Dans cette étude de cas, nous allons vous montrer comment KONE, un leader mondial dans l’industrie des ascenseurs et escaliers mécaniques, utilise Visual Components pour améliorer la productivité et réduire les délais de commercialisation.
Avantages clés :
- Prise de décision plus rapide et communication plus efficace avec les parties prenantes
- Gain de temps lors du processus de développement
- Temps de mise sur le marché réduit
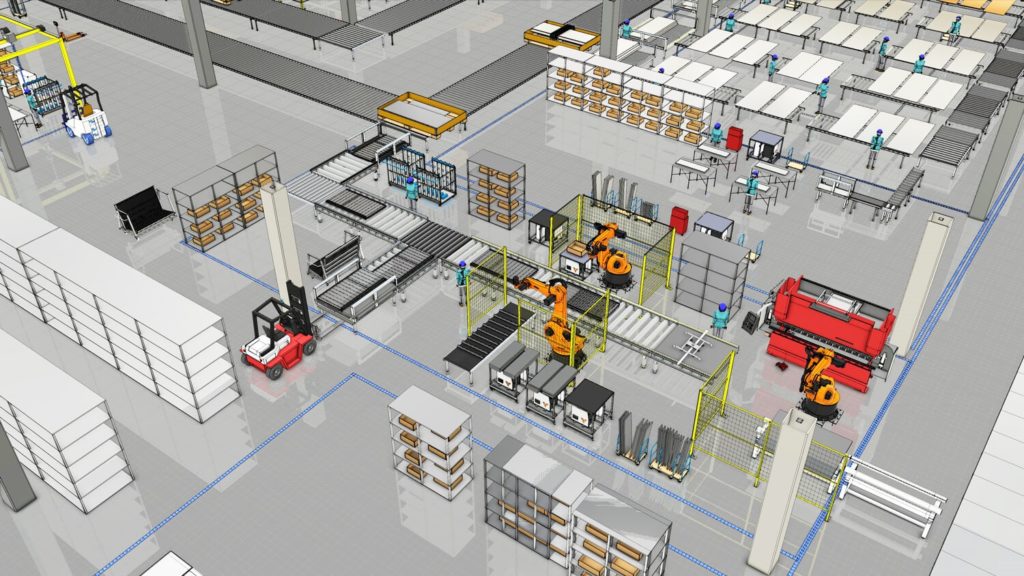
À la recherche d'un outil d’implantation et de simulation 3D
Avec 14 usines, 55000 employés et un chiffre d’affaires de 8,9 milliards d’euros en 2017, KONE est un leader mondial de l’industrie des ascenseurs et escaliers mécaniques. L’entreprise finlandaise fournit des ascenseurs, des escaliers mécaniques et des portes automatiques de bâtiment, ainsi que des solutions pour la maintenance et la modernisation, qui ajoutent de la valeur au cycle de vie de tout bâtiment.
Au fur et à mesure que KONE s’est développée au fil des années, la demande de ses usines a également augmentée.
« Il y a un peu plus d’un an, nous avons constaté la nécessité de modifier la façon dont nous communiquions avec nos parties prenantes sur l’implantation des cellules d’assemblage », a déclaré Miikka Ahola, responsable des solutions de fabrication de KONE pour KSU Manufacturing Solutions.
« Les nouveaux processus de production sont complexes et difficiles à expliquer via CAD et Excel, en particulier avec la robotique. »
Miikka et son équipe ont décidé qu’il était temps de chercher une solution qui pourrait non seulement les aider à planifier et à concevoir de nouvelles solutions de production, mais aussi améliorer leur communication avec les partenaires pendant l’implantation et le développement du processus.
« Nous étions en train de cartographier des solutions potentielles pour la simulation et l’implantation de nos usines et nous voulions avoir des plans 3D, car ils aident beaucoup à visualiser l’implantation et les besoins en espace », a déclaré Miikka.
