des modèles de découpe précis qui peuvent être générés avec la PHL
Les fabricants qui utilisent le logiciel OLP font état de nombreux avantages :
Pas de temps d’arrêt du robot
Le temps de programmation peut être réduit jusqu’à 80 % et l’utilisation du robot augmentée jusqu’à 95 %, ce qui stimule la productivité du programmeur et réduit les temps d’arrêt des cellules.
Temps d’installation rapides
Moins de temps est nécessaire pour lancer un nouveau produit en production – la programmation se fait simultanément plutôt que séquentiellement.
Sécurité accrue
Réduction du risque d’accidents et de blessures
Qualité supérieure et reproductible
Les programmes des robots sont mieux optimisés (temps de cycle plus courts, précision et cohérence accrues), ce qui se traduit par une qualité de production supérieure et reproductible.
Agnostique à la marque du robot et au processus
Quelle que soit la marque du robot ou le type de processus, le logiciel OLP avancé peut couvrir toutes les applications.
Finies les surprises
Les modifications de dernière minute des fixations et de l’outillage sont évitées.
Bien que tout fabricant utilisant des robots puisse bénéficier de la PHL, les gains les plus importants sont observés lorsque les lots sont de petite taille et que les cycles de production sont courts.
Le problème est que, lors de la programmation sur le robot, les changements et les réglages fréquents réduisent la disponibilité et les heures de fonctionnement.
Toutefois, avec Visual Components OLP, les programmes sont testés virtuellement et téléchargés sur les robots pendant que les aspects physiques de la cellule (fixations, pinces, etc.) sont modifiés. La prudence suggère de faire passer le robot par un cycle à faible vitesse pour vérifier l’absence de collisions, après quoi la cellule est prête à redémarrer la production.
En outre, tout problème lié à la conception dans la documentation ou les modèles est identifié à l’avance et peut être communiqué aux autres équipes et résolu sans perte de temps de production.
L’alternative à l’utilisation de l’OLP consiste à programmer directement sur le robot. Cette solution pose au moins trois problèmes :
1. Risque de retard du projet et de coûts supplémentaires
2. Problèmes de sécurité
3. Perte de capacité de production
Le risque de retard du projet est important lorsque la programmation est effectuée sur le robot. À ce stade, tous les outils et montages ont été conçus, construits et installés. Les convoyeurs ou autres dispositifs de manutention sont en place et les pièces sont prêtes à être utilisées. Ce n’est que maintenant que le programmeur peut commencer à enseigner des points au robot.
Il est presque certain que des problèmes surviendront. Le robot ne peut peut-être pas atteindre un endroit particulier, les pièces sont peut-être au mauvais endroit ou le temps de cycle visé n’est peut-être pas réalisable.
Dans tous ces cas, la seule solution consiste à redéfinir les points problématiques de la cellule. Inévitablement, cela retarde le début de la production, parfois de plusieurs semaines, et entraîne des coûts supplémentaires importants.
L’apprentissage des points à l’aide d’un pendentif oblige souvent le programmeur à entrer dans la cellule : c’est parfois le seul moyen de voir où va l’outil ou de vérifier s’il y a des collisions. Le fait de mettre le robot en mode “apprentissage” devrait garantir sa sécurité, mais il existe toujours un risque de mouvement inattendu, soit du robot lui-même, soit de l’un des autres mécanismes de la cellule.
Enfin, pendant que le programmeur apprend des points à l’intérieur de la cellule de travail, le robot ne peut rien faire d’autre. Il s’agit d’un temps improductif jusqu’à ce que le programmeur ait terminé et que le programme soit éprouvé. Et même les meilleurs programmeurs ont tendance à sous-estimer le temps nécessaire à la tâche !