« Lors de la recherche de fournisseurs potentiels, nous avons trouvé le logiciel Visual Components. »
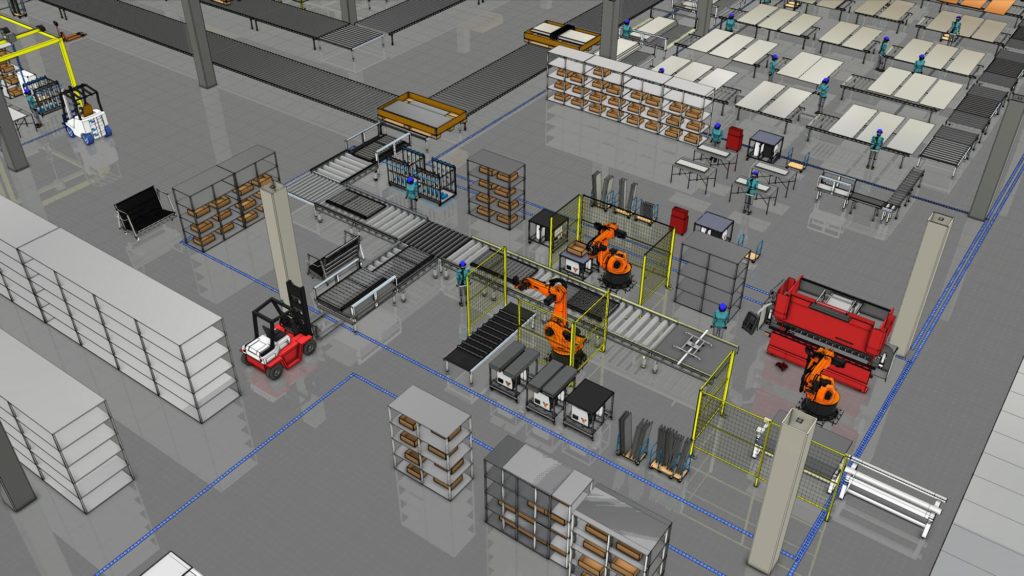
Après avoir mené une évaluation des logicielles potentielles, Miikka et son équipe ont décidé d’aller de l’avant avec Visual Components.
« L’utilisation de Visual Components a été beaucoup plus facile par rapport aux autres produits que nous avons évalués. C’était très important pour nous », a déclaré Miikka.
Une équipe de planification et de développement mondiale
L’équipe mondiale de développement et de planification de KONE a son siège à Espoo, en Finlande. C’est une grande équipe internationale qui s’étend à l’ensemble des 14 usines.
« Nous avons une équipe de développement internationale responsable du développement des technologies et des processus, qui est soutenue par des équipes locales dans chaque usine, avec leurs propres ingénieurs de développement », explique Miikka.
« La majeure partie du développement des lignes, des processus et des technologies est effectuée par l’équipe internationale, tandis que l’implantation et le réglage fin des solutions se font en coordination avec les équipes locales. »
Tous les nouveaux projets de R&D sont d’abord examinés par l’équipe internationale. Ils examinent les investissements, la technologie et la faisabilité des projets dans un premier lieu, puis transfèrent le produit de la R&D à la production et supervisent la mise en œuvre dans les usines de KONE.
« Nous travaillons au milieu, en veillant à ce que tous les plans et investissements soient réalisés, et que tout est prêts afin de démarrer la production », explique Miikka.
Integration de Visual Components dans le processus de planification
Pour Miikka et son équipe, il était facile d’incorporer Visual Components dans leur processus de planification.
« En règle générale, nous utilisons Visual Components dans les premières étapes des projets d’implantation de nouveaux produits. Cela nous aide à présenter à nos partenaires une image claire du type de cellule ou de ligne de production ainsi que de l’espace nécessaire pour atteindre les objectifs de production », explique Miikka.
Les nouveaux projets d’investissement au sein de l’équipe de développement international commencent généralement par la création de maquettes de lignes ou de cellules.
« Nous commençons par définir ce que nous allons faire et élaborons une maquette qui comprend toutes les lignes et cellules d’assemblage nécessaires, mais qui pourrait ne pas être définie en fonction des besoins spécifiques du produit. Cela nous aide à définir l’espace nécessaire pour commencer », explique Miikka
Une fois qu’ils ont choisis un design qui selon eux, fonctionnera, ils se déplacent pour créer l’implantation.
« Nous commençons par affiner les cellules individuelles et à améliorer l’ergonomie », explique Miikka.
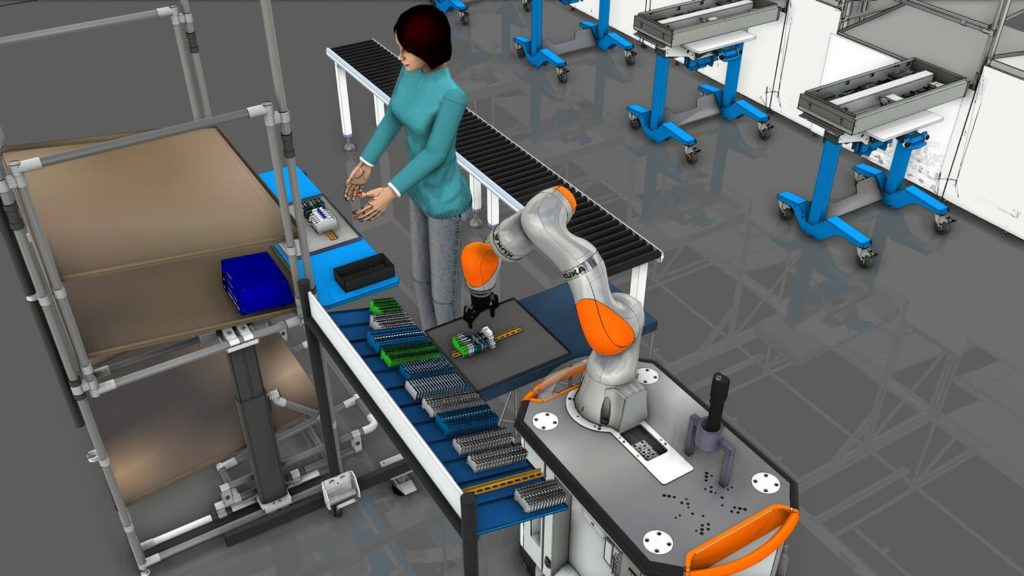
Ensuite, ils simulent le flux de production, validant les calculs de production et l’espace nécessaire, et recherchent des opportunités d’optimisation et de réduction des coûts. Avoir un outil visuel pour communiquer ces compromis avec les partenaires a été particulièrement utile pour Miikka et son équipe.
« Nous pouvons montrer visuellement à nos partenaires dans la R&D, le développement de produits, la qualité et les opérations comment les changements dans la conception peuvent réduire les coûts de main-d’œuvre et d’équipement », explique Miikka.
Après avoir obtenu l’approbation de la direction pour poursuivre le projet, ils utilisent des fichiers d’exportation de Visual Components, tels que des vidéos de simulation, des PDF 3D et des dessins 2D, pour faciliter la communication avec les usines lors de l’implantation et du déploiement.
Travailler avec les fournisseurs pour développer la catalogue électronique
Pour Miikka et son équipe, il était facile d’incorporer Visual Components dans leur processus de planification.
« En règle générale, nous utilisons Visual Components dans les premières étapes des projets d’implantation de nouveaux produits. Cela nous aide à présenter à nos partenaires une image claire du type de cellule ou de ligne de production ainsi que de l’espace nécessaire pour atteindre les objectifs de production », explique Miikka.
Les nouveaux projets d’investissement au sein de l’équipe de développement international commencent généralement par la création de maquettes de lignes ou de cellules.
« Nous commençons par définir ce que nous allons faire et élaborons une maquette qui comprend toutes les lignes et cellules d’assemblage nécessaires, mais qui pourrait ne pas être définie en fonction des besoins spécifiques du produit.
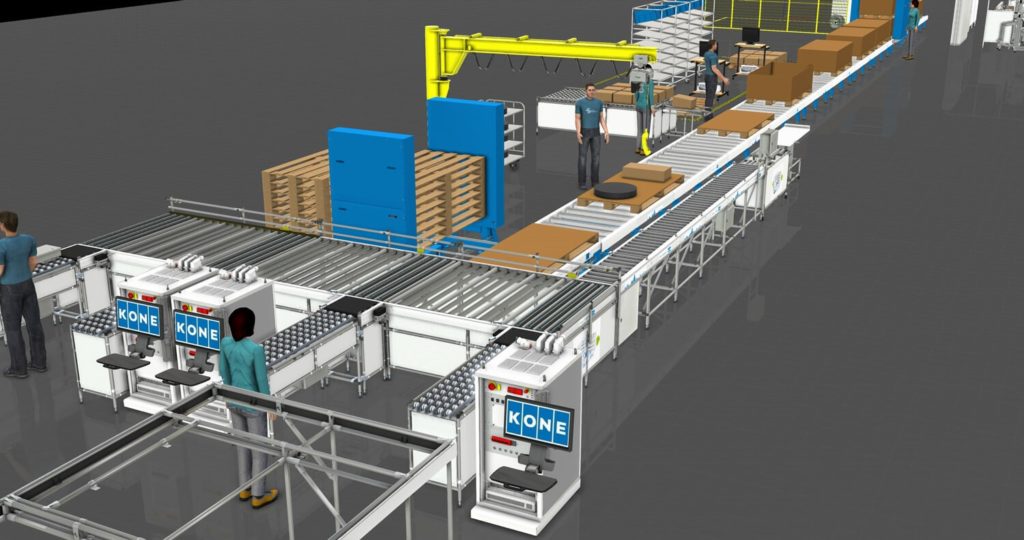
Cela a donné à Miikka et à son équipe des implantations de référence qu’ils peuvent utiliser pour démarrer facilement de nouveaux projets, mais leur ont également permis d’évaluer de nouveaux équipements et solutions développés par l’intégrateur et ont amélioré leur collaboration lors de la planification de nouveaux projets. »
«Dans cet arrangement, les deux parties en bénéficient», explique Miikka.
Grâce au partenariat de KONE avec leur intégrateur de système, Miikka et son équipe disposent d’un flux constant de composants et d’implantations qu’ils peuvent utiliser dans leur processus de planification du développement. Ils sont également mieux informés des dernières technologies et processus de production.
« Nous obtenons une bibliothèque de composants et d’implantations régulièrement mise à jour, pour nous aider dans notre planification, et ils ont des opportunités de projets dans nos usines du monde entier », explique Miikka
Amélioration de la productivité, réduction des délais de commercialisation
Pour Miikka, le plus grand avantage que le logiciel Visual Components apporte à KONE est le gain de temps sur le processus de développement. Il facilite une prise de décision plus rapide et une communication plus efficace avec les partenaires. Cela les aide également à réduire les délais de commercialisation.
« Visual Components nous aide à démarrer le processus de développement de la production bien plus tôt qu’auparavant et à réduire les délais critiques de commercialisation », explique Miikka.
Miikka et son équipe jonglent avec beaucoup de projets simultanés, de la planification de nouvelles usines en Inde aux tests de futurs concepts technologiques. Visual Components les aide à être plus productifs afin de pouvoir répondre à la demande croissante de produits KONE.
À l’avenir, Miikka espère étendre l’utilisation des Visual Components à toutes les usines du monde.
« Nous prévoyons de mettre en place Visual Components dans nos usines, afin que les ingénieurs de développement locaux puissent l’utiliser pour mettre en évidence les changements, les idées et suggérer des améliorations allégées avec les simulations », explique Miikka.